From small batch to 24/7 production: TruDisk always offers the best value for your money. The TruDisk S Series supports up to four machines or process cells – guaranteeing maximum utilization of the systems in continuous operation. In addition, the TruDisk P Series provides the optimum solution for supplying an individual machine with standard utilization. Select the right laser for your production requirements.
High-performance solid-state laser
The TruDisk is a high-power solid-state laser for the welding, cutting, and surface processing of metals. It impresses above all in situations which require the combination of high power and maximum beam quality. The new generation of TruDisk lasers provides you with great advantages, above all due to its much more compact footprint and increased robustness. It also has intelligent inner parts. The data quality of the sensor systems which monitor all the important parameters in the laser has been improved significantly so that the new TruDisk lasers are perfectly prepared for future Industry 4.0 services such as condition monitoring. The TruDisk operates economically in all laser states due to increased efficiency, a new pulse function with increased energy efficiency, and intelligent energy management.
Stable processes through integrated, active laser power control ensure reproducible results.
As a laser medium, the disk in the TruDisk ensures brilliant beam quality up to 2 mm·mrad.
The patented resonator design means that your TruDisk can also process highly reflective materials.
Multiple energy-saving modes and the power factor correction reduce the power requirement.
With BrightLine Weld you can achieve high-quality welding seams with minimal spatter formation.
Choose between an integrated heat exchanger (standard) and compressor cooler (optional).
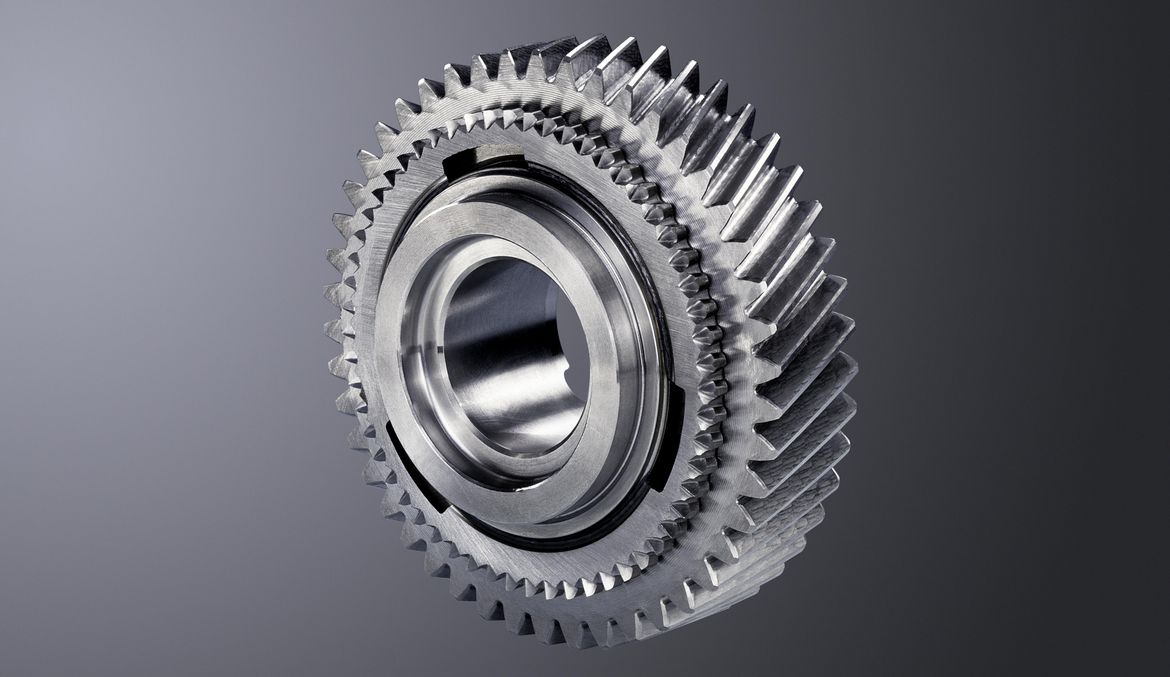
Deep welding
The TruDisk high-power laser is well-suited for numerous applications in the automotive industry, for example in the power train – here a control gear. The requirements regarding accuracy and reproducibility are particularly high here. This is easy for the disk laser, which has a laser power that can be precisely adjusted and is monitored.
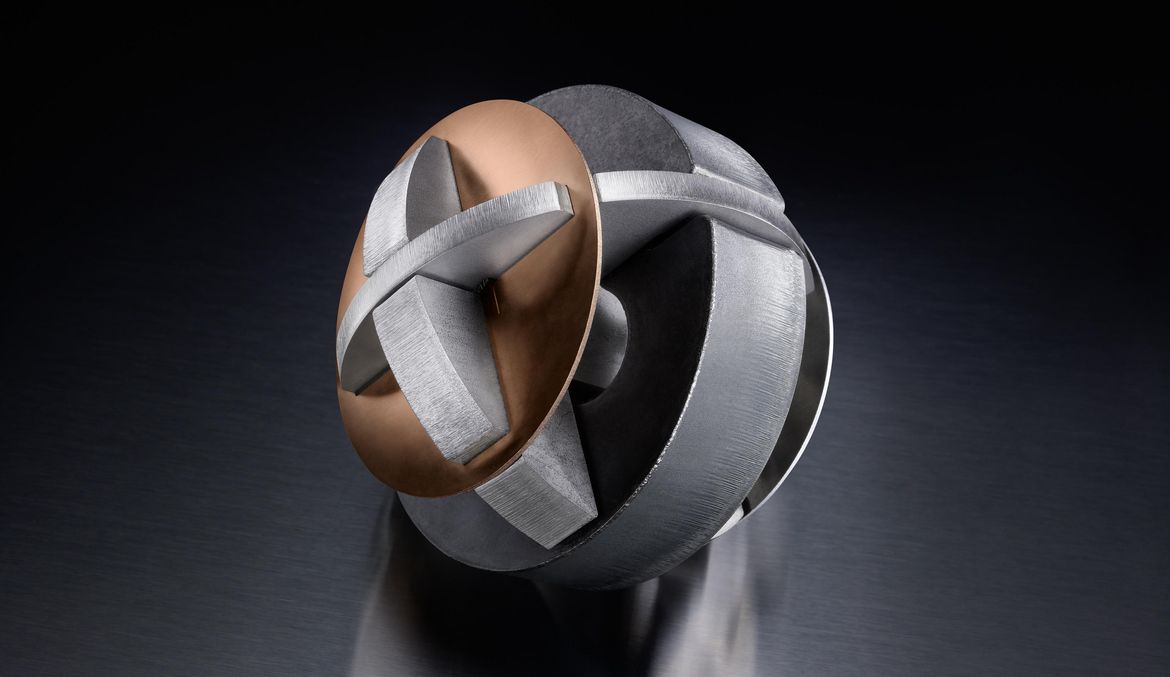
Cutting of an array of materials and sheet thicknesses
Laser cutting makes almost any contour shape possible – even intricate and complex ones – without the need for tool changes. The edges are smooth and burr-free, so there is no need for post-processing. Due to the small size of the heat-affected zone, there is virtually no distortion. The TruDisk cuts an array of sheet thicknesses and material types – even highly reflective non-ferrous metals.
