Projekt wspornika CHU został opracowany pod kątem wytwarzania metodą frezowania i wymaga usuwania materiału z bloku Al7075. Dotychczasowa metoda produkcji wiąże się z usunięciem ok. 90% materiału i znacznie ogranicza układ komponentu.
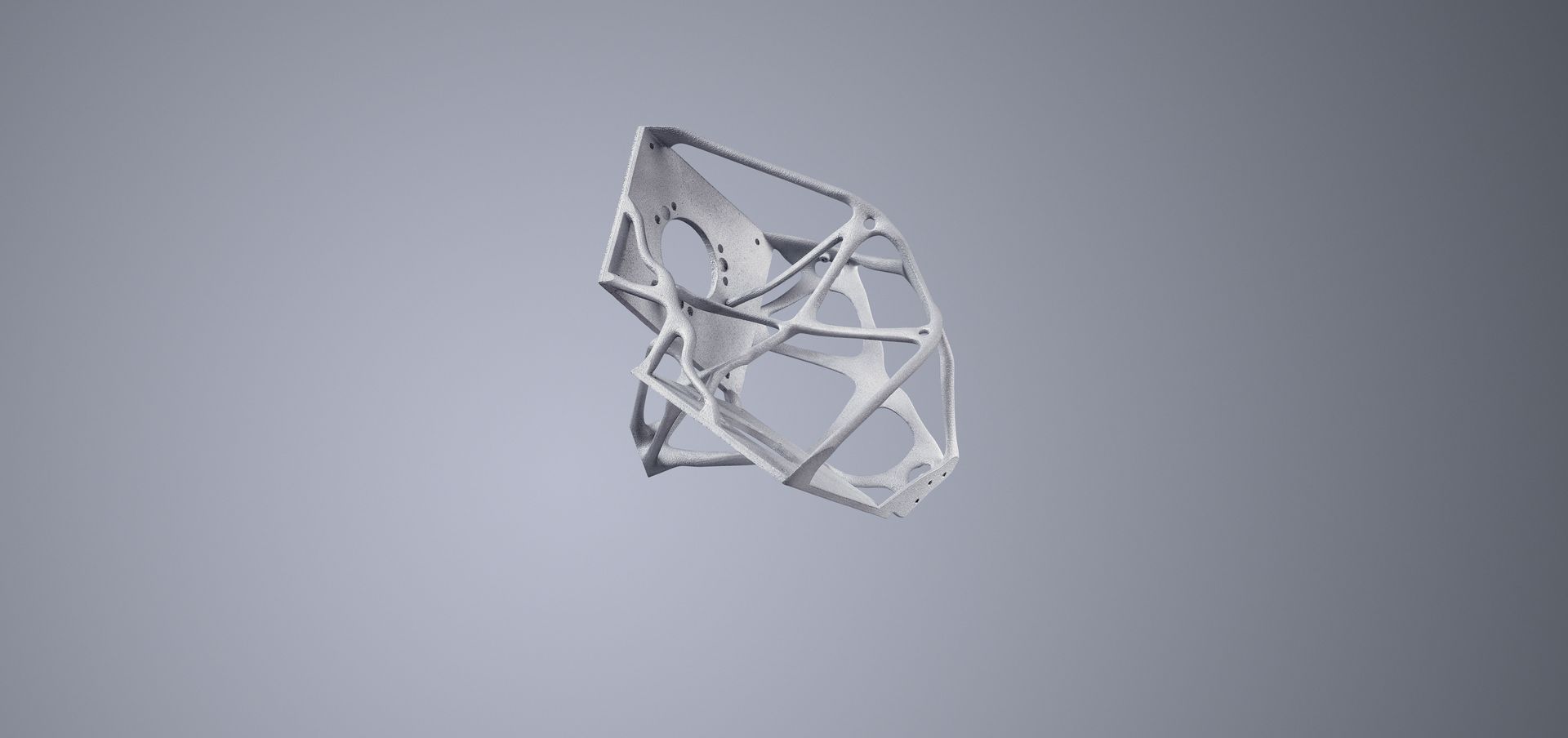
Produkcja addytywna wspornika głowicy kamery (CHU)
Camera Head Unit Bracket I AlSi10Mg I TruPrint 3000
Szukacz gwiazd satelity składa się z połączenia dwóch kamer optycznych („kamer gwiezdnych”), które są ustawione w stosunku do siebie pod kątem wynoszącym ok. 15 stopni. Jednostka kamery (ang. Camera Head Unit = CHU) jest chroniona przed wpływami oddziaływania cieplnego i mechanicznego przez tzw. wspornik głowicy kamery, który tradycyjnie wykonywany jest metodą frezowania bloku aluminium. W porównaniu z tą metodą produkcja addytywna zapewnia wiele zalet, szczególnie dotyczy to swobody kształtowania i właściwości. Szukacz gwiazd jest elementem satelity Flying Laptop, opracowanej w 2014 r. przez Instytut Kosmiczny Uniwersytetu w Stuttgarcie, zadaniem tego elementu, aby niezawodnie obliczać położenie i orientację satelitów w przestrzeni kosmicznej
