TRUMPF's intelligent monitoring solutions enable you to easily monitor, analyze and calibrate the LMF process in TruPrint machines. You can then produce even more efficiently and achieve higher component quality. The professional monitoring process makes it possible to display and analyze sensor-based data. The offer comprises solutions for monitoring the process, condition, and performance. Monitoring results can be seen directly on the TruPrint machine's HMI or evaluated offline via the Monitoring Analyzer. TruTops Monitor provides not only transparency but also the option for remote access via PC or tablet. Furthermore, an OPC UA interface provides full flexibility to connect to your own software solution. With the additionally available calibration functions, you can check the process-relevant parameters for optimal production conditions before the start of the build job.
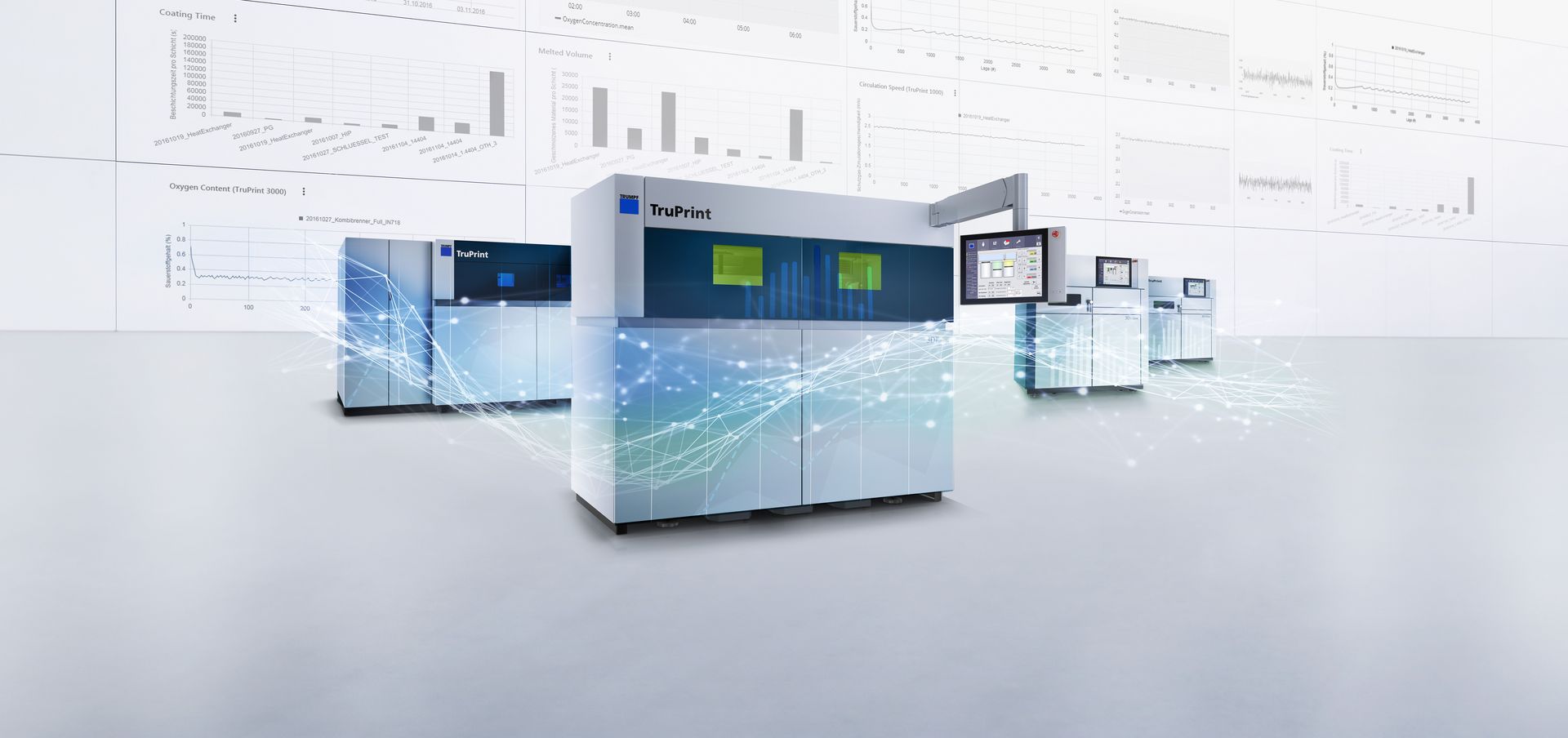
TruPrint monitoring
Clever digitization by TRUMPF for your additive manufacturing systems
As a result of the monitoring solutions, you can keep an overview of key production data and system states across all your machinery.
