The TruPrint 2000 offers you design freedom in a 200 x 200 x 200 mm installation space. The optimized optical design enables high quality even in the corners of the build plate - and all this without any disturbing screws on the build plate.
In the dental sector, 36% more RPDs can be accommodated on the same plate compared to a round plate. The mold and die industry also benefits from the extra surface area of the machine and laser power.
Productivity squared
Highest quality, robust processes and high productivity - that's what the TruPrint 2000 stands for. With a build volume of 200 x 200 mm footprint and a height of 200 mm, it offers ideal possibilities. Thanks to the expanded build volume and the new basic spot configuration with 80 µm, the TruPrint 2000 is the perfect system for the tool industry as well as for applications in the dental, medical or general industry.
For example, up to 36% more RPDs (Removable Partial Denture) can be placed on the square build plate compared to a 200 mm diameter round build plate. With the 80 µm spot Fullfield Multilaser, users also benefit from our new dental parameters that allow them to print up to 30 RPDs in roughly 4 hours.
Thanks to the square base and build plate fixture without screws on top, the parts can be easily arranged – up into the corners.
The 500 W laser power and 80 µm beam diameter with the multilaser option, provide highly productive and excellent results.
The combination of building volume, laser power and coating time results in an economical machine concept for your series production.
With adjustable spot size (55/80 µm) and detailed process analysis, you enjoy high process flexibility and advanced monitoring.
Benefit from easy and safe powder handling under inert, closed powder circuit.
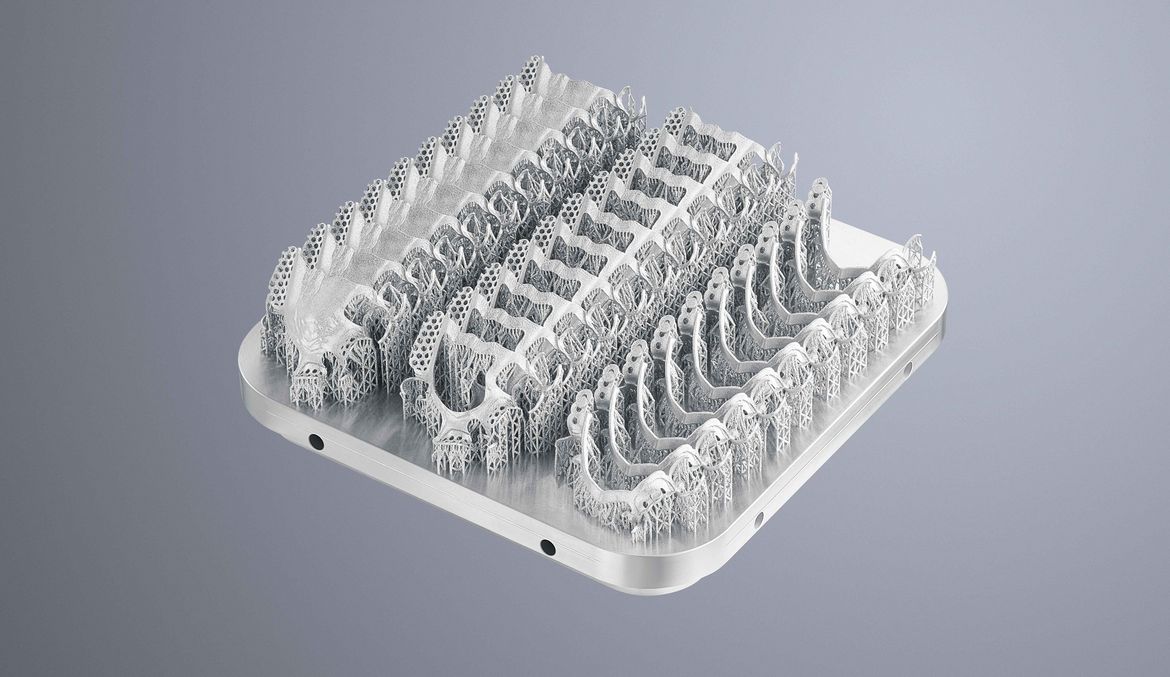
Removable partial dentures (RPDs)
Thanks to the 80 µm beam diameter of the TruPrint 2000's laser, you achieve high productivity and very high surface quality and detail accuracy, which is especially advantageous for dental components. In addition, the low surface roughness saves you rework.
