All industrial part and powder management components can be combined as part of a modular system. This means you can combine the ideal machine and components to ensure reliable powder and parts handling (including optional shielding gas) in your specific industrial production scenario. We would be glad to help you select the most suitable TruPrint machines and versions of the various industrial part and powder management products.
TruPrint components for powder and parts handling
Optimal handling of the powder and components is crucial for additive series production on an industrial scale. The industrial part and powder management from TRUMPF enables you to increase productivity and profitability in your production operations as setup and powder removal on one or more TruPrint machines can be performed parallel to production.
You benefit from the highest possible degree of flexibility due to the modular construction and the use of standard interfaces. Central components are powder removal/depowdering stations, sieving/powder preparation stations and powder silos.
These components can be operated simultaneously for multiple machines and used to complement TruPrint series machines as well as your entire industrial production line. As a result, you can easily set up powder, build, and parts processes to run in parallel.
Setup and powder removal are performed parallel to production, which increases productivity and profitability.
The closed powder circuit ensures a clean, safe production environment at all times
Benefit from the high degree of automation and high outputs, even when handling large powder volumes.
With the modular construction and the use of standard interfaces, you benefit from utmost flexibility for your production operations.
The inert powder handling meets increased requirements when it comes to quality and the obligation to provide proof.
Powder removal station
Compare product
|
Sieving station
Compare product
|
Powder silo
Compare product
|
Powder preparation station
Compare product
|
|
---|---|---|---|---|
Short overview | ||||
Functional overview |
Unpacking station for reliable, external unpacking of components in a glove box by extracting the powder |
Vibration sieve machine with ultrasonic cleaning incl. vacuum conveyor, scale, and electrical cabinet for filling the supply cylinders |
Standardized storage and transport container |
Powder preparation station for supplying and sieving the powder |
Contents |
Glove box with glove ports |
Sieve machine |
Powder silo incl. pipe bend with air supply |
Sieve machine |
Compatibility |
TruPrint 3000 |
TruPrint 2000 |
TruPrint 3000 |
TruPrint 2000 |
Drive | Electric stroke; manual rotation | - | - | - |
Performance data | ||||
Sieve capacity | - | Up to approx. 100 l/h; approx. 400 kg/h 2 | - | Up to approx. 15 l/h; ~ 50 kg/h 2 |
Sieve insert | - | Sieve surface 2800 cm2; 63 μm mesh size 3 | - | Sieve surface 600 cm2; 63 μm mesh size 3 |
Capacity | to approx. 100 l/h 1 | to approx. 100 l/h 1 | to approx. 100 l/h 1 | - |
Volume of powder containers | - | - | Silo volume: 30/80/130/180 l | - |
Connection and consumption | ||||
Electrical connection (voltage) | 325 - 525 V | 208 - 550 / 230 - 400 V | - | 100 - 230 V |
Electrical connection (current intensity) | 16 A | 16 A | - | 7.5 / 3.5 A |
Electrical connection (line frequency) | 50 Hz / 60 Hz | 50 Hz / 60 Hz | - | 50 Hz / 60 Hz |
Compressed air | 7 bar | 6 bar | 6 bar | - |
Shielding gas | - | Argon, nitrogen (optional) | Argon, nitrogen (optional) | Argon, nitrogen (optional) |
Structural design | ||||