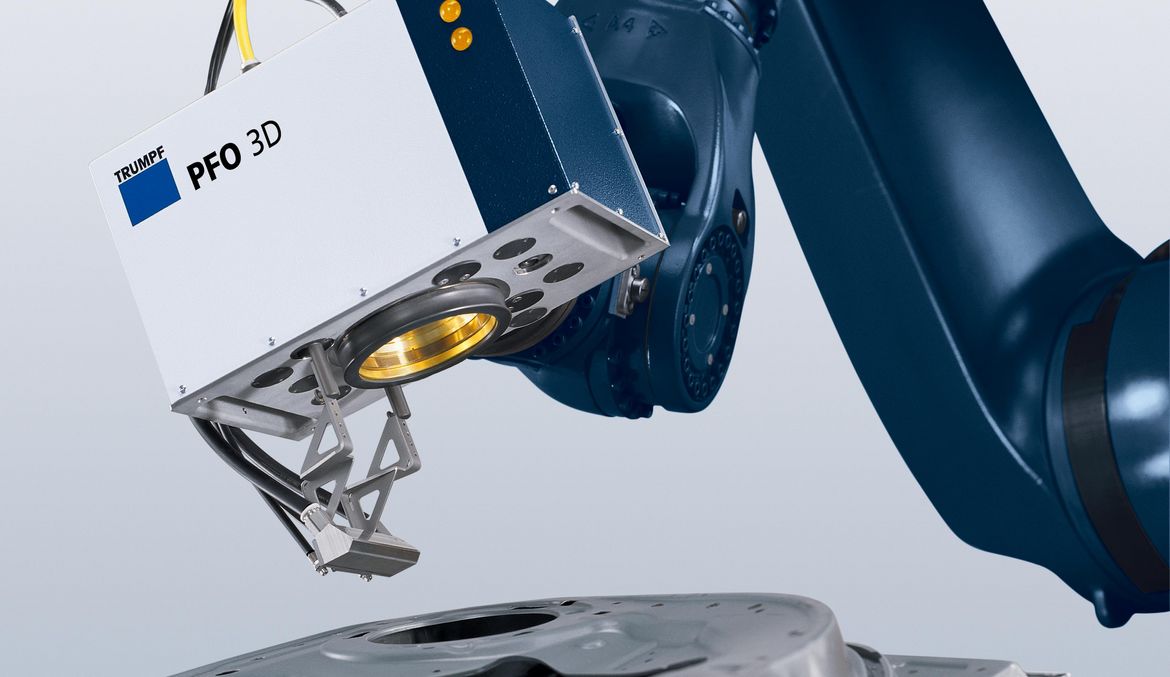
Scanner welding of a car door
In combination with focusing optics, for example the programmable focusing optics PFO 3D, the TruDisk lasers serve as a beam source for scanner welding. In this process, the laser beam is directed by moving mirrors. Angle changes guide the beam over the workpiece. A processing field emerges, which enables highly dynamic and precise welding. Due to the very fast translation movements of the mirrors, non-productive times are reduced virtually to zero and the laser device is able to produce in almost 100% of the available production time.
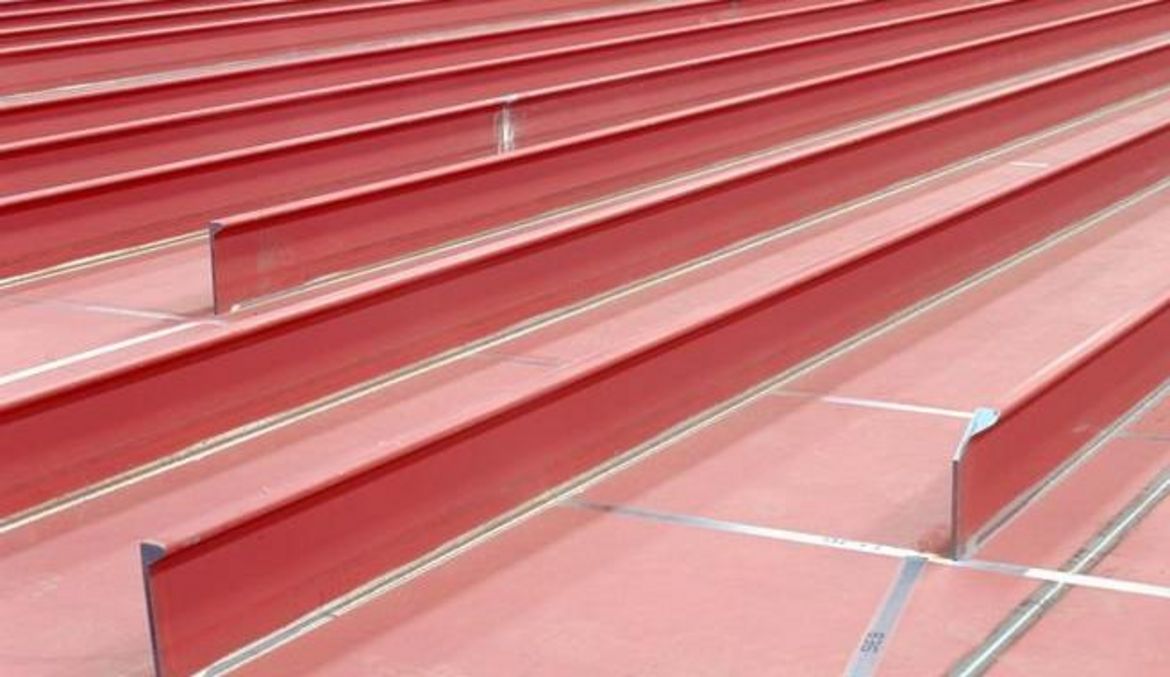
Hybrid welding of enormous ship decks
Hybrid laser welding combines thick sheets of up to 0.8 in. with large joint gaps. The TruDisk is insensitive to reflections that would cause problems for other lasers, and is therefore exceptionally well-suited for this application. Typical hybrid welding applications are in automotive manufacturing, ship building, crane construction, heavy engineering, construction equipment, and many other areas.