Masa obniżyła się o ok. 30%, ponieważ element został topologicznie zoptymalizowany. Skomplikowane struktury elementów można wytwarzać metodą laserowego łączenia metali.
Pomimo mniejszej masy i stopu aluminium o słabszych właściwościach element wydrukowany odznacza się sztywnością większą o ok. 43 %.
Produkcja wspornika z wykorzystaniem systemu TruPrint oznacza obniżenie całkowitej objętości o jedną czwartą.
Ze względu na konstrukcję dostosowaną do obciążeń element wykonany metodą laserowego łączenia metali odznacza się o 48% mniejszymi maksymalnymi naprężeniami niż konwencjonalna część.
Nasze rozwiązania oprogramowania pozwalają użytkownikom polegać na stale wysokiej jakości produktu i dokumentacji.
W porównaniu z obróbką mechaniczną koszty produkcji wspornika wykonanego metodami przyrostowymi spadają nawet o 70%. Jednocześnie zmniejszona masa pozwala na obniżenie znacznych kosztów startu rakiety.
Jak wygląda konwencjonalna produkcja wspornika głowicy kamery (CHU)?
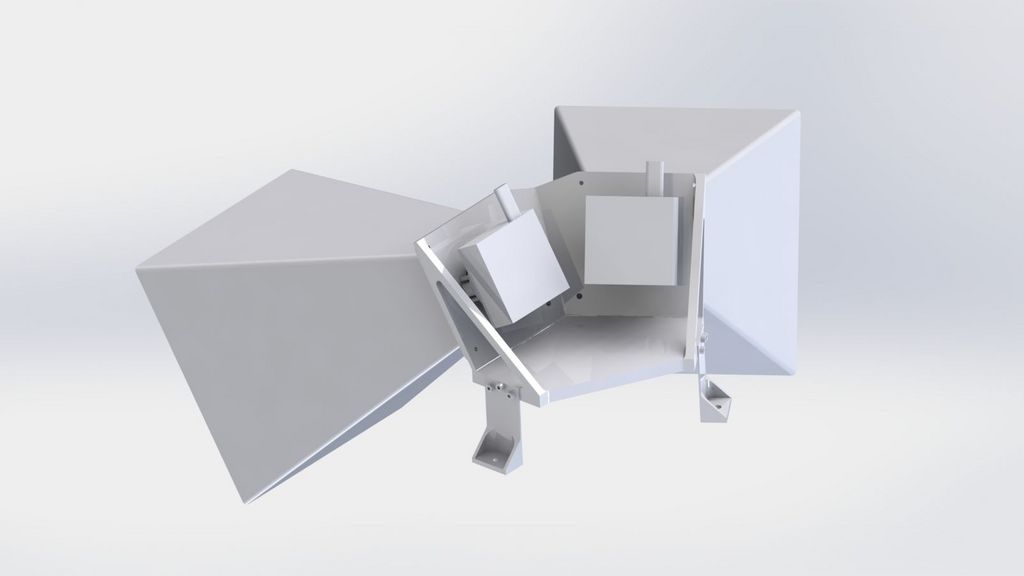
Szukacz gwiazd wykonany konwencjonalnie
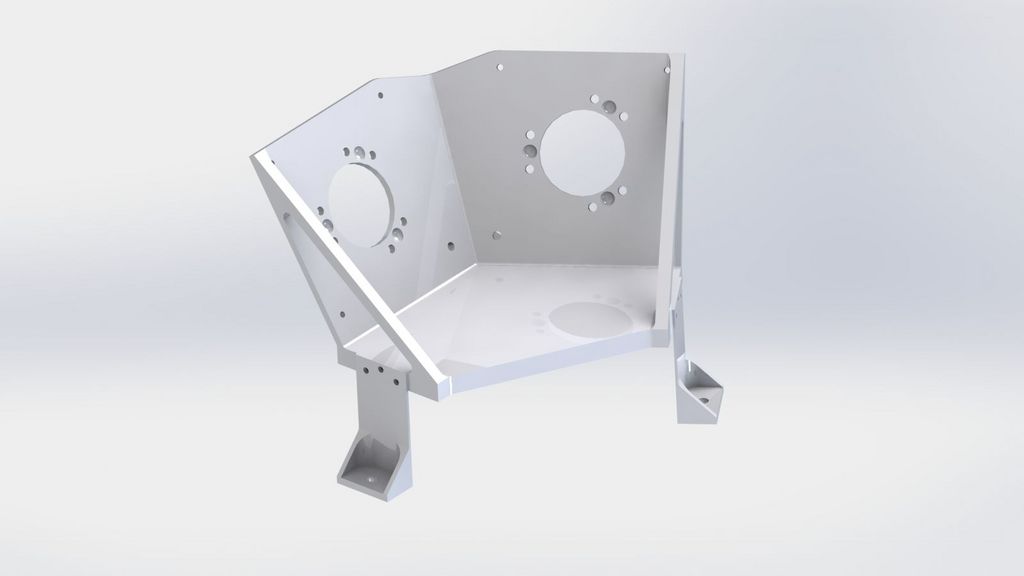
Wspornik CHU wykonany konwencjonalnie
Jak powstaje wspornik CHU wykonany metodą laserowego łączenia metali?