Work area (W x H x D) | 990 mm x 965 mm x 990 mm | - | - | - |
Dimensions (W x H x D) | 1100 mm x 2100 mm x 1000 mm | 2000 mm x 2300 mm x 1000 mm | 670 mm x 1600 mm x 600 mm | 1008 mm x 2090 mm x 755 mm |
Weight | 750 kg | 500 kg | max. 800 kg 4 | 400 kg |
Powder removal station
|
Sieving station
|
Powder silo
|
Powder preparation station
|
|
---|---|---|---|---|
Short overview | ||||
Functional overview |
Unpacking station for reliable, external unpacking of components in a glove box by extracting the powder |
Vibration sieve machine with ultrasonic cleaning incl. vacuum conveyor, scale, and electrical cabinet for filling the supply cylinders |
Standardized storage and transport container |
Powder preparation station for supplying and sieving the powder |
Contents |
Glove box with glove ports |
Sieve machine |
Powder silo incl. pipe bend with air supply |
Sieve machine |
Compatibility |
TruPrint 3000 |
TruPrint 2000 |
TruPrint 3000 |
TruPrint 2000 |
Drive | Electric stroke; manual rotation | - | - | - |
Performance data | ||||
Sieve capacity | - | Up to approx. 100 l/h; approx. 400 kg/h 2 | - | Up to approx. 15 l/h; ~ 50 kg/h 2 |
Sieve insert | - | Sieve surface 2800 cm2; 63 μm mesh size 3 | - | Sieve surface 600 cm2; 63 μm mesh size 3 |
Capacity | to approx. 100 l/h 1 | to approx. 100 l/h 1 | to approx. 100 l/h 1 | - |
Volume of powder containers | - | - | Silo volume: 30/80/130/180 l | - |
Connection and consumption | ||||
Electrical connection (voltage) | 325 - 525 V | 208 - 550 / 230 - 400 V | - | 100 - 230 V |
Electrical connection (current intensity) | 16 A | 16 A | - | 7.5 / 3.5 A |
Electrical connection (line frequency) | 50 Hz / 60 Hz | 50 Hz / 60 Hz | - | 50 Hz / 60 Hz |
Compressed air | 7 bar | 6 bar | 6 bar | - |
Shielding gas | - | Argon, nitrogen (optional) | Argon, nitrogen (optional) | Argon, nitrogen (optional) |
Structural design | ||||
Work area (W x H x D) | 990 mm x 965 mm x 990 mm | - | - | - |
Dimensions (W x H x D) | 1100 mm x 2100 mm x 1000 mm | 2000 mm x 2300 mm x 1000 mm | 670 mm x 1600 mm x 600 mm | 1008 mm x 2090 mm x 755 mm |
Weight | 750 kg | 500 kg | max. 800 kg 4 | 400 kg |
The technical data of all product versions as a download.
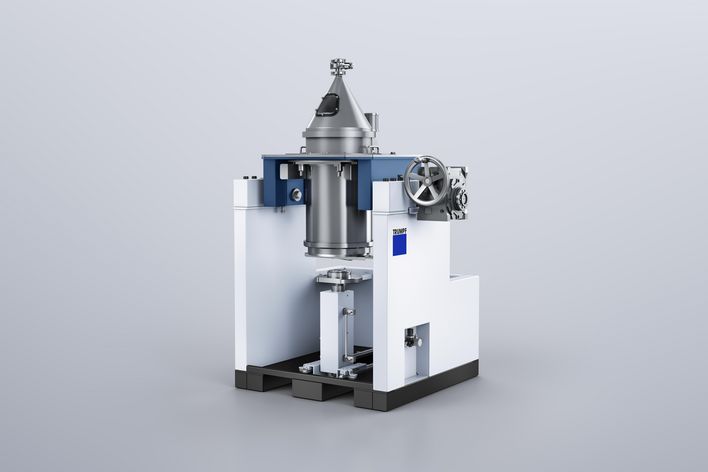
Depowdering station
Our depowdering station with hydraulic lifting and manual swivel and rotary axis allows you to reliably remove powder from components outside the machine. As a result, you benefit not only from high machine availability, but also high cleaning levels of the build job through vibration technology, even for components with complex geometries. Operator involvement is low. We also offer you optional depowdering under shielding gas, including shielding gas flow control and monitoring.
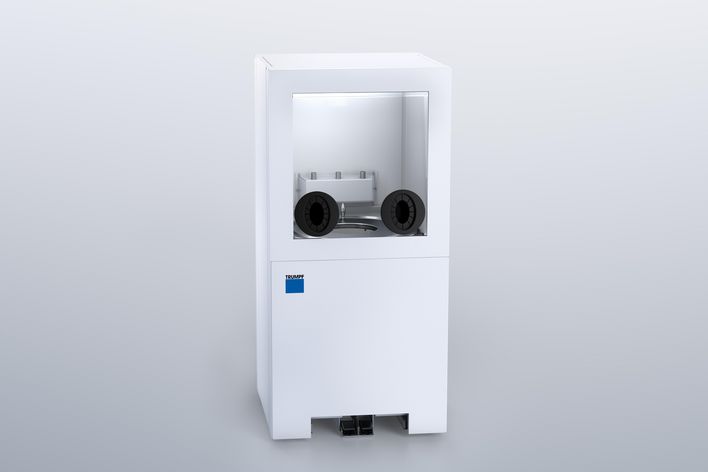
Powder removal station
The powder removal station reliably supplies new metal powder to the 3D printing circuit without any contact with the operator. Components without any contact with the powder can also be separated from the powder bed outside the machine, which improves machine availability. Due to the exchangeable cylinder principle on the TruPrint machines (TruPrint 3000 and TruPrint 5000), the build cylinder can easily be moved into the powder removal station directly after the LMF process. The suction nozzles are optimized to meet requirements and actuated using gloves. They enable even complex components to be cleaned easily. This avoids direct contact with the powder. Optimal access to the station is also provided due to the rotating build cylinder and an electrical lift drive.