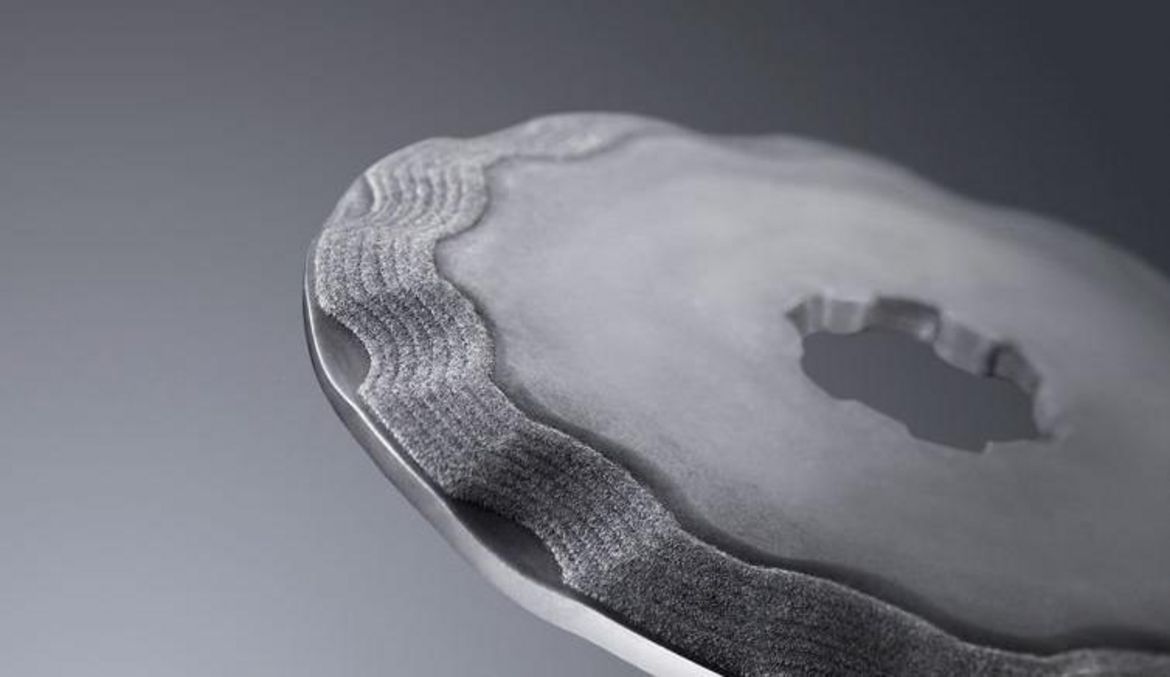
Chopper with LMD contour
If a component is subject to high temperatures, pressure, abrasion, or moisture, special materials must be used. However, this does not mean that the entire component needs to consist of the corresponding material. A protection layer applied to the edge of the load zone by means of laser metal deposition is sufficient. As can be seen here in a chopper. In laser metal deposition, the laser generates a weld pool on the surface of the component. Metal powder is introduced little by little through a nozzle, until the desired layer thickness is achieved.
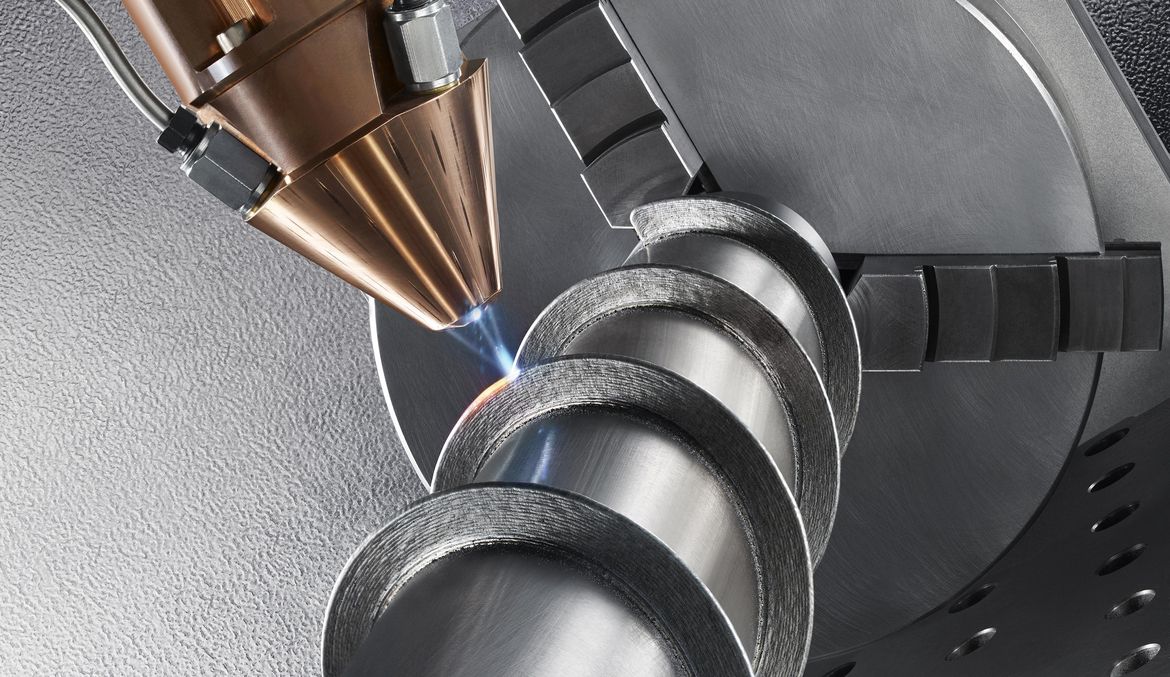
Laser metal deposition as an additive manufacturing method
In laser metal deposition (LMD), the laser generates a weld pool on the component surface. Metal powder is automatically introduced through a nozzle. Beads form that are welded to one another, which then form structures on existing base bodies or entire components. Here, a screw conveyor is applied layer by layer to a tube using LMD. In comparison to other generative processes, LMD has high build-up rates and therefore, a high process speed.