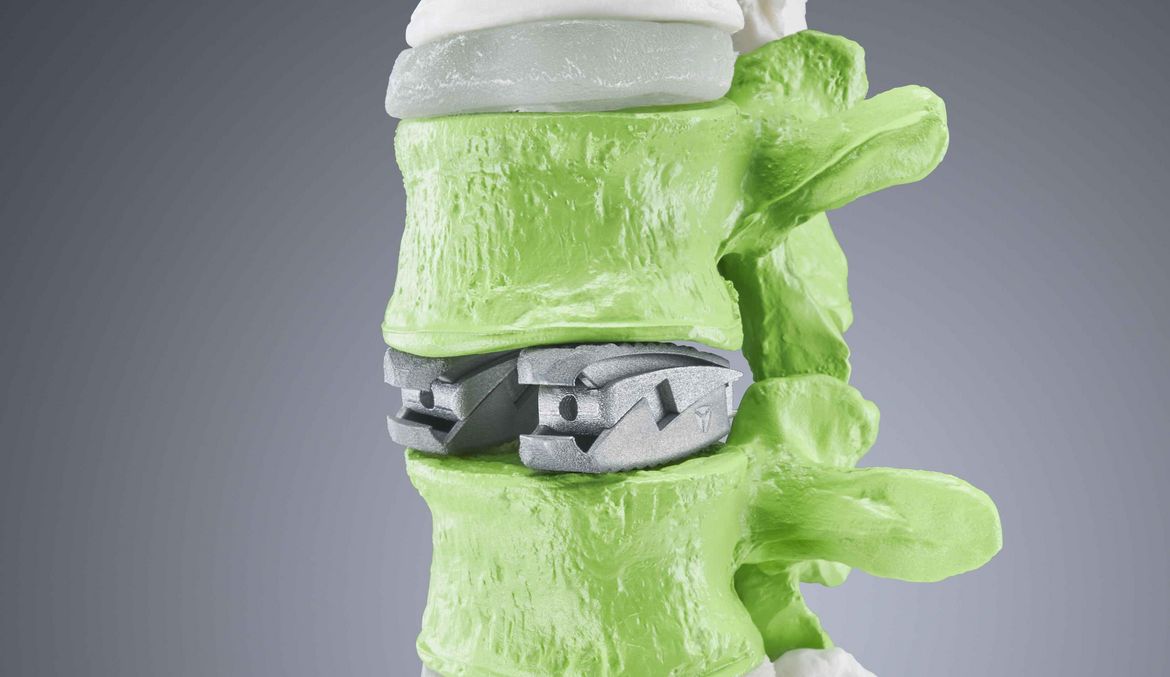
Spine Cages
With the TruPrint 2000 you always receive premium component quality according to the highest medical standards. The surface roughness improves osseointegration between bone and implant. Thanks to additive manufacturing, you gain new design freedom that enables additional functionalization. With additively manufactured spine cages, patients benefit from a faster healing process and significantly improved long-term stability.
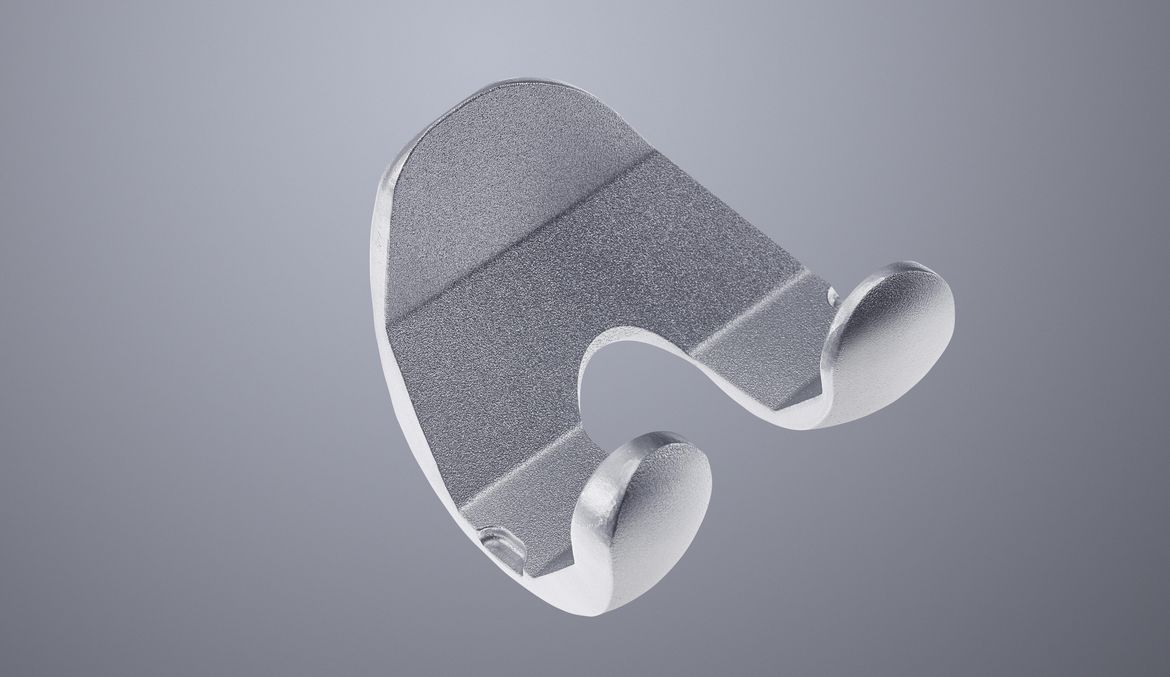
Knee implant
With the TruPrint 2000, you benefit from a level of detail that is particularly predestined for medical implants such as the femoral component of a total knee replacement. This is because additive manufacturing allows the finest lattice structures to be printed; osseointegration is significantly improved.