With early error detection and notification, you can react in time.
Due to improved transparency, you can optimize your processes in the long term.
Take advantage of comprehensive information for verifying the quality of your components.
Display and analyze only the key figures that are relevant for your build job.
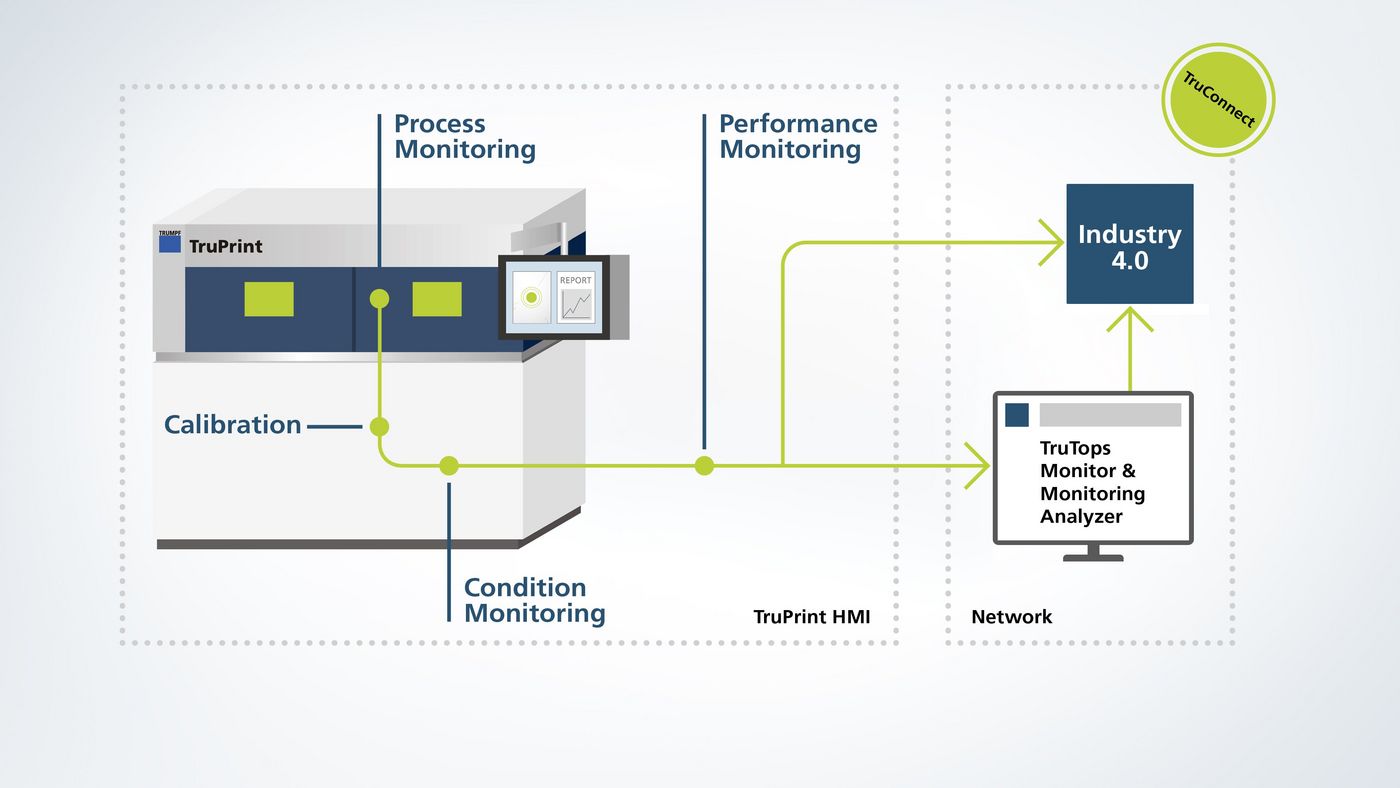
Process Monitoring for monitoring component quality
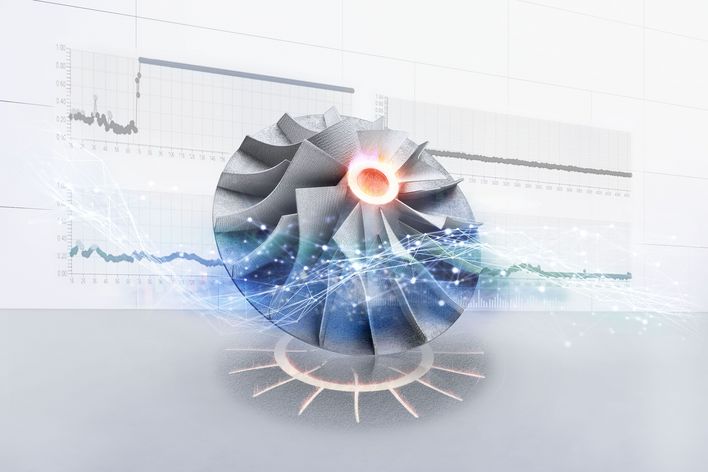
Process monitoring focuses on the LMF process. The powder bed is monitored during the laser exposure process. Two products are available for this purpose: Powder Bed Monitoring enables you to monitor the powder bed, and Melt Pool Monitoring enables you to monitor the weld pool of your TruPrint machine. As a result, you maintain full control over the quality of your components – layer-by-layer. Your production system is also made more efficient as errors are identified quickly.
Layer-by-layer monitoring to verify component quality
View of the weld pool in the TruPrint 2000
How does Powder Bed Monitoring work?
A central component of process monitoring is the Powder Bed Monitoring function. The integrated camera in the TruPrint machine allows you to automatically monitor the powder bed and images are automatically processed. With this, you have an overview of the component state at all times and can analyze the quality parameters layer-by-layer. The TruPrint machines are equipped with a high-resolution camera system, so you have a precise view of each powder layer. Automatic evaluations are possible in conjunction with the image processing function, whereby the integrated dark field illumination additionally supports the image analysis. As the user, you determine the limit values at which notifications or error messages should appear. As the quality parameters are assigned per layer, locating malfunctions is fast and accurate. This means that you can intervene in the current build job at an early stage. In addition to the powder coating, the Powder Bed Monitoring function also records the state of the layer and identifies protruding parts in the powder bed. The process is ideal for evaluating the condition of the components during the LMF process and for identifying potential developments at an early stage. The automatic corrective recoating option ensures component quality in the event of coating errors. A detected lack of powder is automatically corrected by a new powder coating. After the LMF process, a comprehensive analysis of the individual layers can also be performed via the image selection and be compared with CAD data.