TruDisk 1000
Compare product
|
TruDisk 2000
Compare product
|
TruDisk 3000
Compare product
|
TruDisk 3001
Compare product
|
TruDisk 3001 P
Compare product
|
TruDisk 3002
Compare product
|
TruDisk 3006
Compare product
|
TruDisk 4000
Compare product
|
TruDisk 4001
Compare product
|
TruDisk 4001 P
Compare product
|
TruDisk 4002
Compare product
|
TruDisk 4006
Compare product
|
TruDisk 5000
Compare product
|
TruDisk 5001
Compare product
|
TruDisk 5002
Compare product
|
TruDisk 5006
Compare product
|
TruDisk 6000
Compare product
|
TruDisk 6001
Compare product
|
TruDisk 6001 P
Compare product
|
TruDisk 6002
Compare product
|
TruDisk 6006
Compare product
|
TruDisk 8000
Compare product
|
TruDisk 8001
Compare product
|
TruDisk 8002
Compare product
|
TruDisk 10001
Compare product
|
TruDisk 12001
Compare product
|
TruDisk 16001
Compare product
|
TruDisk 20001
Compare product
|
TruDisk 24001
Compare product
|
|
---|---|---|---|---|---|---|---|---|---|---|---|---|---|---|---|---|---|---|---|---|---|---|---|---|---|---|---|---|---|
Laser parameters | |||||||||||||||||||||||||||||
Laser Power | 1000 W 1 | 2000 W 1 | 3000 W 1 | 3000 W 1 | 3000 W 1 | 3000 W 1 | 3000 W 1 | 4000 W 1 | 4000 W 1 | 4000 W 1 | 4000 W 1 | 4000 W 1 | 5000 W 1 | 5000 W 1 | 5000 W 1 | 5000 W 1 | 6000 W 1 | 6000 W 1 | 6000 W 1 | 6000 W 1 | 6000 W 1 | 8000 W 1 | 8000 W 1 | 8000 W 1 | 10000 W 1 | 12000 W 1 | 16000 W 1 | 20000 W 1 | 24000 W 1 |
Typical power constancy at rated power over 8 hours at constant ambient temperature | ± 0.5 % | ± 0.5 % | ± 0.5 % | ± 0.5 % | ± 1 % | ± 0.5 % | ± 0.5 % | ± 0.5 % | ± 0.5 % | ± 1 % | ± 0.5 % | ± 0.5 % | ± 0.5 % | ± 0.5 % | ± 0.5 % | ± 0.5 % | ± 0.5 % | ± 0.5 % | ± 1 % | ± 0.5 % | ± 0.5 % | ± 0.5 % | ± 0.5 % | ± 0.5 % | ± 0.5 % | ± 0.5 % | ± 0.5 % | ± 0.5 % | ± 0.5 % |
Maximum power constancy at rated power over 8 hours at constant ambient temperature | ± 1 % | ± 1 % | ± 1 % | ± 1 % | ± 2 % | ± 1 % | ± 1 % | ± 1 % | ± 1 % | ± 2 % | ± 1 % | ± 1 % | ± 1 % | ± 1 % | ± 1 % | ± 1 % | ± 1 % | ± 1 % | ± 2 % | ± 1 % | ± 1 % | ± 1 % | ± 1 % | ± 1 % | ± 1 % | ± 1 % | ± 1 % | ± 1 % | ± 1 % |
Continuously adjustable power range | 60 W - 1000 W with active power regulation | 60 W - 2000 W with active power regulation | 80 W - 3000 W with active power regulation | 80 W - 3000 W with active power regulation | - | 80 W - 3000 W with active power regulation | 80 W - 3000 W with active power regulation | 80 W - 4000 W with active power regulation | 80 W - 4000 W with active power regulation | - | 80 W - 4000 W with active power regulation | 80 W - 4000 W with active power regulation | 100 W - 5000 W with active power regulation | 120 W - 5000 W with active power regulation | 120 W - 5000 W with active power regulation | 120 W - 5000 W with active power regulation | 120 W - 6000 W with active power regulation | 120 W - 6000 W with active power regulation | - | 120 W - 6000 W with active power regulation | 120 W - 6000 W with active power regulation | 160 W - 8000 W with active power regulation | 160 W with active power regulation | 160 W with active power regulation | 200 W - 10000 W with active power regulation | 240 W - 12000 W with active power regulation | 320 W - 16000 W with active power regulation | 400 W - 20000 W with active power regulation | 480 W - 24000 W with active power regulation |
Beam quality at the input coupling in the LLK | 2 mm▪mrad | 2 mm▪mrad | 2 mm▪mrad | 4 mm▪mrad | 4 mm▪mrad | 8 mm▪mrad | 25 mm▪mrad | 2 mm▪mrad | 4 mm▪mrad | 4 mm▪mrad | 8 mm▪mrad | 25 mm▪mrad | 2 mm▪mrad | 4 mm▪mrad | 8 mm▪mrad | 25 mm▪mrad | 2 mm▪mrad | 4 mm▪mrad | 4 mm▪mrad | 8 mm▪mrad | 25 mm▪mrad | 2 mm▪mrad | 4 mm▪mrad | 8 mm▪mrad | 4 mm▪mrad | 4 mm▪mrad | 4 mm▪mrad | 4 mm▪mrad | 4 mm▪mrad |
