Safety is a top priority in the aerospace industry. That’s why it takes such a long time for new manufacturing methods to reach the shop floor, even though companies are constantly on the look-out for new ways to cut high material costs and reduce component weight. The high-tech aerospace industry’s reluctance to wholeheartedly embrace the promise of 3D printing therefore comes as little surprise – and only the most tenacious efforts are likely to convince them otherwise. One company that is busy promoting the benefits of 3D printing is Spanish supplier RAMEM, which specializes in the design and manufacture of mechanical and electromechanical devices. Headquartered in Madrid, RAMEM produces a wide variety of parts, including aerospace components with complex geometries and sophisticated technical requirements, as R&D manager Silvia López-Vidal explains: “We do a lot of high-mix, low-volume work in this field, which is why we have long been interested in additive manufacturing, or AM. When it comes to reducing weight, cutting down the number of subassemblies and slashing costs, AM offers far more potential than conventional methods.”
Ready for take-off
But RAMEM is interested not only in the opportunities AM offers, but also in the strategic benefits, says López-Vidal: “AM will eventually make the leap into industrial-scale production in the aerospace sector, too. So we’re making sure we’re prepared for that moment by building up the necessary expertise in advance.”
RAMEM’s engineers always have AM in the back of their minds, constantly analyzing all the parts they produce to determine whether AM could add value to the manufacturing process. A rake is one example of a part that offers particular promise. Rakes are used in engine development to take high-precision readings of pressure and temperature to help engineers assess engine performance. Mounted directly in the engine’s air flow, they must be made to very high standards in order to withstand the extreme temperatures and tensile and compressive loads. A rake is a highly complex part that must conform to precise dimensional requirements and feature a smooth, aerodynamic surface in order to deliver accurate measurements.
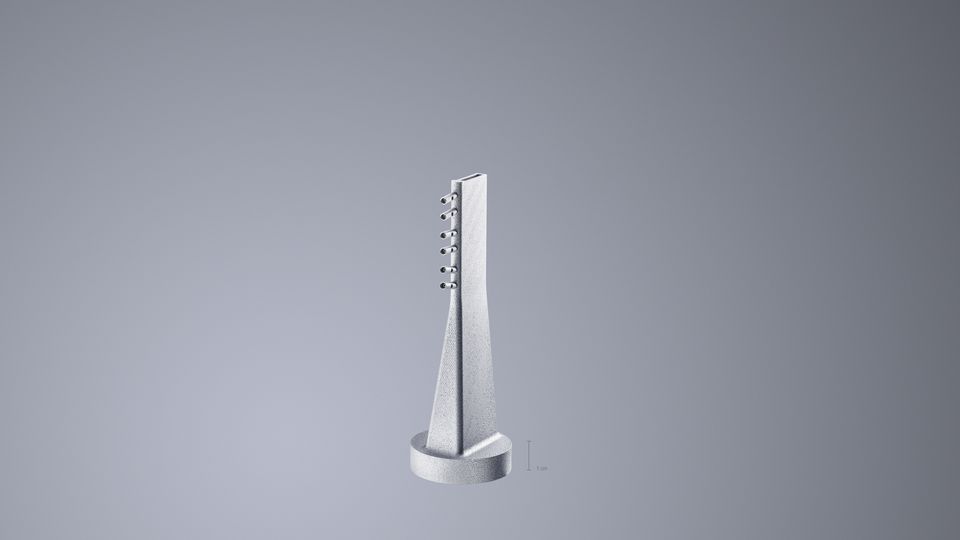
TRUMPF has 3d printed a rake by the Spanish Aero Supplier RAMEM, which is used for the engine developments of airplanes.
The result: costs slashed by almost 80 percent
© TRUMPF GmbH
Challenging parts made to the highest standards
Rakes consists of four components that must be painstakingly milled, assembled manually and then welded individually. At their core are several internal tubes that serve as channels. These are welded to the sampling points known as ‘Kiel heads’ with a wall thickness of <0.3 millimeters. The channels are inserted into the rear of the elongated body of the rake and welded into place to the Kiel heads. The body of the rake is then sealed with a cover plate. “Those delicate channels must be inserted with maximum precision,” says López. “If just one of the welded Kiel head is out of position, the whole rake has to be scrapped. The Kiel heads have dimensional tolerances of +/- 0.05 millimeters and feature a narrow, continuous opening at the end of which the flow sensors are integrated.”
