The CHU bracket is designed to be created by milling, with the component produced from a solid block of Al7075 material through subtraction. This conventional manufacturing method means approx. 90 % of the material is removed and places major restrictions on the component design.
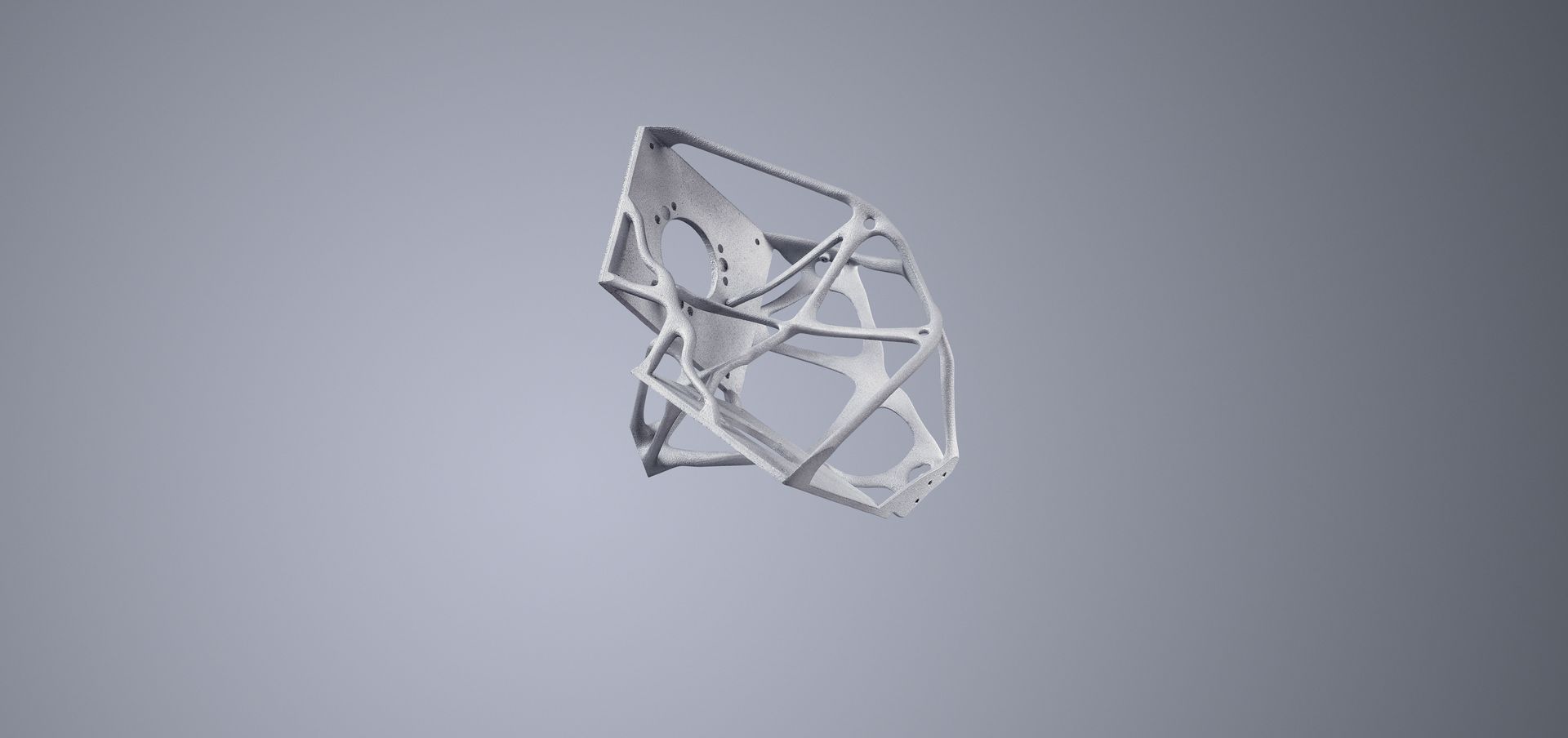
Additive manufacturing for a Camera Head Unit (CHU) bracket
Camera Head Unit bracket I AlSi10Mg I TruPrint 3000
A satellite star tracker consists of a combination of two optical cameras ("star cameras"), aligned to one another at an angle of around 15 degrees. The camera unit (Camera Head Unit = CHU) is protected against thermal and mechanical influences by the CHU bracket, which is normally milled from an aluminum block. Compared to conventional methods, additive manufacturing offers a wealth of advantages, especially design freedom and quality. The star tracker is part of the "Flying Laptop" satellite, which was developed in 2014 by the Institute of Space Systems at the University of Stuttgart and sent into space to reliably calculate the position and alignment of satellites in outer space.