Numerical aperture on the output coupling after LLK | 0.1 | 0.1 | 0.1 | 0.1 | 0.1 | 0.1 | 0.1 | 0.1 | 0.1 | 0.1 | 0.1 | 0.1 | 0.1 | 0.1 | 0.1 | 0.1 | 0.1 | 0.1 | 0.1 | 0.1 | 0.1 | 0.1 | 0.1 | 0.1 | 0.1 | 0.1 | 0.1 | 0.1 | 0.1 |
Wavelength | 1030 nm | 1030 nm | 1030 nm | 1030 nm | 1030 nm | 1030 nm | 1030 nm | 1030 nm | 1030 nm | 1030 nm | 1030 nm | 1030 nm | 1030 nm | 1030 nm | 1030 nm | 1030 nm | 1030 nm | 1030 nm | 1030 nm | 1030 nm | 1030 nm | 1030 nm | 1030 nm | 1030 nm | 1030 nm | 1030 nm | 1030 nm | 1030 nm | 1030 nm |
Minimum laser light cable diameter | 50 μm | 50 μm | 50 μm | 100 μm | 100 μm | 200 μm | 600 μm | 50 μm | 100 μm | 100 μm | 200 μm | 600 μm | 50 μm | 100 μm | 200 μm | 600 μm | 50 μm | 100 μm | 100 μm | 200 μm | 600 μm | 50 μm | 100 μm | 200 μm | 100 μm | 100 μm | 100 μm | 100 μm | 100 μm |
Structural design | |||||||||||||||||||||||||||||
Width | 1175 mm | 1175 mm | 1175 mm | 1175 mm | 1175 mm | 1175 mm | 1175 mm | 1175 mm | 1175 mm | 1175 mm | 1175 mm | 1175 mm | 1175 mm | 1175 mm | 1175 mm | 1175 mm | 1620 mm | 1175 mm | 1175 mm | 1175 mm | 1175 mm | 1620 mm | 1175 mm | 1175 mm | 1620 mm | 1620 mm | 2150 mm | 2150 mm | 2150 mm |
Height | 1430 mm | 1430 mm | 1430 mm | 1430 mm | 1430 mm | 1430 mm | 1430 mm | 1430 mm | 1430 mm | 1430 mm | 1430 mm | 1430 mm | 1430 mm | 1430 mm | 1430 mm | 1430 mm | 1475 mm | 1430 mm | 1430 mm | 1430 mm | 1430 mm | 1475 mm | 1430 mm | 1430 mm | 1475 mm | 1475 mm | 1600 mm | 1600 mm | 1600 mm |
Depth | 725 mm | 725 mm | 725 mm | 725 mm | 725 mm | 725 mm | 725 mm | 725 mm | 725 mm | 725 mm | 725 mm | 725 mm | 725 mm | 725 mm | 725 mm | 725 mm | 920 mm | 725 mm | 725 mm | 725 mm | 725 mm | 920 mm | 725 mm | 725 mm | 920 mm | 920 mm | 1200 mm | 1200 mm | 1200 mm |
Maximum number of laser light cables | 2 | 2 | 2 | 2 | 1 | 2 | 2 | 2 | 2 | 1 | 2 | 2 | 2 | 2 | 2 | 2 | 2 | 2 | 1 | 2 | 2 | 2 | 2 | 2 | 2 | 2 | 2 | 2 | 2 |
Maximum number of laser light cables for extended device size | 4 | 4 | 4 | 4 | - | 4 | 4 | 4 | 4 | - | 4 | 4 | 4 | 4 | 4 | 4 | - | 4 | - | 4 | 4 | - | 4 | 4 | - | - | - | - | - |
Installation | |||||||||||||||||||||||||||||
Protection class | IP54 | IP54 | IP54 | IP54 | IP54 | IP54 | IP54 | IP54 | IP54 | IP54 | IP54 | IP54 | IP54 | IP54 | IP54 | IP54 | IP54 | IP54 | IP54 | IP54 | IP54 | IP54 | IP54 | IP54 | IP54 | IP54 | IP54 | IP54 | IP54 |
Ambient temperature | 10 °C - 50 °C | 10 °C - 50 °C | 10 °C - 50 °C | 10 °C - 50 °C | 10 °C - 45 °C | 10 °C - 50 °C | 10 °C - 50 °C | 10 °C - 50 °C | 10 °C - 50 °C | 10 °C - 45 °C | 10 °C - 50 °C | 10 °C - 50 °C | 10 °C - 50 °C | 10 °C - 50 °C | 10 °C - 50 °C | 10 °C - 50 °C | 10 °C - 50 °C | 10 °C - 50 °C | 10 °C - 45 °C | 10 °C - 50 °C | 10 °C - 50 °C | 10 °C - 50 °C | 10 °C - 50 °C | 10 °C - 50 °C | 10 °C - 50 °C | 10 °C - 50 °C | 10 °C - 50 °C | 10 °C - 50 °C | 10 °C - 50 °C |
TruDisk 1000
|
TruDisk 2000
|
TruDisk 3000
|
TruDisk 3001
|
TruDisk 3001 P
|
TruDisk 3002
|
TruDisk 3006
|
TruDisk 4000
|
TruDisk 4001
|
TruDisk 4001 P
|
TruDisk 4002
|
TruDisk 4006
|
TruDisk 5000
|
TruDisk 5001
|
TruDisk 5002
|
TruDisk 5006
|
TruDisk 6000
|
TruDisk 6001
|
TruDisk 6001 P
|
TruDisk 6002
|
TruDisk 6006
|
TruDisk 8000
|
TruDisk 8001
|
TruDisk 8002
|
TruDisk 10001
|
TruDisk 12001
|
TruDisk 16001
|
TruDisk 20001
|
TruDisk 24001
|
|
---|---|---|---|---|---|---|---|---|---|---|---|---|---|---|---|---|---|---|---|---|---|---|---|---|---|---|---|---|---|
Laser parameters | |||||||||||||||||||||||||||||
Laser Power | 1000 W 1 | 2000 W 1 | 3000 W 1 | 3000 W 1 | 3000 W 1 | 3000 W 1 | 3000 W 1 | 4000 W 1 | 4000 W 1 | 4000 W 1 | 4000 W 1 | 4000 W 1 | 5000 W 1 | 5000 W 1 | 5000 W 1 | 5000 W 1 | 6000 W 1 | 6000 W 1 | 6000 W 1 | 6000 W 1 | 6000 W 1 | 8000 W 1 | 8000 W 1 | 8000 W 1 | 10000 W 1 | 12000 W 1 | 16000 W 1 | 20000 W 1 | 24000 W 1 |
