From casting to milling to 3D printing: the history of the development of metal processing is also reflected in dental technology. Metal dental dentures, created with the casting technique, are now made using 3D printers. The procedure is even quicker and more affordable than when using milling technology. The dental industry has different metal 3D printing solutions for the additive manufacturing of dentures at its disposal. Using powder, the laser creates new workpieces layer by layer using the laser metal fusion technique (LMF). This procedure, also called selective laser melting (SLM) or powder bed fusion (PBD), is used in the highly precise manufacturing of implant-supported dental prostheses, for example. All in all, it is easy to implement a variety of individual geometries. Separation between pontics is eliminated, a milling radius correction is no longer necessary. The advantage: more space in important areas. Furthermore, retentions for plastic veneers and undercuts can be created effortlessly.
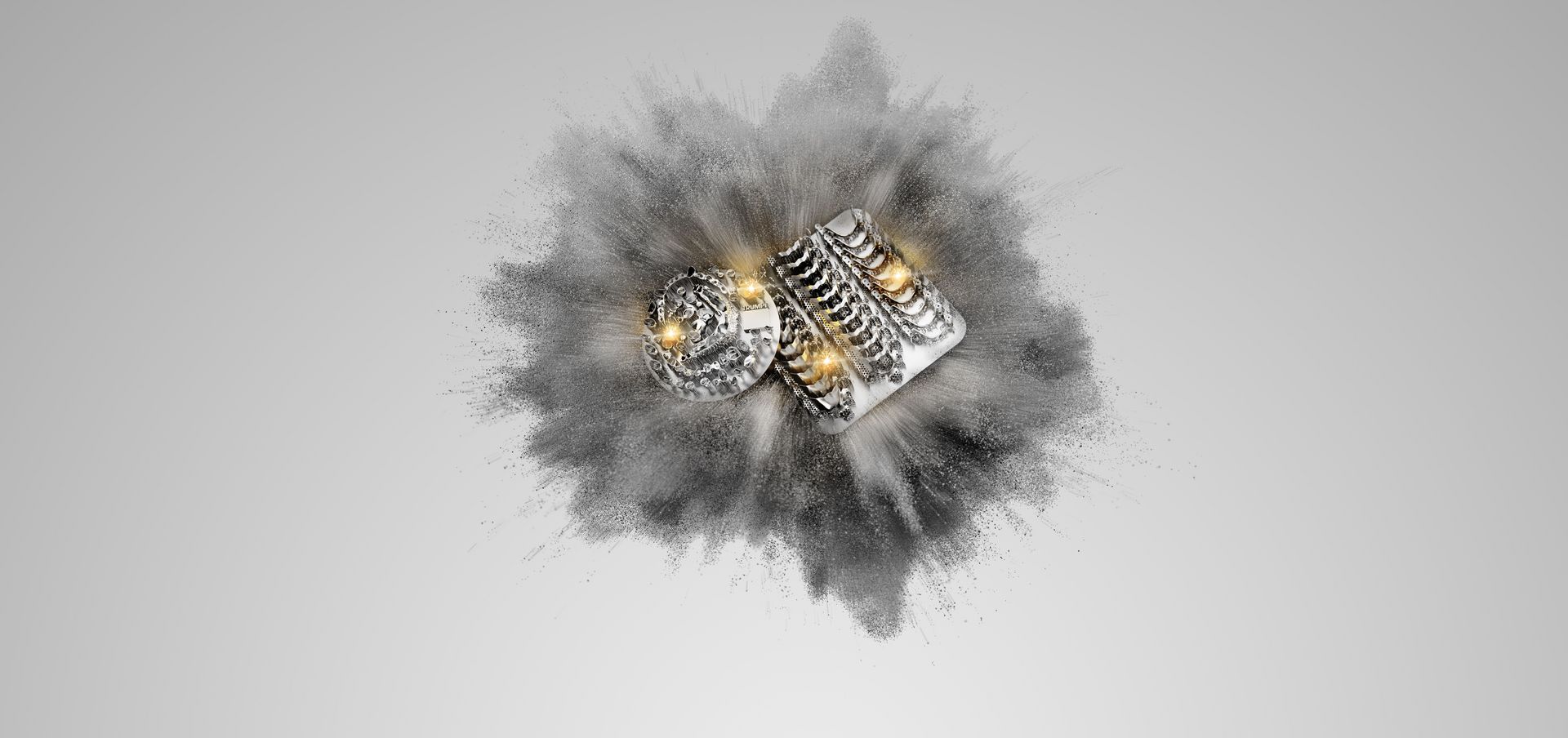
3D printing in dental technology
The production of implant-supported dental prostheses is the fastest growing segment in the dental industry all over the world. This is why it is becoming more and more important for dental laboratories to tap into this lucrative pioneering field, using highly productive 3D printers in response to the growing pressures of cost and competition in the industry. These pages will give you an overview of the advantages and benefits of metal 3D printers for your future business. You will also find out exactly which 3D printers, software solutions and services will provide you with the ideal set-up.