The weight was reduced by around 30% as the component topology was optimized. The more complex component structures can be manufactured using LMF.
Despite its lower weight and the lower strength of the aluminum alloy, the printed component is around 43% more stiff.
If the bracket is manufactured using a TruPrint system, the total volume is reduced by around a quarter.
The design of the LMF bracket has been tailored to the stress it will undergo, resulting in a 48% reduction in peak stresses compared against its conventionally manufactured counterpart.
With our software solution, you can count on consistent top-quality products and documentation.
Compared to mechanical production, the production costs for a bracket produced using additive manufacturing are up to 70% lower. At the same time, the lower weight enables significant cost savings when launching the rocket.
What is the conventional method for manufacturing the Camera Head Unit (CHU) bracket?
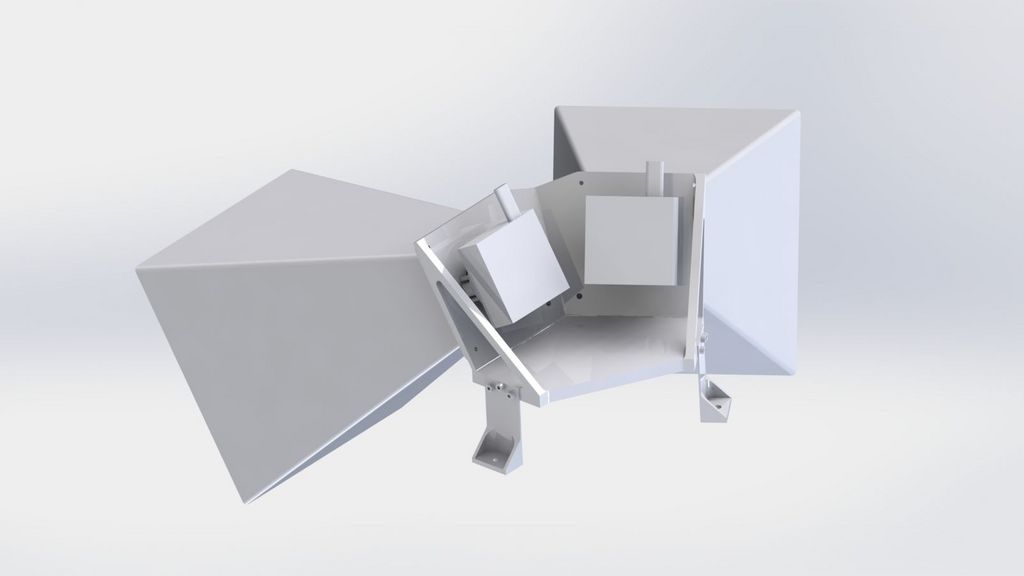
Star tracker manufactured by conventional methods
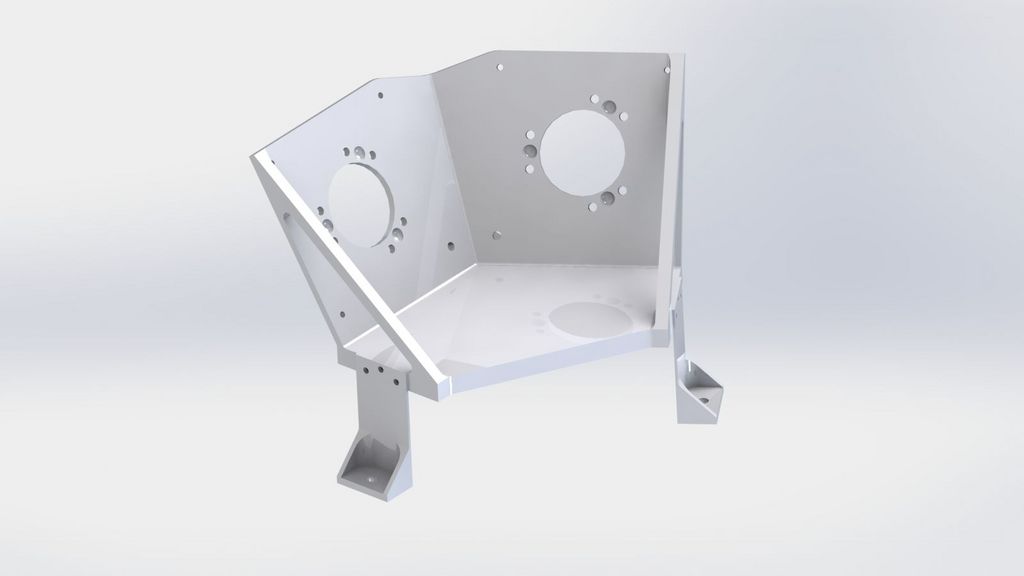
CHU bracket manufactured by conventional methods
How is the CHU bracket created using laser metal fusion?
