Der glänzende weiße Fußboden reflektiert das Licht der LED-Beleuchtung. Die CNC-Maschinen stehen in Reih‘ und Glied wie kleine Raumschiffe auf dem Weltraumflughafen bereit zum Abflug. In ihrem Inneren verwandeln sich Hartmetall-Rohlinge, sorgsam gekühlt durch permanent frisch aufbereitetes Kühlmittel, in schillernde Werkzeuge. Sie verlassen den Bauraum erst dann, wenn die Maschine den letzten Mikrometer Material exakt nach Plan abgetragen hat.
Was bei Horn die Produktionshalle verlässt, muss die Ansprüche Schweizer Uhrenhersteller, der Medizintechnik oder der Luft- und Raumfahrtindustrie erfüllen. Das 1969 von Paul Horn gegründete Unternehmen hat sich weltweit einen Namen für Präzisionswerkzeuge für anspruchsvolle Zerspanung gemacht. Anders ausgedrückt: Nur wenige Unternehmen verstehen es so gut, Material bis aufs letzte µ genau abzutragen, wie Horn.
Lehrgeld zahlen
Umso verwunderlicher scheint es, in diesem Unternehmen eine Maschine vorzufinden, deren Stärke genau das Gegenteil ist. Denn im ersten Stock im Tübinger Werk 2 perfektioniert Horn seine Kompetenzen in der Additiven Fertigung mit einem 3D-Drucker von TRUMPF. In der TruPrint 3000 von TRUMPF transformieren zwei 500 Watt Laser rund um die Uhr die Ideen der Entwickler und Konstrukteure aus feinstem Metallpulver in die Realität.
„Nur wer Neues wagt, kann dazulernen“, sagte der kürzlich verstorbene Geschäftsführer von Horn, Lothar Horn 2019 in einem Interview. Matthias Luik, seit 2010 Leiter Forschung und Entwicklung des Unternehmens nimmt den Ball auf: „Wer die Technologieführerschaft in einem Bereich für sich proklamiert, der darf sich vor neuen Technologien nicht verschließen.“ Und so war es für die Experten für Präzisionswerkzeuge selbstverständlich, 2018 einen eigenen Bereich für Additive Manufacturing (AM) in der Tübinger Zentrale zu schaffen, um die Grenzen und Möglichkeiten des 3D-Drucks auszuloten. „Das Know-how für Werkstoffe und Materialien hatten wir bereits im Haus, auch das verwendete Pulver können wir selbst analysieren“, erklärt Matthias Luik. „Für alles andere haben wir auch Lehrgeld bezahlen dürfen.“ Aus seinem Mund klingt selbst das noch euphorisch – „aus Fehlern lernen“ ist bei Horn Teil der Unternehmenskultur.
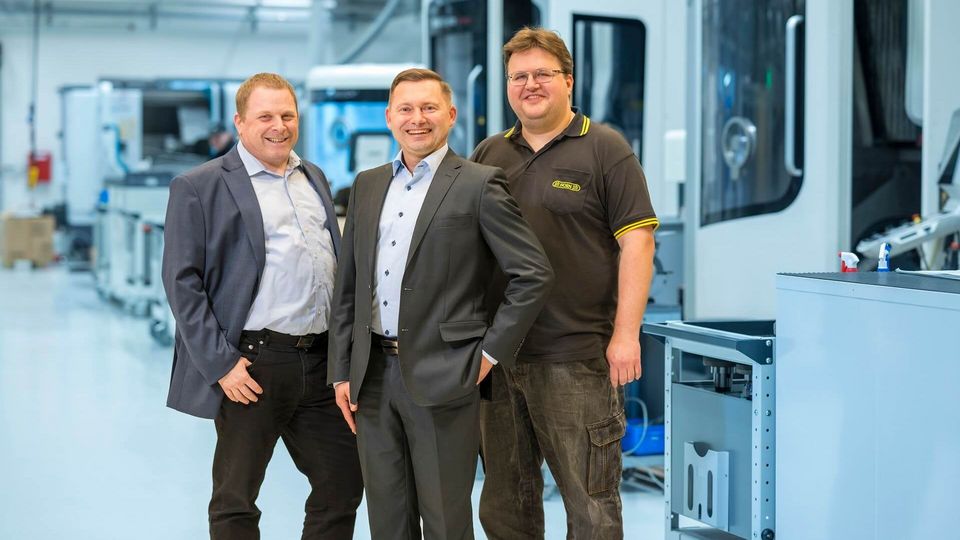
Matthias Luik (links), Leiter Forschung und Entwicklung bei Horn, mit dem AM-Team: Dr. Konrad Bartkowiak (Mitte), Leiter des Bereichs Additive Fertigung und Michael Schäfer (rechts), Konstrukteur für Additive Fertigung und hauptverantwortlicher Bediener der neuen TRUMPF Anlage bei Horn.
Nicht zufriedenstellend
Schon nach drei Jahren intensiver Tests und der akribischen Auseinandersetzung mit Pulvern, Prozessparametern, Druckprozessen und Prototypenfertigung kam die initial gekaufte Maschine von einem anderen Hersteller mit den Ansprüchen des AM-Teams nicht mehr mit. Eine Neue musste her. Ein strukturierter, halbjähriger Benchmarktest inklusive Langzeittest, Bewertung von Servicequalität und Kommunikation brachte Horn schließlich zu TRUMPF. „Das Ding läuft einfach“, kommentiert Dr. Konrad Bartkowiak, Leiter des Bereichs Additive Fertigung bei Horn und lobt die Robustheit und konsistente Qualität der Anlage. Die geringen Ausfallzeiten und die Prozessstabilität der TruPrint 3000 scheinen zudem positiven Einfluss auf die Work-Live-Balance des AM-Teams haben: „Seit wir mit der TruPrint 3000 arbeiten, gehe ich viel entspannter ins Wochenende“, ergänzt Michael Schäfer – er ist Konstrukteur für Additive Fertigung bei Horn und hauptverantwortlicher Bediener der neuen TRUMPF Anlage. In der Vergangenheit musste er bei Fehlermeldungen oder abgebrochenen Baujobs Sonderschichten einlegen, um die Maschine wieder in Gang zu setzen.