What is metal 3D dental printing and which procedures are available?
What are the advantages of metal 3D printing in dental technology?
Faster, more affordable and new dental indications thanks to a hybrid process chain. The investment in additive manufacturing is worthwhile for dental laboratories in many respects.
Many individual geometries can be implemented easily and productively with powder-based laser metal fusion (LMF). Functions such as Multilaser or Multiplate ensure efficient production of customized dental components.
A dental 3D printer produces dental prostheses much more quickly than conventional methods such as milling technologies. But metal 3D printers do not just benefit production, preparation is also much quicker thanks to the digital process chain. This means that dental technicians can work with digital data records transmitted to dental laboratories in real time. Thanks to digital molding, there are no plaster casts or silicone imprints.
With dental 3D printing, you can produce a large number of dental indications precisely, saving materials at the same time. Thanks to the digital connection of the TruPrint systems with milling machines, indications such as implant-supported crowns and bridges, telescopic crowns and secondary parts can be produced economically within a hybrid procedure. In this case, we truly see the benefits of direct printing of individual single abutments on special base parts (preforms) made of titanium or cobalt-chromium.
As the 3D printer only processes as much metal powder as it actually needs, users save material and money. At the same time, the sustainable use of materials such as cobalt-chromium is beneficial to the environment. Excess powder can simply be reused after the printing process. 3D printers can ideally develop complex geometries such as corners and edges within the smallest amount of space. This means that dental technicians can increase the quality of their manufactured parts significantly.
Thanks to open interfaces, the 3D printer can be ideally integrated in the existing CAD/CAM process chains. The result is that dental laboratories do not have to convert their entire system. The advantages of this hybrid workflow: shorter production times, lower costs.
3D dental printing in metal - questions and answers
Depending on the shape, up to 100 crowns can be fitted onto one standard plate (diameter: approx. 100 mm).
A build plate with approximately 100 crowns is printed in around three hours using a double laser. A single laser needs approximately five hours.
Up to 30 RPDs
A build plate with 30 RPDs is printed in around four hours using a double laser. Thus the print duration per RPD is about 8 minutes.
Crowns, bridges, separators and superstructures as well as all implant-supported objects such as single abutments, telescopic crowns, primary and secondary parts, orthodontic parts, cast metal partial dentures and partial prostheses can be produced with additive manufacturing.
Cobalt-chromium and titanium can be effortlessly processed by a 3D printer. Thanks to the open system architecture, there are generally no restrictions concerning the material used. In addition, plug-and-play solutions facilitate a simple and quick start for many powders.
It is very easy to set up 3D printers in dental laboratories. They fit through a normal standard door and in an elevator. They do not need any compressed air and are operated with normal electric power (230V). One machine weighs 650 kg (including powder).
TruPrint 1000 and TruPrint 2000 operate with gas cylinders.
Book an appointment for our AM Showroom now – in person or online!
Immerse yourself in the additive future of the dental sector with our industry experts, and experience our machines live in action! Or take advantage of an online machine presentation in our Virtual AM Showroom.
