TRUMPF TruPrint 1000 3D printer automatically changes substrate plates // Machine handles several print jobs overnight, on its own // Solution prevents bottlenecks when job orders spike
Formnext 2019: TRUMPF to present a solution for automated mass 3D printing
Ditzingen, 17. October 2019.– TRUMPF is set to present a new, patented solution that automatically changes substrate plates on the TruPrint 1000 3D printer. The high-tech company intends to unveil it at Frankfurt’s Formnext, the world's leading trade show for additive manufacturing. A function TRUMPF calls Multiplate prompts the system’s recoater to push the substrate plate into the overflow container at the end of the print run. The 3D printer then automatically goes to work on a new substrate plate. The system can immediately start the next print job without an operator having to open it and insert a new plate. This saves time, costs and resources. It also helps manufacturers avoid bottlenecks when job orders peak, because the machine can run overnight. This solution is particularly well-suited for industries where orders tend to fluctuate greatly. One example is the dental sector, where employees often have to restart 3D printers in the middle of the night to meet delivery obligations. Many smaller dental labs lack the capacity for this, and have no choice but to decline orders. The Multiplate function solves that problem, helping them to avoid bottlenecks and remain competitive. “With our solution, we are making a significant contribution to the industrialization of additive technologies in the dental industry,” says Florian Krist, product manager at TRUMPF Additive Manufacturing.
Goodbye handiwork, hello recoater
The construction cylinder, overflow container and recoater all have a part to play when the TruPrint 1000 automatically changes substrate plates. The cylinder and container sit below the process chamber. The machine prints the component on a substrate plate in the construction cylinder, while the overflow container collects excess powder. In a Multiplate setup, the recoater that distributes the powder in the build chamber during printing handles what is usually the machine operator’s task. It pushes the substrate plate on which the previous component was printed into the system’s overflow container. A spring support mechanism ensures that the overflow container lowers the substrate plate evenly. The next substrate plate is standing by in the TruPrint 1000's construction cylinder. After printing a component, the system lifts the new plate up into the process chamber. The TruPrint 1000 immediately starts the next printing job without an operator having to intervene.
A solution that saves time, resources and labor costs
Multiplate saves companies time and labor costs. Smaller companies can use it to run their systems at full capacity without additional personnel, so it takes the pressure off when job orders spike. This solution also conserves resources, as the machine operator does not have to replenish the shielding gas. With its machine base, the TruPrint 1000 is the world’s best-selling small-format 3D printer. And the Multilaser function, which uses two lasers simultaneously to print the component, makes it one of the fastest in its class. “We will be in an even better position to tap the market potential of the TruPrint 1000 with the Multiplate solution,” says Krist.
Digital photographs in print-ready resolution are available to illustrate this press release. They may only be used for editorial purposes. Use is free of charge when credit is given as “Photo: TRUMPF”. Graphic editing – except for dropping out the main motive – is prohibited. Additional photos can be accessed at the TRUMPF Media Pool.
Contato
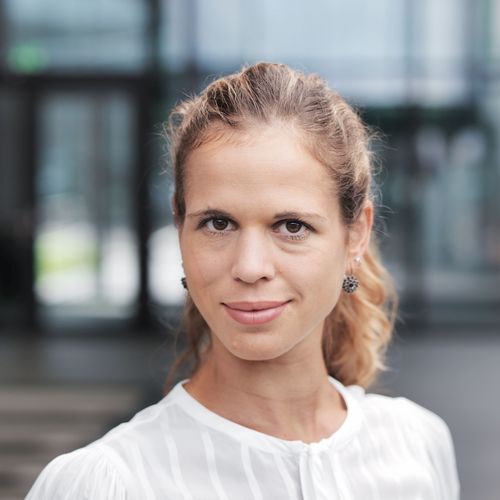