
Additive Fertigungssysteme
The right solution for every metal AM application
Von der Prototypenfertigung bis hin zur industriellen Serienproduktion. Als Pionier in den additiven Technologien und Laserspezialist seit 1979 bieten wir für jede metallische Applikationsanforderung die passende Technologie: Laser Metal Fusion (pulverbettbasiertes Laserschmelzen) bzw. (Laser) Powder Bed Fusion (PBF / LPBF) oder Laser Metal Deposition (generatives Laserauftragschweißen). Profitieren Sie bei TRUMPF von reproduktiven, hochqualitativen Ergebnissen sowie industriellen Lösungen mit intelligentem Monitoring und smarten Services weltweit.
Finden Sie jetzt Ihre additive Fertigungslösung für die Zahntechnik!
Welche TruPrint Maschine am besten zu Ihrer Anwendung in der Zahntechnik passt, erfahren Sie mit Hilfe des TruPrint Produktfinders!
Powder Bed Fusion
Laser Metal Deposition
Kontakt
Services
Downloads
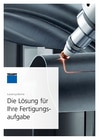
Broschüre Lasersysteme
pdf -
4 MB
Flyer Additive Fertigungssysteme für Metallpulver im Überblick
pdf -
7 MB
Flyer Beratung für die additive Fertigung
pdf -
647 KB
Seminar - Bauteilgestaltung für AM
pdf -
571 KB