Order preparation processes are integrated in Oseon. Interfaces enable communication with adjacent sections , e.g., programming. You can use the production planning tool to simplify production planning. It provides reliable information on delivery dates, taking into account workstation capacities and the current status of production. Paperless and networked with all production employees.
Oseon Workflow
Oseon Go digitalizes all core processes in your production.
Oseon Grow is an extension of Go in the areas of storage, logistics, and interfaces.
You achieve a complete network with Oseon Flow.
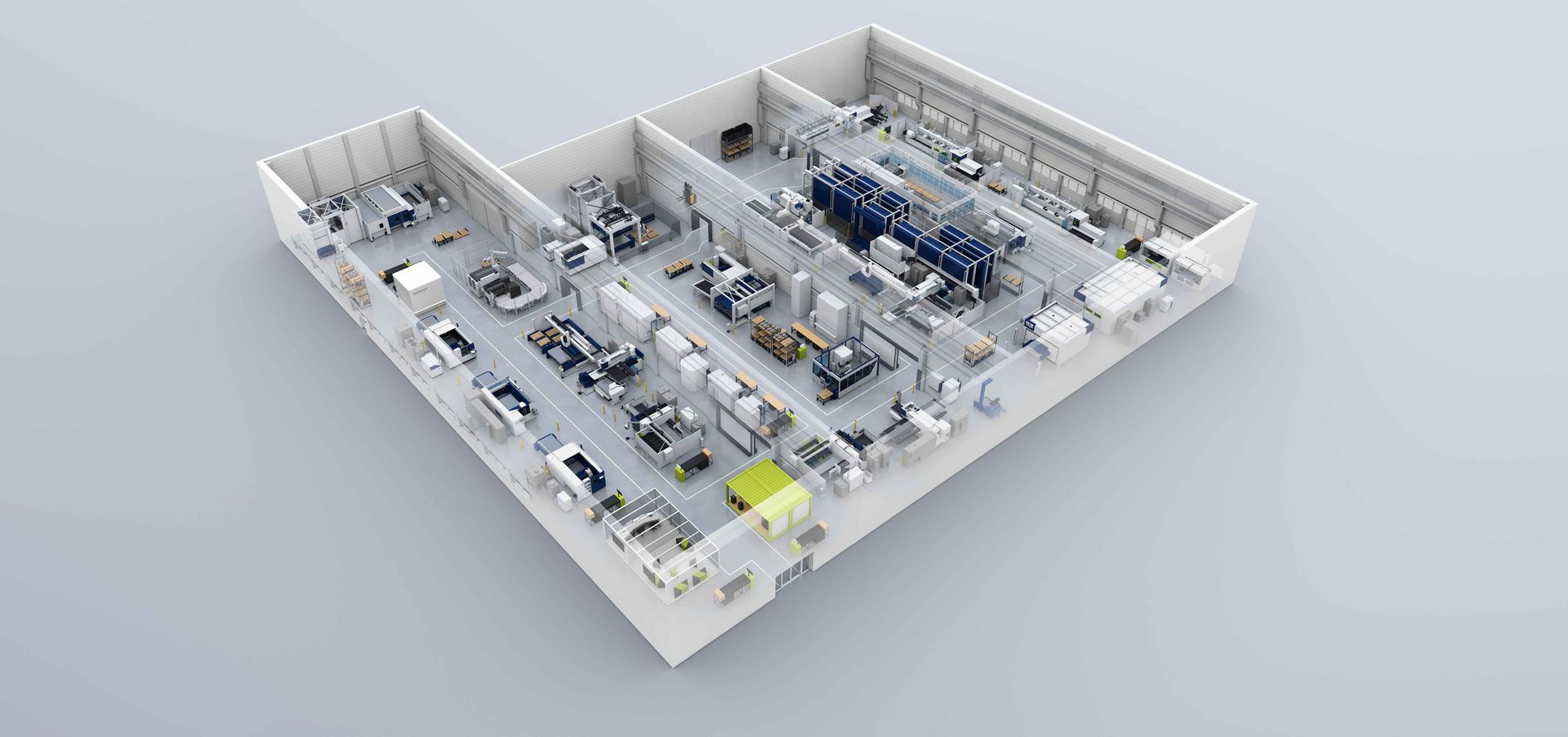
1. Order preparation
In work preparation, production orders are created quickly and easily or imported via an interface and scheduled for production.
Find out more2. Cutting parts
The web-based app on the tablet provides targeted support to production employees. It displays information relevant to the order and step-by-step instructions.
Find out more3. Sorting
Graphical support on the web-based app simplifies part separation, both directly on the machine and at a separate workstation.
Find out more4. Factory flow
Automatic transport planning and ordering keeps your materials constantly flowing. You can check stock, know exactly where orders are and find out where they are required next .
Find out more5. Bending
With the app, employees at bending machines receive all key information about production orders and bending programs. Reduced to the essentials and directly at the workstation.
Find out more6. Welding
Oseon also integrates non-networked production systems into the production flow. To do so, the app sends all relevant to the machine operator's tablet.
Find out more7. Threaded bolt welding
With the web-based app, manual workstations are fully integrated. Step-by-step instructions ensure a high level of process reliability, even for inexperienced employees.
Find out more8. Assembly
With Oseon ,assembly employees have mobile access to work instructions and drawings. This increases efficiency and process reliability.
Find out more9. Analytics
Oseon Analytics gives you a complete overview of your entire production line at all times with instant malfunction notifications. Comprehensive dashboards ensure a high level of transparency.
Find out moreOrder preparation
Cutting parts
With Oseon, production employees on the shop floor (e.g., operators of 2D laser cutting and punching machines) always have all the important information about their own production on hand. For a transparent overview and better process reliability, all feedback on the order is provided digitally. As a result, paper consumption is reduced to a minimum.
Sorting
The app uses colored markers to show shop floor workers exactly which parts belong to a production order, assembly or customer order. For even more efficiency, the parts are booked on pallets or containers in the same work step and transport orders are created for the next workstation. This is a major simplification that increases transparency and process reliability.
Factory flow
Manual and automatic transport vehicles are taken into account depending on availability. Logistics employees are informed about transport orders via the web app and are supported in their operations digitally. The seamless interaction increases the efficiency in material flow. Oseon also supports the stock management of manual, automatic or large storage systems - depending on the customer's needs.
Bending
Oseon provides bending programs suitable for the loaded production orders on the tablet or machine monitor. The availability of the parts to be bent is also displayed with the corresponding priorities . To increase flexibility, the management of bending pools and the assignment of a bending machine are also supported. Processes can be easily booked via the app, bringing transparency to the shop floor.
Welding
The web-based app shows employees all the information relevant to the work order at the respective workstation. Loaded production orders and priorities, drawings, necessary materials - including storage locations and work and safety instructions - are clearly provided. Work progress can be conveniently recorded in the app.
Threaded bolt welding
Oseon integrates manual workstations holistically into networked production. Drawings and bills of materials can be viewed and material postings and reject messages can be booked digitally, directly at the workstation. Production progress is reported to the system via the app and transport orders are registered for subsequent processes through automatic booking at docking stations.
Assembly
Oseon digitally integrates assembly stations into production. Operator's manuals and 3D drawings ensure clear work instructions. The availability of parts from upstream operations that are necessary for the production order are displayed via web app. This eliminates uncertainties. The system is digitally notified when the order is complete by the click of a button.
Analytics
Evaluation options and status messages on machines and workstations enable a consistent and transparent view of your production. Use this information together with your employees for active shop floor management. Together you will achieve shorter production and delivery times and a faster response to customer requests.