Hybrid workflow
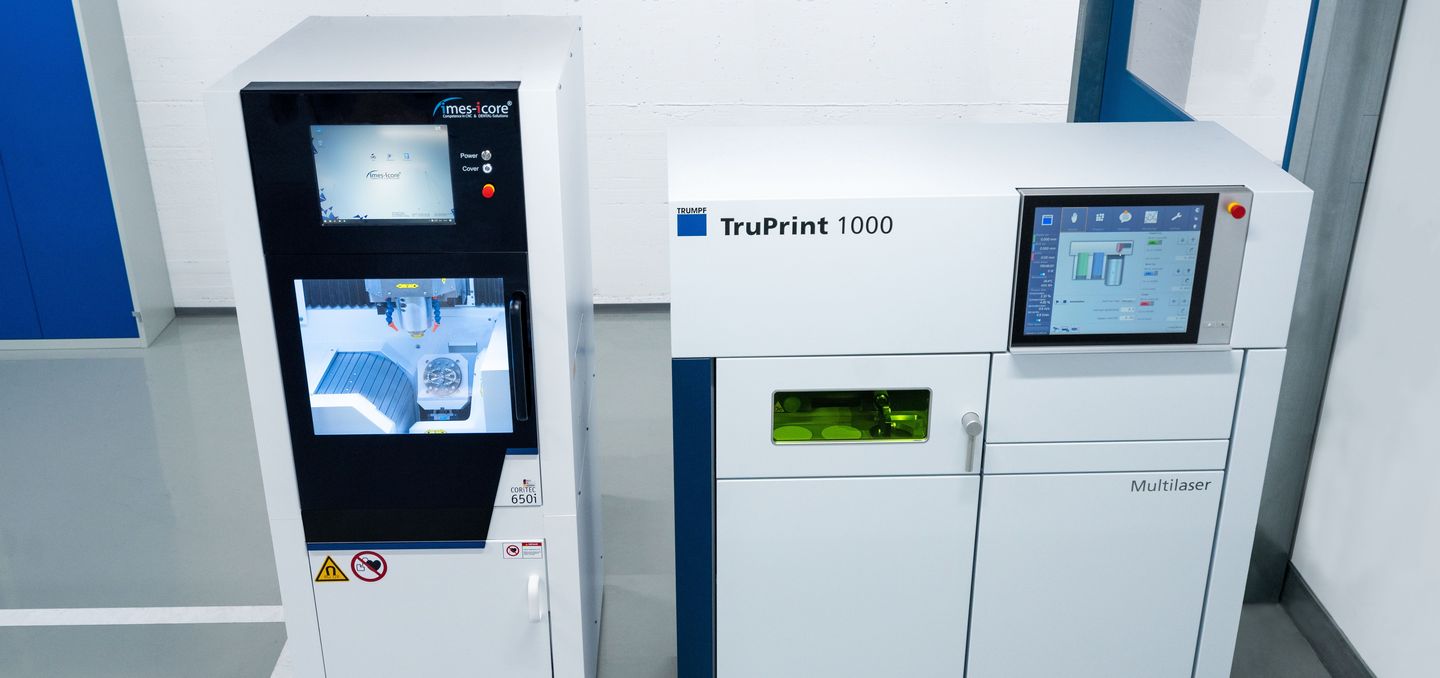
Linking up with the milling machine is an important milestone on the journey to automated series production in dental technology .
Hybrid workflow: this is how you prepare your dental prostheses production for the future
There is a clear trend: dental prostheses are being increasingly produced in bulk in automated processes. It is therefore becoming more and more important for dental laboratories to rely on a consistently digitized workflow and an intelligent combination of 3D printing and milling technology in order to facilitate competitive production of as many components as possible to a high quality standard. Open IT interfaces and cooperation with partners form the basis of this hybrid process chain which has two primary advantages: shorter production times and decreased costs.
Integration in the digital process chain
Linking up with the milling machine is an important milestone on the journey to automated series production in dental technology. Experts have extended the IT interface of additive production systems for this purpose. The hybrid workflow makes it possible to print and subsequently post-process implant-supported dentures and telescopic parts with milling technology. Thanks to the highly precise results, implants and dental prostheses can be safely screwed in place.
This is what a hybrid workflow looks like in practice
Book an appointment for our AM Showroom now – in person or online!
Immerse yourself in the additive future of the dental sector with our industry experts, and experience our machines live in action. Or take advantage of an online machine presentation in our Virtual AM Showroom.
Our machines for your additive future

With the additive production systems TruPrint 1000 and TruPrint 2000 from TRUMPF, you can print a wide range of dental indications high productively and precisely while saving materials.
Step it up a notch: with the TruPrint systems and the Multilaser option
TruPrint 1000 and TruPrint 2000 with the multilaser function are the most productive 3D printers for metal dental components to date. With this function, 3D printers from TRUMPF produce much more efficiently than conventional methods such as milling machines. There's even more: the possibility of linking both machines to milling stations is another highlight. This increases the range of applications for dental 3D printers. We also have the TruPrint 1000 Basic Edition in our lineup. It is affordable and robust, intuitive to use and reliable.