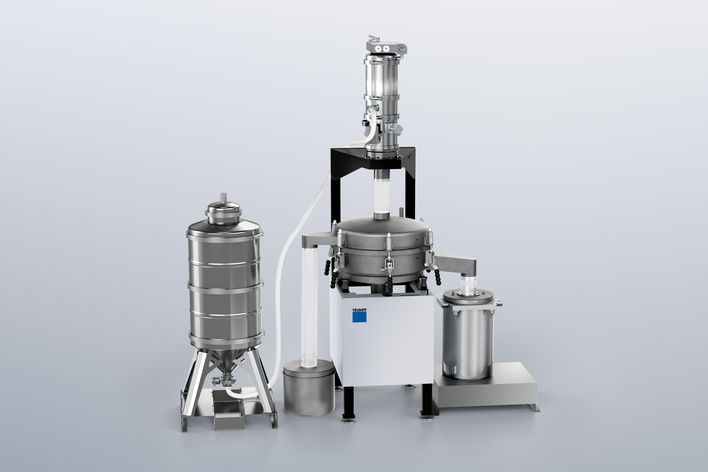
Sieve station with vacuum conveyor
The sieving station provides a highly productive, automatic sieving process with ultrasonic cleaning for industrial metal powder applications. The high degree of automation means the station can be operated unattended. You benefit from a high sieve throughput rate with consistent powder quality due to the large sieve surface and the automated supply of powder on a vacuum conveyor. With the integrated vacuum conveyor, you can also sieve from any container and fill the desired container as required using the weigh-in function. If you need to reliably extract or add large volumes of powder, the vacuum conveyor is the ideal solution for you. It can quickly be attached to the sieving station. What's more, the integrated auxiliary HEPA (high efficiency particulate air) filter ensures a very high level of safety for operators and the environment. For customers with greater requirements when it comes to powder management, sieving with (inert) shielding gas is available as an option – either with argon or nitrogen with 1%, 3% or 5% residual oxygen. Here you are provided with an installation kit including oxygen sensor, as well as the expansion of the user interface for the control and monitoring of the change in the shielding gas over time during the sieving process. Due to the modular periphery, you can also retrofit the option at a later point in time.
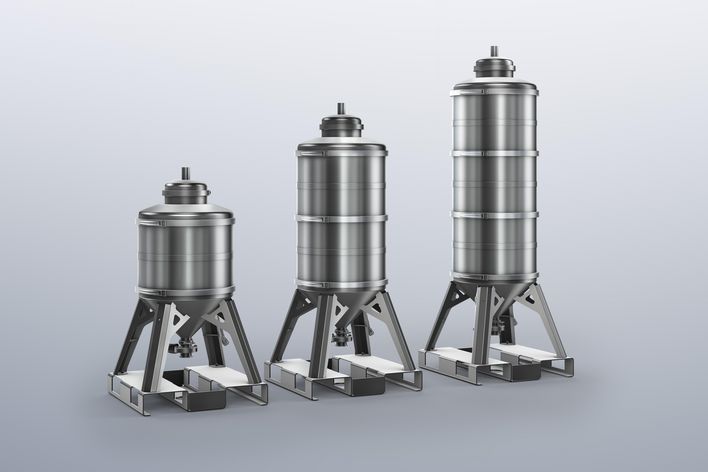
Powder silo
With the powder silo, you can reliably and efficiently store, transport, and fill large powder quantities in a standard container. You can tailor the volume to your needs and select from three sizes (30, 80, and 130 liters). The powder silo can be adapted with utmost flexibility to meet the needs of your specific application. The basic container can easily be expanded by fitting clamps, which can quickly be removed for cleaning purposes. Furthermore, the powder silo is easy to transport using the standard pallet jack. The vacuum conveyor can also be attached to the powder silo in order to easily and reliably extract and add large quantities of powder. Powder storage under shielding gas is also an option. This way, you can regulate and inspect the change in the shielding gas over time during storage. Up to three silos can therefore be monitored in parallel using the testing log. Due to the modular periphery, you can also easily retrofit the option at a later point in time.
