Every year, we process over 3,000 application orders in our Laser Applications Center (LAC) in Ditzingen. We have also gathered valuable expertise in the area of fuels cells. A large number of bipolar plates have already been welded by customers in our LAC and their processes have been successfully optimized – while of course adhering to the highest standards of confidentiality. We are pursuing one objective: we want to play an active role in the fuel cell evolution and develop industrially mature, customized manufacturing methods for our customers.
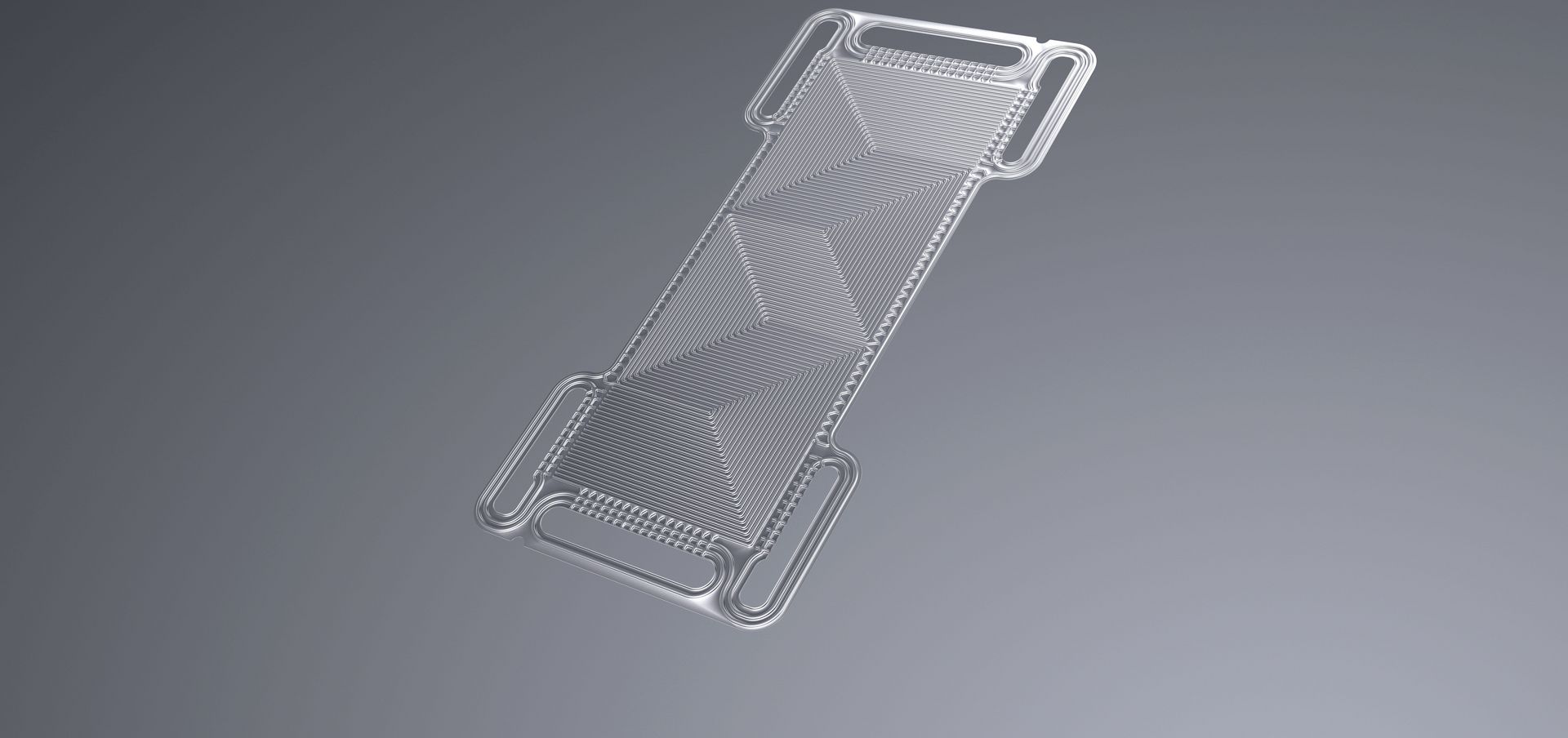
Gas-tight welding of components for the fuel cell
The e-mobility sector faces the great challenge of manufacturing fuel cells safely, economically and reproducibly on an industrial scale. This is exactly where TRUMPF lasers come into their own. The highest requirements for a repeatable welding process apply when joining metallic bipolar plates for PEM fuel cells. Media-tight, highly precise weld seams are achieved which have high mechanical stability at the same time. Thanks to large scan field sizes and highly precise positioning of the bipolar plates, our customers benefit from maximum flexibility and precision.

