New concepts make it easier to integrate lasers into production processes // Easy integration of beam sources and their peripheral components in the digital world of the smart factory // Laser-based manufacturing processes are ready for Industry 4.0
TRUMPF showcases new concepts of integration and digital connectivity at LASYS laser exhibition
Ditzingen, June 5, 2018 – The high-tech company TRUMPF will be presenting hardware and digital solutions in the field of laser technology from June 5 to 7, 2018 at LASYS in Stuttgart (hall 4, booth C51). "No other tool can successfully handle so many different production processes," says Klaus Löffler, Managing Director of TRUMPF Laser Technology. "We're seeing a steady increase in the number of machine builders and system integrators that are incorporating laser technology into their products. Our goal is to offer attractive solutions based on an array of diverse technology modules that allow our customers to access and visualize machine and process data."
Intelligent optics and tailor-made sensor systems
Laser processes rely on flawless interaction between the beam source and processing optics. The simplest solution is for the laser control system to ensure optimum synchronization between the two components. Intelligent processing optics maintain constant contact with the process sensors and beam guidance systems. "Recent developments in process sensors have given new impetus to robot-controlled remote processing," says Till Schneider, Head of Laser Product Management at TRUMPF Laser- und Systemtechnik. "For example, today's systems can position a weld using a camera or OCT sensor connected to the optics and then monitor the process and control it in real time." What's more, modern scanner optics such as intelligent programmable focusing optics (I-PFO) control the robot movements and use a flexible and highly dynamic system of mirrors to aim their deflection of the laser beam at the required point within the three-dimensional working space. "It all sounds very complicated, but actually it's very easy to program because of the way we integrated the laser and I-PFO optics into a single system. TRUMPF provides software that can be used to simulate the component, optics and robot in order to optimize cycle times. Technicians on the shop floor can then implement and adjust the entire process on the robot manufacturer's control panel in the production facility itself," says Schneider. "That's where our experience with this process really comes to the fore," emphasizes Löffler. "It means we can support system integrators in programming, modifying and developing suitable optics for specialist applications."
New developments in beam guidance and shaping systems
The kind of solid-state lasers that TRUMPF is presenting at LASYS are finding favor in an increasing number of applications. There are three key reasons for this: simplified integration of the beam guidance system via laser light cables, flexible beam division or deflection in the TRUMPF Laser Network (TLN), and ongoing development of the TLN itself. TRUMPF is already developing hollow waveguides as a future form of laser light cable for ultrashort pulsed lasers.
Rapid progress is also being made in beam shaping systems for solid-state lasers. For example, TruDisk lasers now come with BrightLine Weld, a new feature that enables flexible distribution of the laser output between the inner and outer fiber core of the laser light cable. This produces different laser beams in the two cores. The system then positions one beam on top of the other on the workpiece, synchronizing the beams to create the best results for each particular process. This approach offers some major quality improvements and helps boost productivity. The patented BrightLine Weld technology can even be retrofitted to most existing laser installations and can be applied to multiple laser outputs from a single beam source.
A treasure trove of data
Complete laser processes - from the power socket to the process zone - can now be mapped in the form of data and then monitored and controlled. That's why the optics, sensors and beam sources TRUMPF is presenting at this year's LASYS are the perfect choice of tool to integrate in the digital world of the smart factory. The data they generate can be made available to many of the applications that are becoming standard in Industry 4.0, such as quality data storage and cockpits for data visualization. With remote access to the laser via a secure IT system, customers can also choose to benefit from the expertise and experience TRUMPF technicians have accumulated for a range of applications by taking advantage of services such as condition-based monitoring and predictive maintenance. The data is transmitted through encrypted channels to a cloud, where a combination of algorithms and real TRUMPF experts evaluate it to produce trend analyses. That paves the way for predicting anomalies and their effects in the machining process, leading to major improvements in machine availability.
The new TruFiber generation
Beam sources themselves also contribute to creating simpler and smarter ways to configure optimum integration in higher-level machines. Good examples include the TruDisk beam sources - on show at LASYS in the form of the new TruDisk 3000 - as well as the new generation of TruFiber beam sources, such as the TruFiber 2000, which TRUMPF is also showcasing at LASYS.
Easy integration stems from a number of different factors, including a compact laser design, flexible interfaces to all common fieldbus systems, and the maximum laser safety rating with Performance Level 'e'. Other helpful features include integrated laser power control in real time for even more reliable process results, the option of incorporating a compressor cooling system in the laser cabinet, and cooling of peripheral components via the beam source.
The way these beam sources work in practice reflects a trend toward better beam quality - a trend that has multiple explanations. "On the one hand, beam quality is one of the keys to overall process productivity," says Schneider. The TruFiber 2000 generates perfect single-mode output, enabling very small focal diameters with high power densities. "But, on top of that, better quality beams enable a larger scan field during remote processing," says Schneider. Both beam sources are an excellent choice not only for welding processes with linear feed, but also wobbling welding, a technique that involves oscillation overlaid with forward motion of the beam. The process offers improvements in weld seam quality as well as flexible adjustment of the weld seam width. The very high beam quality in this case yields greater penetration depth without having to increase laser power.
Digital photographs in print-ready resolution are available to illustrate this press release. They may only be used for editorial purposes. Use is free of charge when credit is given as "Photo: TRUMPF". Graphic editing – except for dropping out the main motive - is prohibited.
İrtibat yetkilisi
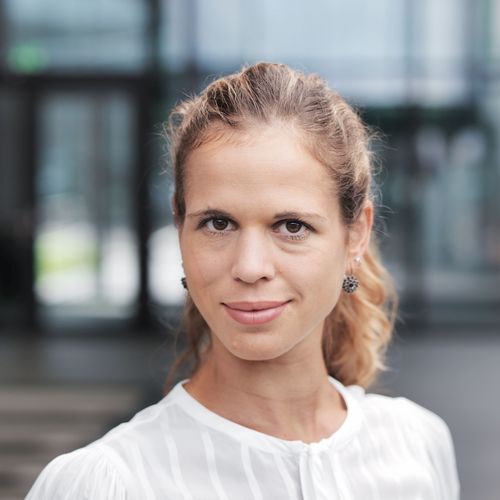