Typical power constancy at rated power over 8 hours at constant ambient temperature | ± 0.5 % | ± 0.5 % | ± 0.5 % | ± 0.5 % | ± 1 % | ± 0.5 % | ± 0.5 % | ± 0.5 % | ± 0.5 % | ± 1 % | ± 0.5 % | ± 0.5 % | ± 0.5 % | ± 0.5 % | ± 0.5 % | ± 0.5 % | ± 0.5 % | ± 0.5 % | ± 1 % | ± 0.5 % | ± 0.5 % | ± 0.5 % | ± 0.5 % | ± 0.5 % | ± 0.5 % | ± 0.5 % | ± 0.5 % | ± 0.5 % | ± 0.5 % |
Maximum power constancy at rated power over 8 hours at constant ambient temperature | ± 1 % | ± 1 % | ± 1 % | ± 1 % | ± 2 % | ± 1 % | ± 1 % | ± 1 % | ± 1 % | ± 2 % | ± 1 % | ± 1 % | ± 1 % | ± 1 % | ± 1 % | ± 1 % | ± 1 % | ± 1 % | ± 2 % | ± 1 % | ± 1 % | ± 1 % | ± 1 % | ± 1 % | ± 1 % | ± 1 % | ± 1 % | ± 1 % | ± 1 % |
Continuously adjustable power range | 60 W - 1000 W with active power regulation | 60 W - 2000 W with active power regulation | 80 W - 3000 W with active power regulation | 80 W - 3000 W with active power regulation | - | 80 W - 3000 W with active power regulation | 80 W - 3000 W with active power regulation | 80 W - 4000 W with active power regulation | 80 W - 4000 W with active power regulation | - | 80 W - 4000 W with active power regulation | 80 W - 4000 W with active power regulation | 100 W - 5000 W with active power regulation | 120 W - 5000 W with active power regulation | 120 W - 5000 W with active power regulation | 120 W - 5000 W with active power regulation | 120 W - 6000 W with active power regulation | 120 W - 6000 W with active power regulation | - | 120 W - 6000 W with active power regulation | 120 W - 6000 W with active power regulation | 160 W - 8000 W with active power regulation | 160 W with active power regulation | 160 W with active power regulation | 200 W - 10000 W with active power regulation | 240 W - 12000 W with active power regulation | 320 W - 16000 W with active power regulation | 400 W - 20000 W with active power regulation | 480 W - 24000 W with active power regulation |
Beam quality at the input coupling in the LLK | 2 mm▪mrad | 2 mm▪mrad | 2 mm▪mrad | 4 mm▪mrad | 4 mm▪mrad | 8 mm▪mrad | 25 mm▪mrad | 2 mm▪mrad | 4 mm▪mrad | 4 mm▪mrad | 8 mm▪mrad | 25 mm▪mrad | 2 mm▪mrad | 4 mm▪mrad | 8 mm▪mrad | 25 mm▪mrad | 2 mm▪mrad | 4 mm▪mrad | 4 mm▪mrad | 8 mm▪mrad | 25 mm▪mrad | 2 mm▪mrad | 4 mm▪mrad | 8 mm▪mrad | 4 mm▪mrad | 4 mm▪mrad | 4 mm▪mrad | 4 mm▪mrad | 4 mm▪mrad |
Numerical aperture on the output coupling after LLK | 0.1 | 0.1 | 0.1 | 0.1 | 0.1 | 0.1 | 0.1 | 0.1 | 0.1 | 0.1 | 0.1 | 0.1 | 0.1 | 0.1 | 0.1 | 0.1 | 0.1 | 0.1 | 0.1 | 0.1 | 0.1 | 0.1 | 0.1 | 0.1 | 0.1 | 0.1 | 0.1 | 0.1 | 0.1 |
Wavelength | 1030 nm | 1030 nm | 1030 nm | 1030 nm | 1030 nm | 1030 nm | 1030 nm | 1030 nm | 1030 nm | 1030 nm | 1030 nm | 1030 nm | 1030 nm | 1030 nm | 1030 nm | 1030 nm | 1030 nm | 1030 nm | 1030 nm | 1030 nm | 1030 nm | 1030 nm | 1030 nm | 1030 nm | 1030 nm | 1030 nm | 1030 nm | 1030 nm | 1030 nm |
Minimum laser light cable diameter | 50 μm | 50 μm | 50 μm | 100 μm | 100 μm | 200 μm | 600 μm | 50 μm | 100 μm | 100 μm | 200 μm | 600 μm | 50 μm | 100 μm | 200 μm | 600 μm | 50 μm | 100 μm | 100 μm | 200 μm | 600 μm | 50 μm | 100 μm | 200 μm | 100 μm | 100 μm | 100 μm | 100 μm | 100 μm |
Structural design | |||||||||||||||||||||||||||||
Width | 1175 mm | 1175 mm | 1175 mm | 1175 mm | 1175 mm | 1175 mm | 1175 mm | 1175 mm | 1175 mm | 1175 mm | 1175 mm | 1175 mm | 1175 mm | 1175 mm | 1175 mm | 1175 mm | 1620 mm | 1175 mm | 1175 mm | 1175 mm | 1175 mm | 1620 mm | 1175 mm | 1175 mm | 1620 mm | 1620 mm | 2150 mm | 2150 mm | 2150 mm |
Height | 1430 mm | 1430 mm | 1430 mm | 1430 mm | 1430 mm | 1430 mm | 1430 mm | 1430 mm | 1430 mm | 1430 mm | 1430 mm | 1430 mm | 1430 mm | 1430 mm | 1430 mm | 1430 mm | 1475 mm | 1430 mm | 1430 mm | 1430 mm | 1430 mm | 1475 mm | 1430 mm | 1430 mm | 1475 mm | 1475 mm | 1600 mm | 1600 mm | 1600 mm |