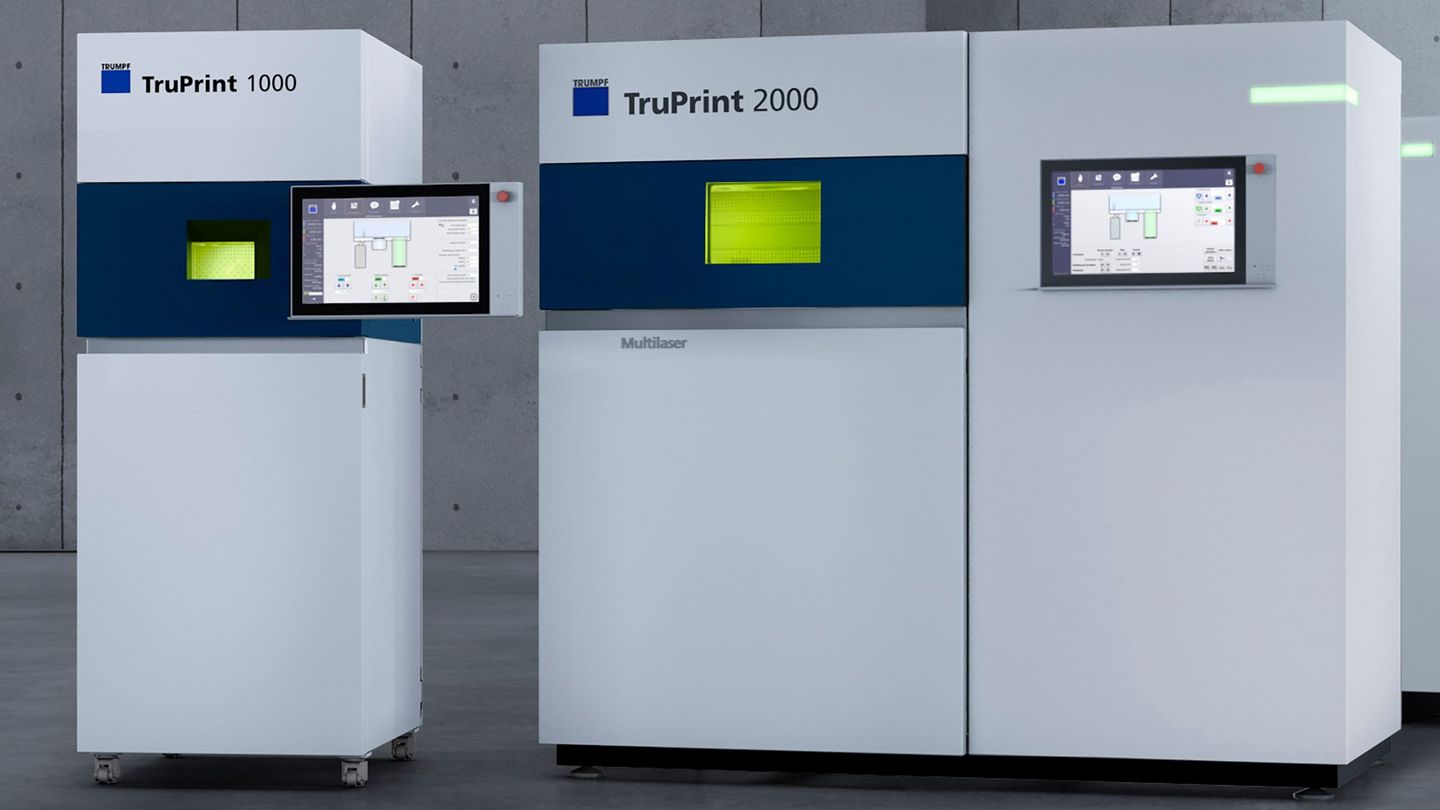
3D printing in premium quality: Highly productive and compact with the TruPrint 1000 or economically with the TruPrint 2000
The advantages of TRUMPF's metal 3D printers
Dental application examples
Book an appointment for our AM Showroom now – in person or online!
Immerse yourself in the additive future of the dental sector with our industry experts, and experience our machines live in action! Or take advantage of an online machine presentation in our Virtual AM Showroom.
A strong network: an overview of our dental partners
From the purchase of your machine to maintenance and servicing – at TRUMPF, you benefit from a broad range of individual services as well as a large network of partners with whom we cooperate closely.
On this page you will find numerous partners who support you with customized solutions in various fields.
If you are interested in a metal printing machine, you are welcome to contact any of our 70 TRUMPF subsidiaries worldwide directly at any time.