Melt Pool Monitoring – monitoring the weld pool
For a better overview of the LMF process in the TruPrint machine and the ability to optimally evaluate the component quality you can take advantage of the Melt Pool Monitoring product for the TruPrint 2000 and the TruPrint 5000, along with the Powder Bed Monitoring function. With Melt Pool Monitoring, the weld pool of the laser metal fusion process is monitored using sensors. Take advantage of a detailed quality check and documentation, layer-by-layer. This enables you to detect any process deviations early on, including during series production, and, if necessary, see critical areas of the component. These key figures can then be automatically compared with a reference build job to monitor the stability of the process. Furthermore, when using several lasers, you can also easily monitor all of weld pools in parallel. The data can be evaluated on a desktop computer or offline with the Monitoring Analyzer.
Note: This product range and this information may deviate depending on the country. Changes in technology, equipment, price and available accessories are reserved. Please get in touch with your local contact person to find out whether the product is available in your country.
Always have an overview of the TruPrint machine state with Condition Monitoring
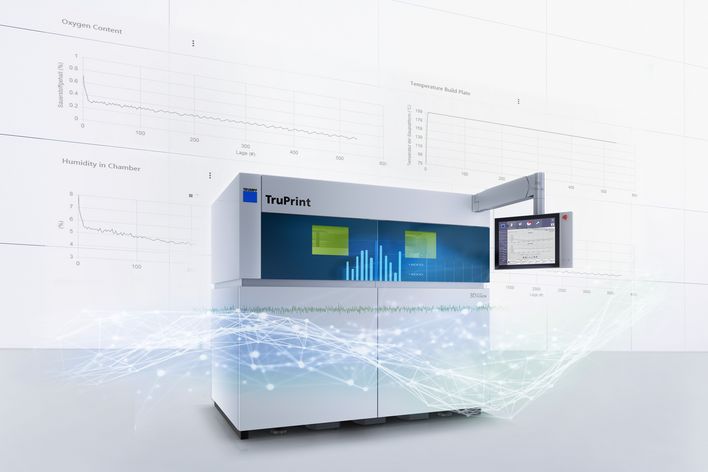
In addition to the machine's status data, condition monitoring also records data from the process environment. This allows you to monitor the machine condition at any time and analyze many parameters. Data on the current status of your TruPrint machine is collected via a large number of sensors. This data is documented and can be used for quality control. You can view the data directly at any time via the HMI. In this way, you can identify faults at an early stage so that you can intervene in the LMF process or cancel it in an emergency. Customize your data view and get a clear overview of all the information relevant to you.
A range of different indicators which influence the machine state can be monitored by Condition Monitoring from TRUMPF:
- Build chamber state such as humidity, substrate plate temperature, shielding gas speed, etc.
- Ambient conditions such as oxygen level or temperature
- Cooling water temperature
- Filter data
- Machine axes
Note: This product range and this information may deviate depending on the country. Changes in technology, equipment, price and available accessories are reserved. Please get in touch with your local contact person to find out whether the product is available in your country.
Performance monitoring for complete transparency regarding machine productivity
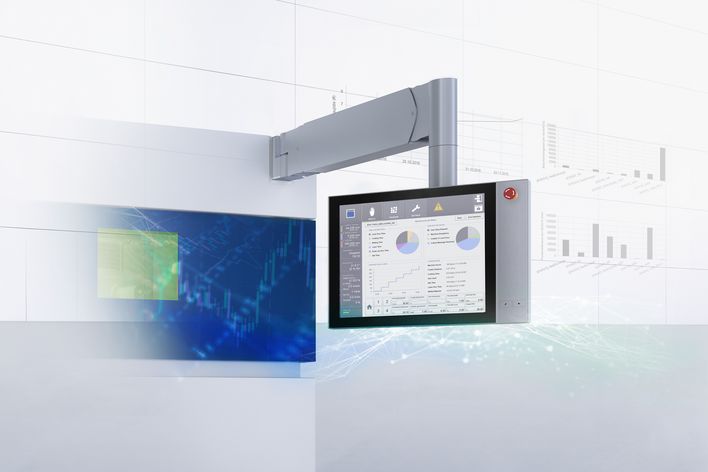
Machine productivity is essential for successful industrial manufacturing. Therefore, performance monitoring from TRUMPF provides all the key productivity figures for comprehensive evaluation of the machine's performance. You can check and analyze the status of all consumption easily and at any time on the TruPrint HMI. After the build job is complete, a comprehensive report is created via Performance Monitoring. This report contains all the important facts about the assignment as well as findings from the other monitoring observations. You can easily configure and design this report according to your needs. In order to display machine consumption or key productivity figures such as shift times, fusion rate and running times as clearly as possible, all performance parameters are prepared graphically for you. You also benefit from target/actual comparisons based on the process and condition monitoring data. This enables you to carry out a comprehensive analysis of the build job. By collecting all productivity and utilization factors, performance monitoring contributes to more economical production overall.