The programmable TRUMPF focusing optics PFO 3D increase the process reliability and quality during the welding process thanks to intelligent sensor systems.
Welding metallic bipolar plates with TRUMPF lasers
Many challenges – one partner: TRUMPF continually develops and conducts research to provide industrially mature laser solutions for safe and high-quality joining of thin materials.
In order to weld the thin metallic plates (70 to 120 µm) so that they are gas-tight without penetrating them, TRUMPF ensures precise positioning and clamping of these plates thanks to its extensive application know-how and actively supports its customers in their development projects.
Welding bipolar plates involves a great deal of inspection effort in terms of tightness and stability. TRUMPF provides an integrated sensor technology which is constantly developed further in line with demands in order to monitor and ensure the processes and quality and to reduce the subsequent inspection expenditure to a minimum.
TRUMPF singlemode lasers (TruFiber) in combination with PFO scanner optics are predestined for joining the thin half-shells of the bipolar plates at high welding speeds. Typical requirements include laser power of 500-1,000 W IR Single Mode and a laser spot diameter of 30-50 µm on the workpiece with a large scan field available at the same time, so that it is possible to weld as many of the long and numerous welds uniformly in one position with repeatability.
E-mobility consulting - tackling the challenges of e-mobility together
Would you like to know how we can provide your production with optimum support on your path to electromobility? Make an appointment directly with our internationally active branch managers. They are happy to advise you concerning our customized complete packages and facilitate new production technologies for the new mobility.
Why you should choose TRUMPF when thinking about fuel cells
There is simply no alternative to lasers when it comes to joining metallic bipolar plates. TRUMPF provides an extensive product portfolio, corresponding to the application and requirements, as well as comprehensive application expertise.
We work with all leading companies involved in fuel cells. TRUMPF can already draw on comprehensive expertise for welding bipolar plates.
TRUMPF is an application expert and is extremely familiar with the market. We are actively involved in many professional committees focused on fuel cells and are therefore front and center when it comes to the challenges of the industry.
We work with leading companies involved in fuel cells for mobile applications. TRUMPF can already draw on comprehensive expertise for welding bipolar plates.
A PEM fuel cell system consists of many individual subsystems or components, such as MEA, membranes, anode outlet valve, H2 tank, H2 injector, air filter, humidifier unit as well as cooling unit with cooling pump. These also offer a multitude of already established, state-of-the-art and/or potential new application fields for lasers.
TRUMPF the expert
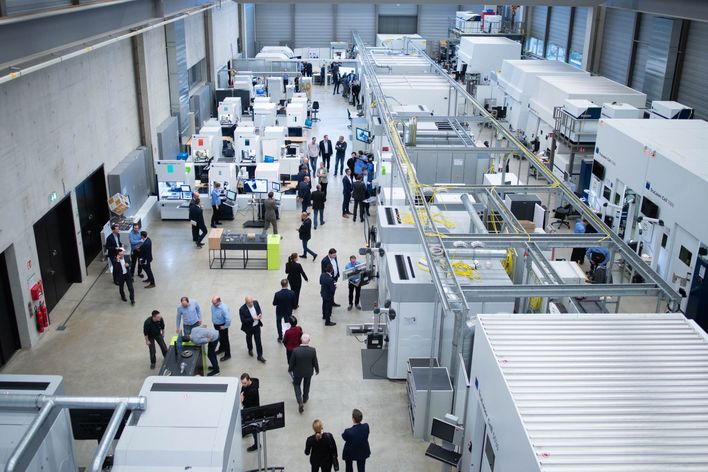