Depth | 725 mm | 725 mm | 725 mm | 725 mm | 725 mm | 725 mm | 725 mm | 725 mm | 725 mm | 725 mm | 725 mm | 725 mm | 725 mm | 725 mm | 725 mm | 725 mm | 920 mm | 725 mm | 725 mm | 725 mm | 725 mm | 920 mm | 725 mm | 725 mm | 920 mm | 920 mm | 1200 mm | 1200 mm | 1200 mm |
Maximum number of laser light cables | 2 | 2 | 2 | 2 | 1 | 2 | 2 | 2 | 2 | 1 | 2 | 2 | 2 | 2 | 2 | 2 | 2 | 2 | 1 | 2 | 2 | 2 | 2 | 2 | 2 | 2 | 2 | 2 | 2 |
Maximum number of laser light cables for extended device size | 4 | 4 | 4 | 4 | - | 4 | 4 | 4 | 4 | - | 4 | 4 | 4 | 4 | 4 | 4 | - | 4 | - | 4 | 4 | - | 4 | 4 | - | - | - | - | - |
Installation | |||||||||||||||||||||||||||||
Protection class | IP54 | IP54 | IP54 | IP54 | IP54 | IP54 | IP54 | IP54 | IP54 | IP54 | IP54 | IP54 | IP54 | IP54 | IP54 | IP54 | IP54 | IP54 | IP54 | IP54 | IP54 | IP54 | IP54 | IP54 | IP54 | IP54 | IP54 | IP54 | IP54 |
Ambient temperature | 10 °C - 50 °C | 10 °C - 50 °C | 10 °C - 50 °C | 10 °C - 50 °C | 10 °C - 45 °C | 10 °C - 50 °C | 10 °C - 50 °C | 10 °C - 50 °C | 10 °C - 50 °C | 10 °C - 45 °C | 10 °C - 50 °C | 10 °C - 50 °C | 10 °C - 50 °C | 10 °C - 50 °C | 10 °C - 50 °C | 10 °C - 50 °C | 10 °C - 50 °C | 10 °C - 50 °C | 10 °C - 45 °C | 10 °C - 50 °C | 10 °C - 50 °C | 10 °C - 50 °C | 10 °C - 50 °C | 10 °C - 50 °C | 10 °C - 50 °C | 10 °C - 50 °C | 10 °C - 50 °C | 10 °C - 50 °C | 10 °C - 50 °C |
The technical data of all product versions as a download.
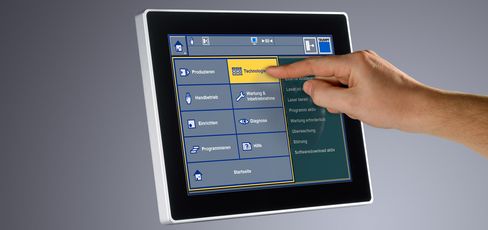
TruControl
TruControl is the control software for your TRUMPF solid-state laser – for quick and simple operation. You can program pulse shapes individually to match the application. The laser power is controlled in real time to ensure maximum reproducibility of your process results. In order to retrace important quality data of your produced parts even years later, the optional DataStore software module records all data relevant to quality.
If external controls are present, TruControl will communicate with them via all standard interfaces. Inputs are made via the touchscreen of the operating panel or via a panel PC. You can integrate your laser into the network via Ethernet and connect multiple PCs.
With TRUMPF you have the ability to adapt your solid-state laser to your installation and operating situation with flexibility. This applies, for example, to all beam guidance components and the control. You also have several options for the cooling water supply. Interfaces for different optics are provided right from the start. To save costs, your beam source can supply several work stations at the same time. The TRUMPF Remote Service helps you to ensure your system remains available, anywhere and at any time.
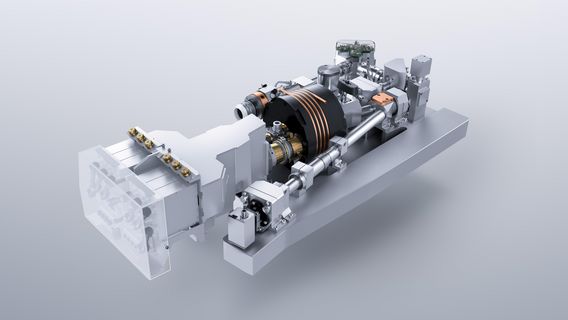
There are many different options for the beam guidance that will enable you to plan flexibly with your laser. The plug & play optical laser cables can be easily connected to different work stations. Here, you choose the number of fiber outlets up to a total of six. The laser power can be divided across the outlets with flexibility. This allows multiple work stations to operate simultaneously with split laser power or one after the other at full laser power. The modular design means that the laser power and the number of outlets can be changed retrospectively in the field at any time.
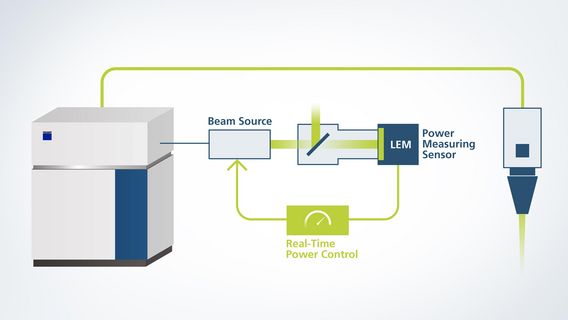
Instead of manual control, the power of the TruDisk can be controlled in real time. The active laser power control stabilizes the laser power to deviations of +/- 1% and thereby keeps the process constant, regardless of ambient influences. You therefore, benefit from the greatest power stability on the market – throughout the entire service life of your laser.