The engineers at RAMEM immediately saw that the delicate rakes were perfect candidates for 3D printing. The challenge was to design them in a way that would be compatible with AM. This task was tackled by Prodintec, a RTO that specializes in redesigning parts for additive manufacturing. They succeeded in reducing the number of components from four to one. Yet the results were still disappointing, says López-Vidal: “The rakes were deformed during production, and the printing process deposited powder and other solids in the narrow channels. What’s more, the 3D printing process wasn’t meeting requirements – neither for dimensional accuracy nor for a smooth, pore-free rake surface.”
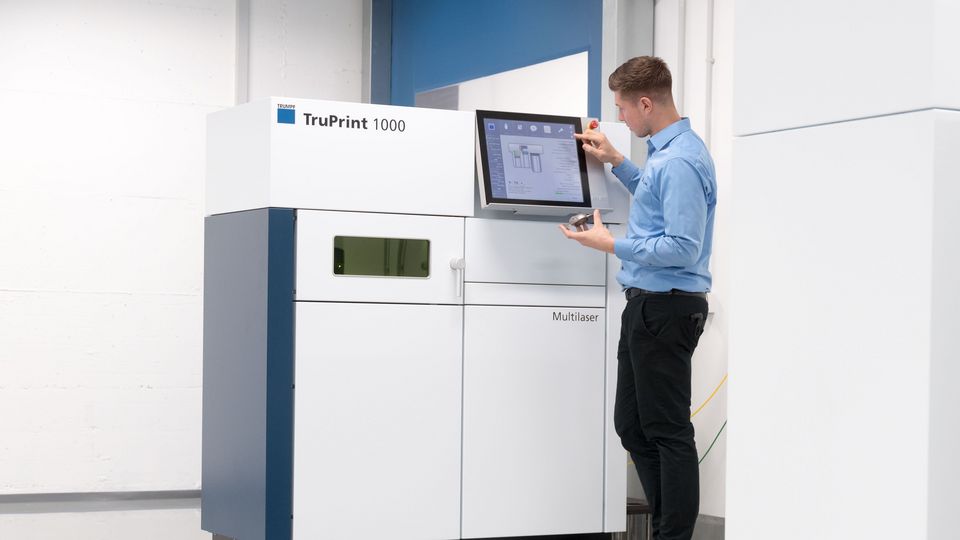
The optimized rake was printed with the TRUPrint 1000 by TRUMPF.
© TRUMPF
A breakthrough with the first prototype
But Silvia López-Vidal and her team refused to be discouraged by this setback. At FORMNEXT 2017, they explained the problems they were facing to Julia Moll, Project Manager Additive Manufacturing, and her team of TRUMPF colleagues. “The TRUMPF developers were confident they could solve our problems with their lasers and powder,” says López-Vidal. So, armed with the CAD drawing from Prodintec, the TRUMPF team set out to find a solution.
“The biggest challenge in the printing process was the issue of part orientation,” says Julia Moll. “We had to align the part in such a way that we could print it without support structures, because we wouldn’t have been able to attach those to the highly fragile Kiel heads or anywhere inside the part. We also had to rule out any risk of thermal distortion. That wasn’t easy because the rakes are so thin-walled.” The team used a TruPrint 1000 to print the parts. This 3D printer has a 200-watt laser that can be used to generate remarkably delicate structures from the powder bed.
The results checked all the right boxes right from the very first rake prototype, says Moll: “A 3D scan enabled us to demonstrate that it had the required level of geometric accuracy, and using micrographs we established a surface density of 99.95 percent.” But the experts were keen to get even more accurate information, so they sent the prototype for a CT scan at YXLON, a developer and producer of X-ray and computed tomography inspection systems. The company verified the uninterrupted continuity of the channels and the size of the pores. The TRUMPF experts also automatically ascertained and checked over 40 measurements inside the part. All the results came back positive: the channels were clear and all the requirements were met by the very first prototype, including the required level of dimensional accuracy and the stipulated pore size of less than 100 microns.
Costs slashed by almost 80 percent
Julia Moll was delighted with what the TRUMPF team had achieved: “Redesigning the part has cut throughput times and reduced the amount of material we use by around 80 percent. All in all, the decision to 3D-print the rakes has reduced our overall costs by around 74 percent. That’s a whole order of magnitude in this industry.” The practical part of the process is now underway, and Silvia López-Vidal is optimistic: “The key is to stay up to speed with this new method and keep decision-makers up-to-date with the opportunities offered by additive manufacturing. Rakes are yet another example of just how much potential AM has to offer. But the aerospace industry is a challenging market, and it will take us a while to convince our customers to use additive manufacturing for structural components and other key assemblies. Nevertheless, we and other big suppliers are steadily expanding our strategic expertise in AM methods – and that’s a clear sign of how confident we are that this technology will ultimately succeed.