Note: This product range and this information may deviate depending on the country. Changes in technology, equipment, price and available accessories are reserved. Please get in touch with your local contact person to find out whether the product is available in your country.
Connectivity – monitoring on the machine and in the network
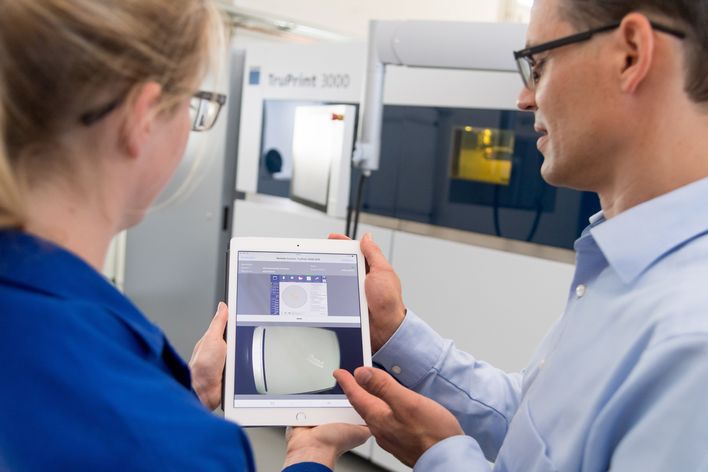
TruTops Monitor
With TruTops Monitor, you are also provided with complete transparency externally across your machinery, along with the option of remote access. Observe, analyze, and control your TruPrint machinery comfortably from your desktop. The analysis of the machine data and utilization of the entire machinery will enhance your industrial additive manufacturing. Error notifications via email give you the option of modifying your processes as quickly as possible.
Monitoring interfaces
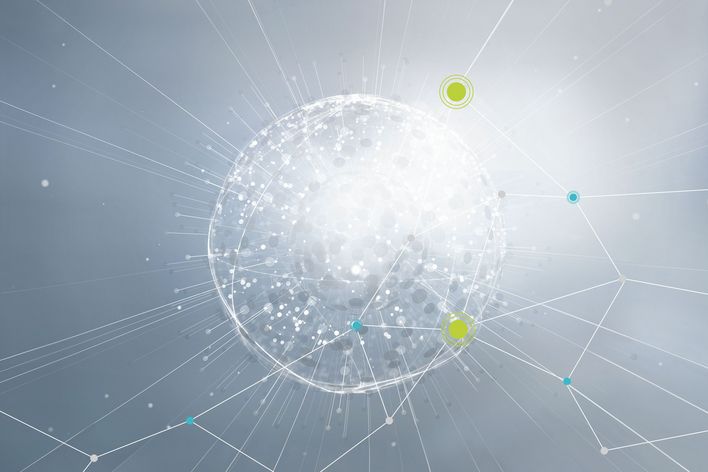
OPC UA interface – for connecting to your own network solutions
With the OPC UA monitoring interface, you have the option to link the TruPrint performance monitoring data with your individual software in a flexible manner. The performance monitoring data is transferred live, by means of a standardized interface.