Benefit from virtually spatter-free laser welding and top welding seam quality with the BrightLine Weld option. You have the choice – increase your productivity considerably due to significantly increased feed rates, or reduce your energy costs by up to 40%. In doing so, you can reduce your machine downtimes and operating costs, as post-processing is also reduced.
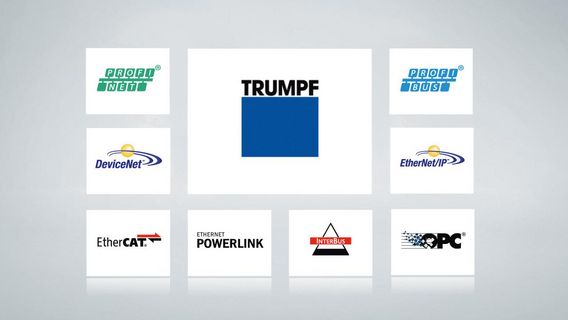
Interfaces are key for the integration of a TruDisk laser in your machine or production line. The solid-state lasers from TRUMPF offer interfaces to all common fieldbus systems. Also available: real-time interface, parallel digital I/O, interface for process sensor systems, OPC UA software interface, analog input board, interface for intelligent TRUMPF optics (CFO, PFO).
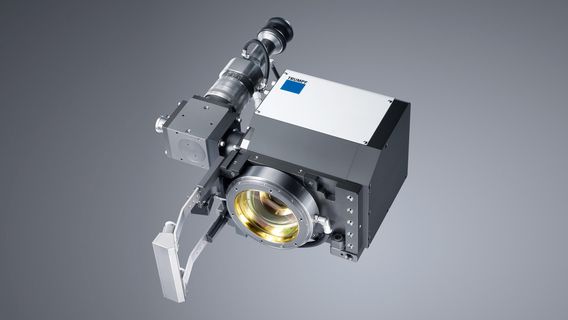
Intelligent optics can be synchronized with your laser via a dedicated interface. For example, the CFO focusing optics or PFO scanner optics can be used optimally for your purposes. You can program the processing optics easily via the laser control system. You do not need any additional PCs or control systems.

In the event of a fault, TRUMPF service experts will remotely access your laser via a secure remote connection. In many cases the fault can be remedied directly in this way, or the configuration of the laser can be modified in a way that permits you to continue manufacturing until the spare part arrives. This enables maximum availability for you.
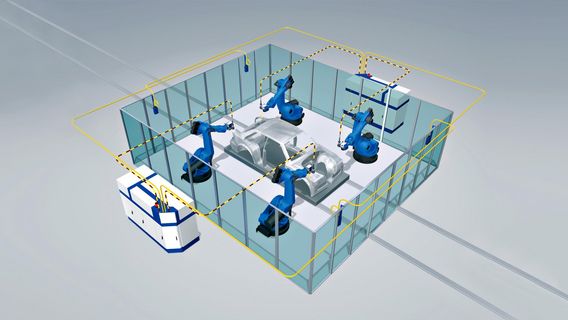
With the laser network, you can network one or more lasers with up to six work stations in each case. In the process, your laser either splits its power to multiple stations, or it supplies them by taking turns with full power. This will enable you to combine different applications, such as welding and cutting.
With the integrated compressor cooler you can benefit from a maximum cooling water supply temperature of 38°C – an external cooler is not required at all. The laser still saves space here as the overall footprint is not increased even with the integrated compressor cooler. TruControl conveniently controls and monitors the cooler. You can also replace the entire cooler or refrigerant circuit quickly and flexibly.
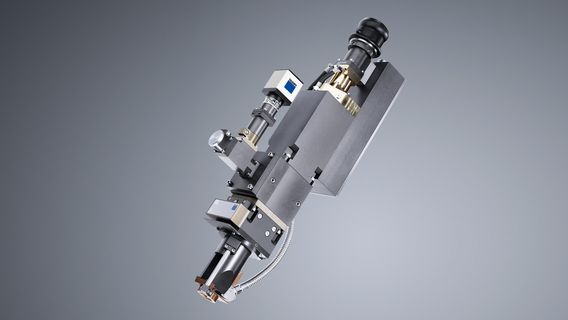
Processing optics and fiber optic cables can be cooled easily and conveniently using the laser cooling water. Separate cooling is therefore, not necessary.
The TRUMPF sensor systems mean that your production will always be both efficient and cost-effective. The sensor products VisionLine, CalibrationLine or integrated pyrometers ensure stable processes by monitoring all the procedures in laser production and make a significant contribution towards your process reliability. Processing continues unimpeded during the measurement – no interruptions are required, saving you valuable production time.
Image processing
TRUMPF VisionLine image processing detects features on the components and ensures that welding is always in the correct location.
Calibration
The TRUMPF CalibrationLine tool checks and corrects the focal position and laser power on the workpiece at regular, individually definable intervals.
Seam position control
The sensor system detects the joint gap and controls the welding position during the welding process.
Temperature control
The TRUMPF temperature control ensures high-quality visual results for plastic welding.
Welding depth monitoring
The TRUMPF welding depth monitoring warns the user if the process deviates from the preset welding depth.
Lasers and laser systems – with us, the perfect pair. All beam sources are optimally attuned to the requirements of the TRUMPF laser systems. You can choose between numerous versions and options, resulting in a system which is precisely tailored to your task. It is, of course, also possible to integrate our lasers directly into your production lines.
TRUMPF offers you all the components you need for beam guidance from the laser to the workpiece. This also applies for various focusing optics which have proven themselves to be precise and reliable over many years of industrial use. The optics can be easily integrated – both in stand-alone processing stations as well as in complete production lines. The modular structure enables the optics to be continually adapted to the laser types as well as various processing situations.
Focusing optics
Regardless of whether you are welding, cutting, ablating, heat treating, or drilling, you can count on high-quality process results with robust focusing optics from TRUMPF.
Programmable focusing optics
The ideal optics for remote processing
This product range and information may vary depending on the country. Subject to changes to technology, equipment, price, and range of accessories. Please get in touch with your local contact person to find out whether the product is available in your country.
Footnotes-
The laser power at the workpiece may deviate from the rated power depending on the optics configuration.