3D printed mold inserts for injection molding
Filigree cooling channels, which can be found, for example, in mold inserts with near-contour temperature control. This improved cooling of the injection molding tool can significantly reduce the cycle time for manufacturing gears, allowing a stable and safe production of plastic parts.
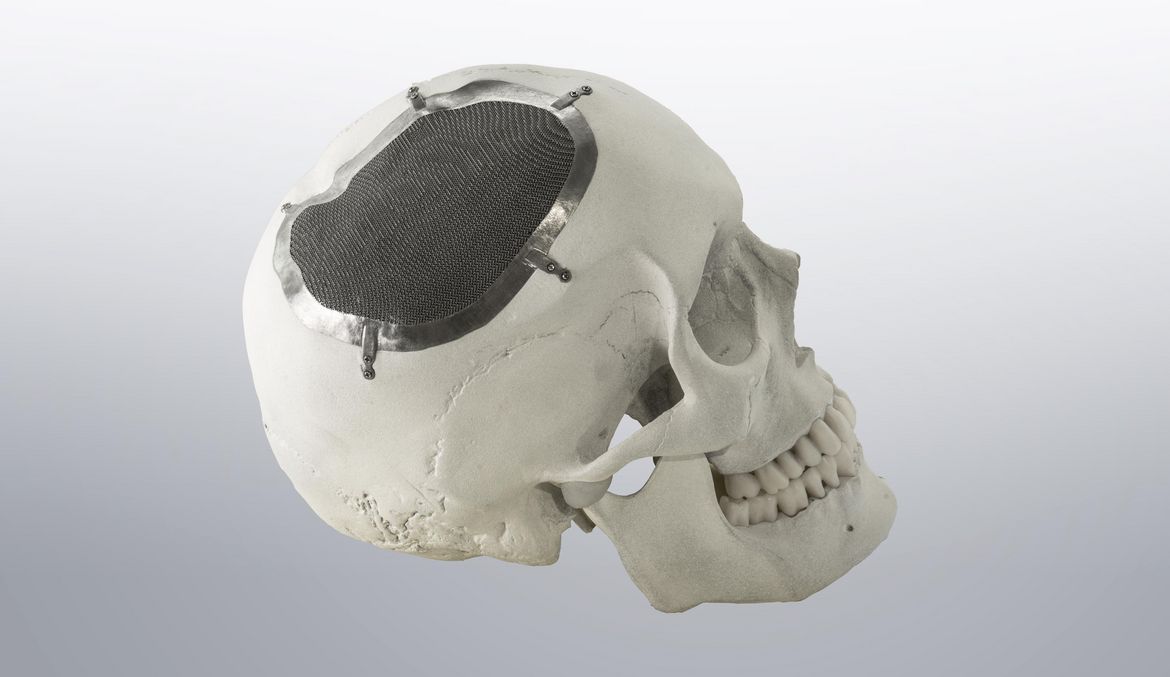
CMF Implant - Skull Plate
With the TruPrint 2000, you produce individual implants with the highest quality requirements in a qualified environment. The high-precision components with the material Ti6Al4VELI can be printed cost-efficiently with the system "on demand" within a very short time - even in series if required.