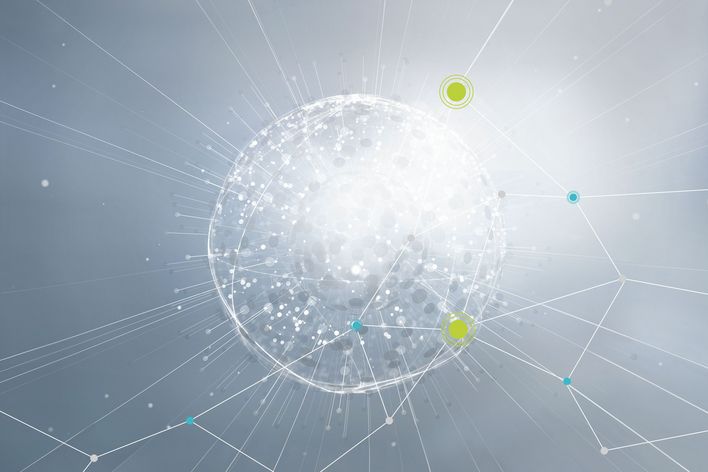
Monitoring file interface
The monitoring file interface enables automatic export of monitoring data to the user's file system. The monitoring data is provided for the Monitoring Analyzer. The data can be analyzed and archived by the user with their own software.
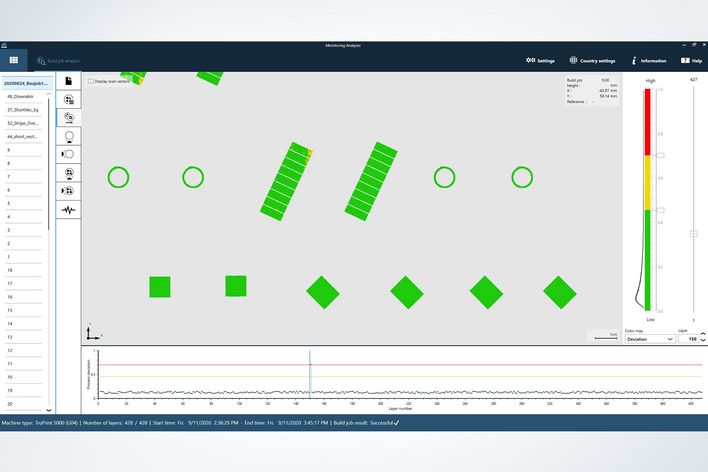
Monitoring Analyzer
The Monitoring Analyzer is a Windows desktop application which can be used to view the data of the monitoring file interface. Each user has their own floating license. This means that monitoring data, whether current or archived, can be easily analyzed and viewed on a PC desktop and at a workstation away from the machine.
Note: This product range and information may vary depending on the country. Subject to changes to technology, equipment, price, and range of accessories. Please get in touch with your local contact person to find out whether the product is available in your country.
Calibration
Verifying machine performance
Optimise component quality like never before: the Automatic Multilaser Alignment provides fully automated online monitoring and correction of beam source positioning relative to each other - to 27.5 µm accuracy. A high-resolution camera system and darkfield lighting make it possible to record, analyze and correct images while the build job is in progress. Quality indicators for each measurement sequence enable faults to be quickly localized. Measurement readings are documented in condition monitoring.
Our laser power calibration measures and, where necessary, recalibrates the laser power between two build jobs - independently of annual maintenance by the customer. All lasers are checked on machines with the fullfield multilaser option. At the same time, measurement readings are documented to comply with the requirement to provide verification. Laser power measurement is based on DIN 35224 and ISO 52941.
This option is used to measure focus positions between two build jobs. The laser protective screen is checked for possible impurities (thermal shift). Measurement readings are documented to comply with the requirement to provide verification.
Scan field calibration enables you to measure and, where necessary, to recalibrate the scan field between two build jobs. Measurement readings are also documented to comply with the requirement to provide verification.