Paula kuschelt sich gemütlich an ihre Mutter und lauscht gebannt ihrer Gute-Nacht-Geschichte. Sie liebt Bücher und ganz besonders liebt es sie, wenn ihr jemand vorliest. Dass die Fünfjährige heute Worte und sogar Musik hören kann, war kurz nach ihrer Geburt nicht vorstellbar. Denn Paula wurde gehörlos geboren. Die Stimmen ihrer Eltern und Geschwister, die Geräusche ihrer Umgebung hörte sie nicht. Eins von 1.000 Kindern kommt in Deutschland wie Paula ohne Gehör zur Welt. Ihre Familien stehen dann vor der Entscheidung: Hörimplantat oder Gebärdensprache. Paulas Eltern wollten ihrer Tochter ein möglichst barrierefreies Leben ermöglichen und entschieden sich für ein sogenanntes Cochlea-Implantat. Also ein Hörgerät, das in die Cochlea, die Hörschnecke, implantiert wird.
Komplexes System
Diese Hörsysteme bestehen aus einem Audioprozessor mit Mikrofon und dem Implantat selbst. Den Prozessor tragen Patienten hinter dem Ohr. Er erfasst Geräusche in der Umgebung und passt die Töne und Lautstärke an, reduziert störende Hintergrundgeräusche und verstärkt feine Töne. Das Implantat setzen Chirurgen unter der Haut ein. Es übernimmt die Funktion der Sinneshärchen im Ohr, reizt den Hörnerv elektrisch und macht das Hören dadurch wieder möglich.
Hörbarrieren abbauen
Das österreichische Unternehmen MED-EL mit Sitz in Innsbruck hat sich auf die Entwicklung und Fertigung von Cochlea-Implantaten spezialisiert. Zum Produktportfolio gehören implantierbare und nicht implantierbare Hörsysteme. 2.500 Mitarbeiter zählt das Familienunternehmen. Zu den Kunden gehören neben Kliniken und Ärzten auch Audiologen, die die Patienten nach der Operation begleiten.
Dietmar Köll, verantwortlich für die Fertigung bei MED-EL, sagt: „Nicht sehen zu können, trennt von den Dingen – nicht hören zu können, trennt von den Menschen.“ Mit seinem Team arbeitet er daran, das zu ändern. „Mit unseren Produkten wollen wir Hörverlust als Barriere für Kommunikation und Lebensqualität überwinden und den Menschen wieder zu mehr Lebensfreude verhelfen. Das ist eine schöne Aufgabe.“
Jedes Ohr ist anders
Bei seinen Produkten setzt MED-EL auf eine breite Palette, denn: So individuell der Mensch, so individuell ist auch sein Ohr – beziehungsweise die Cochlea. Dietmar Köll erklärt: „Wir arbeiten sehr dynamisch und versuchen, die Rückmeldung der Kunden in unsere Produkte einfließen zu lassen. Darum bieten wir ein sehr breites Portfolio, das modular aufgebaut ist. Wir haben unterschiedliche Prozessoren und Implantate. Diese stellen wir nach den individuellen Bedürfnissen der Patienten zusammen. So finden wir für verschiedene Hörsituationen die optimale Lösung.“
Präzise Markierungen auf kleinstem Raum
Kleine Seriengrößen mit individuellen Beschriftungen sind in der Innsbrucker Fertigung daher Tagesgeschäft. Hier montiert MED-EL die Cochlea-Implantate und Audioprozessoren und versieht die kleinen Bauteile aus Metall und Kunststoff mit Markierungen. Zwei Trends beschäftigen die Tiroler Hörexperten aktuell besonders: Damit sie angenehmer zu tragen sind, werden die Bauteile immer kleiner, gleichzeitig steigen die Anforderungen an die Rückverfolgbarkeit und Dokumentation der Produkte und Fertigungsprozesse. Das Fertigungsteam muss also immer mehr Markierungen auf immer weniger Raum aufbringen. Zudem sollen sie gut lesbar und widerstandsfähig sein. Deshalb braucht es zuverlässige Fertigungstechnologien mit hohen Standards.
Kontrastreich und resistent
Bei MED-EL übernehmen drei TruMark Station 5000 von TRUMPF den Job. Ausgestattet mit Lasern der TruMark Serie 3000 markieren sie Bauteile aus Titan, Platin-Iridium und Kunststoff. Christoph Fankhauser ist stellvertretender Fertigungsleiter. Er erklärt: „Wir bringen hauptsächlich Seriennummern und sogenannte Unique-Device-Identification-Codes, kurz UDI, auf Metall- und Kunststoffteile auf. Diese maschinenlesbare, universelle Produktkennung ist für Medizinprodukte in Europa vorgeschrieben. Außerdem versehen wir die Teile mit Symbolen wie Pfeilen und Hinweisen, die den Anwendern die Handhabung erleichtern.“ Einheitliche Verläufe sind für MED-EL dabei das A und O, schließlich sind viele der Beschriftungen am Endprodukt sichtbar. Ein hoher Kontrast ist dafür ausschlaggebend, denn er gewährleistet eine gute Lesbarkeit. „Und natürlich müssen die Beschriftungen reproduzierbar sein. Sprich: Das Ergebnis muss immer dasselbe sein, selbst wenn es bei der Materialqualität mal mögliche Schwankungen gibt“, betont Fankhauser. „Eine hohe Leistungsstabilität ist die Voraussetzung dafür. Der TruMark Laser erfüllt diese Anforderungen auch auf kleinsten Bauteilen.“
Mit allen Sinnen
Von all diesen Bemühungen der Cochlea-Experten ahnt Paula nichts. Dass sie mit ihren Geschwistern lautstark und fröhlich durch die Wohnung tobt, gehört für sie ebenso zum Alltag wie der tägliche Kindergartenbesuch. Ihr Cochlea-Implantat hat das Leben für sie hörbar gemacht – und das genießt sie nun mit allen Sinnen.
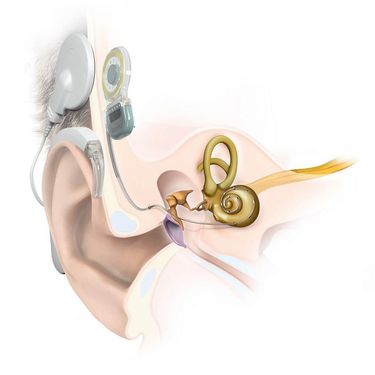
Eine Cochlea-Hörlösung besteht aus zwei Teilen: Einem Audioprozessor mit Mikrofon, der hinter dem Ohr getragen wird und Töne und Geräusche aufnimmt und dem eigentlichen Implantat, das unter der Haut sitzt. Vom Implantat führt ein Elektrodenträger ins Innenohr. Dieser lange, flexible Platindraht ist mit Elektroden bestückt und mit Silikon beschichtet. Empfängt der Audioprozessor Geräusche, gelangen sie als elektrische Signale zum Implantat. Dieses wandelt sie in elektrische Impulse um, die der Elektrodenträger in die Cochlea leitet und den Hörnerv stimuliert. Dieser gibt die Hörempfindungen an das Gehirn weiter, das sie als Töne und Geräusche interpretiert. Hochgradig Schwerhörige oder gehörlos geborene Menschen können damit hören lernen. Der künstliche Impuls, den das Implantat erzeugt, klingt anders als natürliche Geräusche. Wie eine neue Sprache, muss das Gehirn darum erst lernen, diese zu verstehen. Ein regelmäßiges Sprachtraining hilft dabei.
© MED-EL