TruLaser Cell 7040 boasts biggest range of beam sources and highest laser power on the market // Automation reduces non-productive time // System enables high-volume production of a wide range of parts
EuroBlech debut: TRUMPF makes the world’s most flexible 3D laser system even faster
Ditzingen, Germany, October 23, 2018 – At this year's EuroBlech, TRUMPF will be launching the latest generation of its TruLaser Cell 7040, one of the most productive and versatile 3D laser systems in the world. As with previous versions, users can opt to equip their machine with either an energy-efficient disk laser or a CO2 beam source. This allows the machine to process a broad range of materials, including steel and light metals, without the need for time-consuming retooling. Operators can choose between cutting and welding operations in 2D or 3D, and TRUMPF has given this new model a major productivity boost by reducing non-productive time, integrating automation features and improving processing quality. Users also benefit from consistently high quality parts and excellent reproducibility as well as reduced energy and material costs. The new machine is particularly suitable for industries that need to produce many different product variants in a short space of time, for instance job shops, the automotive industry and aviation.
Productivity increased, non-productive time significantly reduced
The TruLaser Cell 7040 is an inherently powerful and flexible machine, offering the largest range of beam sources and highest laser power on the market, and capable of executing multiple machining processes. To make the machine even more efficient, TRUMPF has worked on cutting down non-productive time. This encompasses any activity before or after processing that does not add value to the process – retooling or loading and unloading, for instance. "When companies are making batches of products that change on a frequent basis, the cost of this non-productive time really adds up," says TRUMPF product manager Thomas Kirchhoff. The TruLaser 7040 saves time thanks to its smart optic set-up station, a swivel-mounted apparatus mounted on the machine frame that automatically orientates the optics within the work area. This improves accuracy, resulting in consistently reproducible, high quality cutting results.
It also enables the operator to start producing batches much faster than before, since hardly any time needs to be spent on the set-up. As a further improvement, the TRUMPF engineers have also included optimized cutting parameters for both beam sources in the machine control system. Thanks to these integrated laser technology tables, operators need only select the material and thickness and the machine will automatically choose the right cutting parameters for settings such as power and gas pressure. That eliminates the need to hunt for the best parameters manually and enables operators to start the process quicker. What's more, it increases machining quality and decreases scrap rates by locking in the optimal parameters right from the very first part.
In a bid to further boost productivity, TRUMPF experts have also drawn on the latest generation of TRUMPF lasers. The range of compatible products includes highly efficient TruDisk lasers up to 5kW as well as tried-and-tested CO2 TruFlow lasers offering as much as 6kW of laser power. During laser cutting, X-Blast technology ensures increased process reliability by enabling the nozzle to machine the sheet metal at twice the distance. That results in fewer collisions, guaranteeing higher quality, burr-free cutting results even in the case of highly complex components.
Improved cutting and weld quality with the very latest TRUMPF technology
The TRUMPF experts have also set out to significantly boost part quality by integrating BrightLine Weld, a technology developed by TRUMPF for low-spatter laser welding. "With this technology, not only do we get a better quality of weld seam, we can also triple welding speed and achieve a major boost in overall productivity," says Kirchhoff. The developers have also incorporated doors made of glass fiber composites into the new design. These are almost half the weight of their steel equivalent, shaving the time needed to open and close the doors by three seconds. That can help achieve time savings of up to 35 percent per processing cycle.
New ergonomic operating concept
Last but not least, TRUMPF has taken operators' needs very much into account in this new version of the TruLaser Cell 7040. Programming and teach-in are easier because operators can now see inside the machine without having to make unnatural movements. This improvement stems from a moveable, swivel-mounted control panel that operators can quickly adjust to their height and stature. The white paint finish and balanced lighting give operators a clear view of the work area at all times.
Digital photographs in print-ready resolution are available to illustrate this press release. They may only be used for editorial purposes. Use is free of charge when credit is given as "Photo: TRUMPF". Graphic editing – except for dropping out the main motive – is prohibited.
Contactpersoon
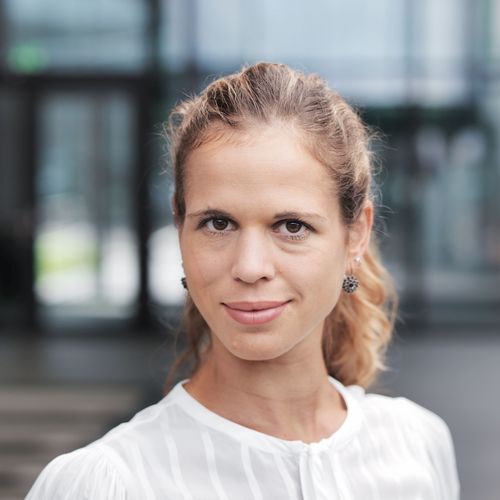