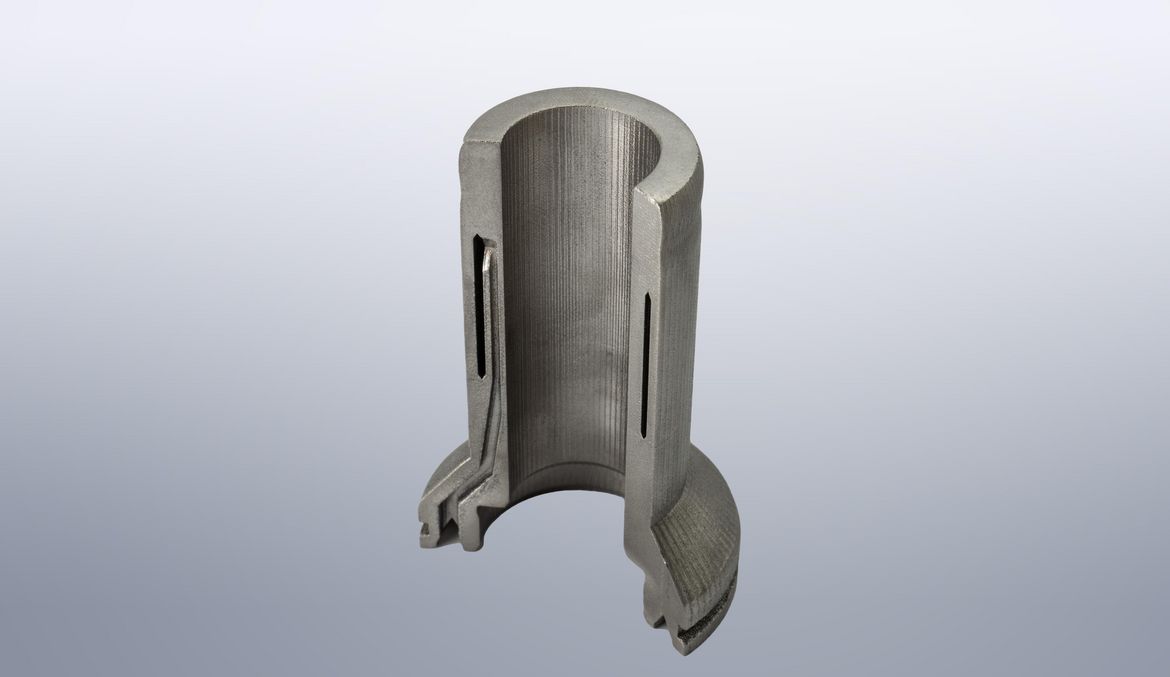
Expansion sleeve
A printed expansion sleeve made of the amorphous metal AMLOY ZR01 (AMZ4) has a low weight, which is made possible by the high elasticity and strength of the material - especially compared to crystalline materials. In addition, complex geometries can be printed directly in a component, eliminating the need for individual parts in the assembly. Created by Heraeus AMLOY
TruPrint 2000
|
|
---|---|
Build volume (cylinder) L x W x H | 202 mm x 202 mm x 200 mm |
Processable materials | Metal powders for welding, such as stainless steels, tool steels, and aluminum, nickel-based, cobalt-chrome or titanium alloys, amorphous metals. Current availability of materials and their parameters available on request. |
Preheating (standard) | Up to 200 °C |
Maximum laser power at the workpiece (TRUMPF fiber laser) | 300 W (Optional 500 W, single-laser or dual-laser) |
Beam diameter (standard) | 80 μm |
Beam diameter (option) | 55 μm - 80 μm |
Layer thickness | 20 - 100 μm |
Connection and consumption | |
Electrical connection (voltage) | 400 / 460 V |
Electrical connection (current intensity) | 32 A |
Electrical connection (line frequency) | 50 Hz / 60 Hz |
Shielding gas | Nitrogen, argon |
Structural design | |
Dimensions (W x H x D) | 2180 mm x 2030 mm x 1400 mm |
Weight (including powder) | 2500 kg |
The technical data of all product versions as a download.