Schnell produktiv sein
Seit Mai 2022 steht das „Baby“ von Bartkowiak und Schäfer in der Produktion, seit September arbeitet das Team produktiv mit der Anlage. In den ersten sieben Monaten haben sie mehr als 20 interne und externe Projekte umgesetzt: Auftragsarbeiten für Kunden, Prototypen für den Werkzeugkatalog und Bauteile für die Produktionsanlagen, um das Maximum aus den eigenen Maschinen herauszuholen. So zum Beispiel eine Kühlmitteldüse für eine Maschine, auf der die Mitarbeiter Werkstücke innenrundschleifen. Die dutzenden, innenliegenden Kanäle der Kühlmitteldüse ermöglichen eine präzise und punktgenaue Kühlung von Schleifstift und Werkstück. Das Resultat: Der Schleifstift hält länger und die Qualität des bearbeiteten Werkstücks ist höher. „Mit konventionellen Fertigungsmethoden wäre das Bauteil aufgrund der sehr feinen, innenliegenden Strukturen nicht realisierbar gewesen“, erklärt Matthias Luik.
Grenzen ausloten
Perspektivisch will Horn die Auslastung der Maschine weiter steigern. Ein Prototyp eines bislang konventionell gefertigten Drehwerkzeugs befindet sich derzeit in der Testphase und könnte schon bald den Sprung in den Produktkatalog von Horn schaffen. Einer Serienproduktion steht dann nichts mehr im Wege. „Auf der Serienproduktion liegt derzeit aber nicht der Fokus unserer AM-Abteilung“, sagt Entwicklungschef Luik. „In erster Linie geht es uns darum, mit der Anlage von TRUMPF die Grenzen des technologischen Fortschritts auszuloten, den uns die Additive Fertigung bietet. Das ist das, was Horn am Ende einen Marktvorteil und unseren Kunden bessere Werkzeuge für ihr Business bringt. Im Bereich der Prototypenentwicklung, der Gewichtsreduktion und der Kühlung sehen wir aktuell die größten Vorteile des 3D-Drucks für uns“. Perspektivisch will das Unternehmen auch in die hybride Fertigung von Werkzeugen einsteigen. Angedacht sind konventionell gefertigte Werkzeugrohlinge, auf die der Werkzeugkopf mit innenliegenden Kühlkanälen additiv gedruckt wird. Dieser kann dann im Nachgang mit Wendeschneidplatten aus unterschiedlichen Schneidstoffen bestückt werden. Darüber hinaus bietet Horn für seine Kunden auch die Herstellung 3D-gedruckter Bauteile mit der gesamten Prozesskette an – inklusive kompletter Nachbearbeitung.
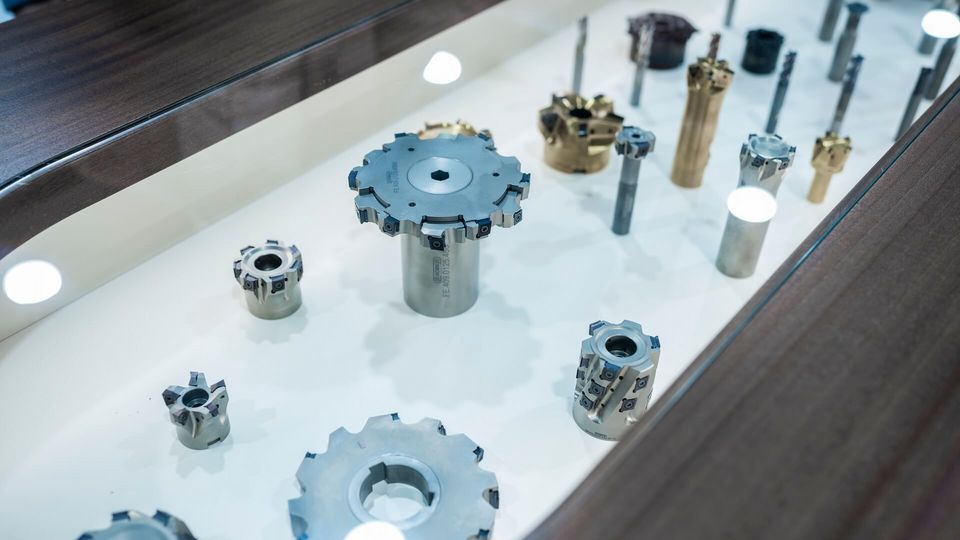
Das erste additiv gefertigte Drehwerkzeug könnte schon bald das Sortiment der mehr als 25.000 Standardwerkzeuge von Horn erweitern.
In die Zukunft investieren
Dass die Additive Fertigung gekommen ist, um zu bleiben, steht bei Horn außerfrage. Den eigenen AM-Nachwuchs zieht sich das Unternehmen bereits mit ersten Azubi-Projekten auf der TRUMPF Anlage heran. Und auch für den Fall, dass das AM-Geschäft plötzlich explodiert, hat das Unternehmen bereits vorgesorgt: In Werk 2 hat Horn in unmittelbarer Nachbarschaft zur TruPrint 3000 noch reichlich Platz für weitere Additive Fertigungssysteme freigehalten.