As a general rule, developments in the aviation and aerospace industry require increasingly affordable, complex and powerful components. Against this backdrop in particular, using additive manufacturing to produce the CHU bracket offers a number of advantages. You benefit from a high degree of freedom when it comes to complex designs. This is particularly useful when deviating from regular geometries such as bionic structures. The design of the CHU bracket was reimagined from the ground up for use with additive manufacturing, and the topology was optimized. Three Camera Head Unit bracket components were printed simultaneously on the substrate plate using a TruPrint 3000 system. The process of manufacturing a component using the TruPrint 3000 lasts approx. 6 hours. If a TruPrint 5000 is used to print the component, the build time is reduced to around 2.5 hours. Further facts and figures on the component can be found at the end of this page. Samples built at the same time for quality assurance purposes were also located on the build plate. Electrochemical polishing and heat treatment for static and modal analyses were no longer required since the change of material meant optimized mechanical material properties for the build.
Arrange your consultation today!
Do you also have a component that would be a good candidate for additive manufacturing? Would you like to know what savings and advantages you can benefit from with additive manufacturing? Then get in touch with us today to arrange an individual consultation with our experts.
Facts & figures about the component
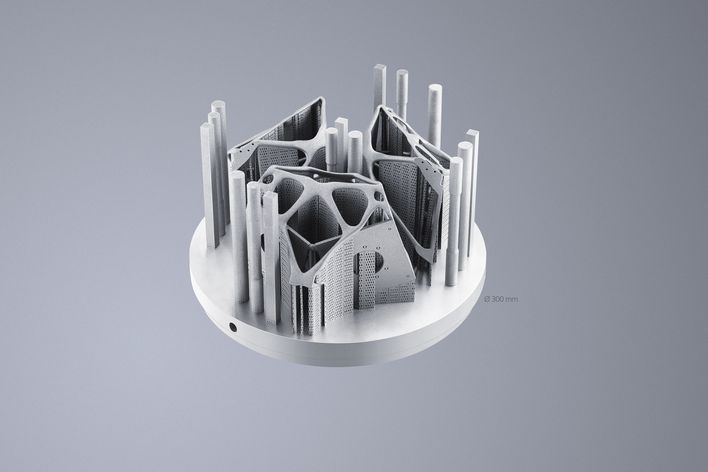
- Component dimensions: 112 mm x 160 mm x 128 mm
- Build time (per component/substrate plate): approx. 6 h (TruPrint 3000), 2.5 h (TruPrint 5000)
- Total build time (all components/substrate plate): 18 h (TruPrint 3000), 7.5 h (TruPrint 5000)
- Layer thickness: 60 µm
- Number of layers: 2,155
- Build rate: 9,626 cm³/hr
- Weight: 332.338 lbs
- Volume: 57,757 cm³
- Customer: The Institute of Space Systems at the University of Stuttgart and the Institute of Structures and Design at the German Aerospace Center