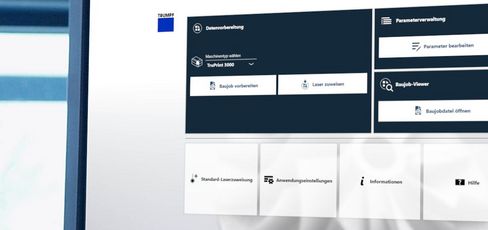
TruTops Print
With TruTops Print, TRUMPF offers the right software solution for getting the most out of TruPrint machines. The modern user interface clearly summarizes all functionalities and enables quick access to all functions. The high degree of flexibility and the individual options for data preparation, such as z-segmentation, as well as the intuitive and clear parameter management with fully accessible parameters, ensure maximum efficiency and productivity with the best print quality and reproducibility, as well as support-reduced overhang buildability. The high quality of the created vector data in WZA format can be verified with the integrated BuildJob Viewer.

Data preparation to match your workflow
For a seamless data preparation workflow, TruTops Print is already connected to numerous CAD/CAM systems. This gives you the greatest possible flexibility when selecting data preparation software. Decide for yourself which solution fits your workflow perfectly.
Increase your productivity with the Multilaser option: Two TRUMPF fiber lasers, each with 300 W resp. 500 W and a beam diameter of 55 or 80 µm, expose simultaneously in the installation space and thus flexibly generate up to 80 % more parts in the same time. In this way, you achieve faster parts availability and maximum flexibility for customer orders. In addition, since each contour is exposed by a laser, there are no "seams". You work with the Fullfield Multilaser with 100% overlap. The Automatic Multilaser Alignment option automatically monitors and calibrates the multilaser scan fields in relation to each other during the current build job - for optimum quality with multilaser parts.
You can automatically monitor the powder bed via an integrated camera in the TruPrint build chamber and automatic image processing. This gives you an overview of the component condition at all times and allows you to analyze the quality parameters layer by layer. The automatically correcting re-coating function checks the powder coating in the build area before melting. If the build area is not coated correctly, the coating is repeated.
Various options are available for your TruPrint to meet the verification requirement: Laser power calibration - also for multilasers, focus position measurement and scan field calibration - so you can measure, recalibrate if necessary and document your measurement results.
Deviations in the laser melting process can be detected at an early stage by means of sensors and critical areas on the component can be visualized. You can also monitor all melting baths in parallel - especially helpful with the Fullfield Multilaser option.
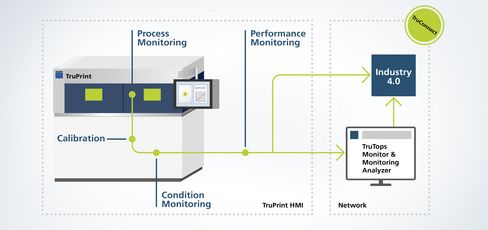
Monitoring
With the intelligent monitoring solutions from TRUMPF, you can easily monitor, analyze and calibrate the build process of TruPrint machines - allowing you to manufacture even more efficiently and achieve higher component quality. Professional monitoring enables the display and evaluation of sensor-based data. The range includes solutions for process, condition and performance monitoring. The monitoring results can be viewed directly on the HMI of the TruPrint machine or evaluated offline using the Monitoring Analyzer. In addition to transparency, TruTops Monitor gives you the option of remote access via PC or tablet. The OPC UA interface also offers you full flexibility with the connection to your own software solution. With the additionally available calibration functions, you can check the process-relevant parameters for optimal production conditions before the start of the construction job.
The inert machine concept of the TruPrint 2000 with Powder Preparation Station n enables very simple powder and parts handling under protective gas. The closed circuit effectively avoids powder contact and enables a high level of work safety. In addition, the material does not degrade due to the minimal oxygen contact.

Powder and parameters
High-quality metal powders are the basis for reliable process conditions in additive manufacturing. The combination of recommended powders and the right parameters leads to high-quality material properties for 3D-printed components.
This product range and information may vary depending on the country. Subject to changes to technology, equipment, price, and range of accessories. Please get in touch with your local contact person to find out whether the product is available in your country.
Find your additive manufacturing solution for dental technology now!
Use the TruPrint product finder to discover which TruPrint machine is best suited to your dental technology application!
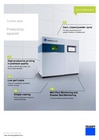