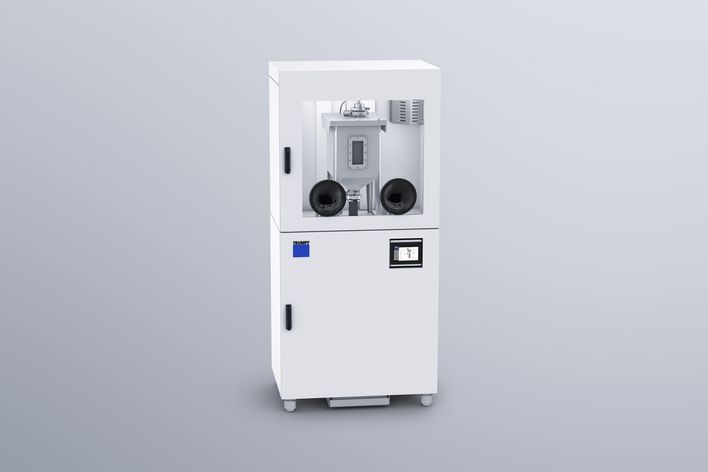
Powder preparation station
The inert machine concept of the TruPrint 2000 with powder preparation station, provides extremely easy powder and parts handling under shielding gas. The closed circuit means that contact with the powder is effectively avoided, and a high level of occupational safety provided. The material also does not degrade due to the minimal contact with oxygen. The powder preparation station can be used for several machines from the TruPrint Series at the same time.
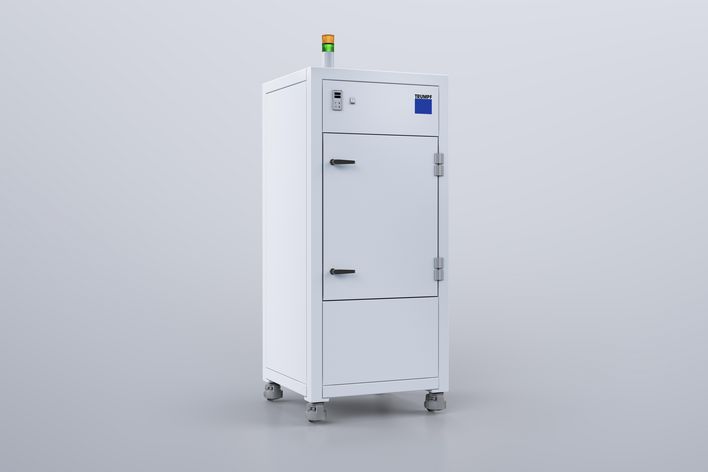
Cooling station
Our separate cooling station for cooling parallel to production after a 500°C build job gives you many advantages: you reduce machine downtime and ensure consistent powder quality through an inert process chain that effectively prevents oxidation of the powder during cooling. The powder can simply be reused. The cooling station is available with the 500°C preheating option.

The right powder for your application
The industrial part and powder management components are based on a closed powder circuit. As a result, you can set up powder, build, and parts handling processes to run in parallel, and can ensure a clean, safe production environment.
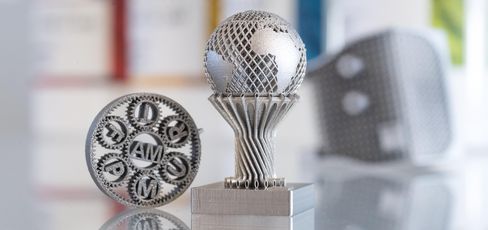
The TRUMPF range includes powders from the areas of stainless steel, tool steel, and titanium, for example. TRUMPF can supply the ideal metal powder and corresponding parameters for your specific application.
This product range and information may vary depending on the country. Subject to changes to technology, equipment, price, and range of accessories. Please get in touch with your local contact person to find out whether the product is available in your country.
Footnotes-
in conjunction with vacuum conveyor
-
depending on the material
-
further mesh sizes on request (80 µm, 100 µm)
-
Permissible filled weight, tare weight 35 kg