Firmy z branży lotniczo-kosmicznej wymagają coraz większego obniżania kosztów, zwiększania złożoności i polepszania parametrów komponentów. Produkcja addytywna wspornika głowicy kamery odznacza się wieloma zaletami w tych obszarach. Pozwala to na uzyskanie dużej swobody kształtowania przy złożoności elementu. Jest to szczególnie istotne w przypadku odejścia od standardowej geometrii takich jak struktur bionicznych. Projekt wspornika CHU został wykonany na nowo pod kątem produkcji addytywnej, a następnie zoptymalizowany topologicznie. Na płycie substratu urządzenia TruPrint 3000 drukowane są jednocześnie trzy elementy wspornika głowicy kamery. Produkcja elementów na urządzeniu TruPrint 3000 trwa ok. 6 h. Jeśli używana jest maszyna TruPrint 5000, czas generacji zmniejsza się do ok. 2,5 h. Więcej danych i faktów dotyczących elementu znajduje się na końcu niniejszej strony. Na płycie roboczej znajdują się ponadto próbki wykorzystywane podczas kontroli jakości. Polerowanie elektrochemiczne i obróbka cieplna nie były konieczne, ze względu na przeprowadzenie analizy modalnej i statycznej – podczas zmiany materiału przeprowadzono optymalizację z uwzględnieniem właściwości mechanicznych.
Warto zapewnić sobie doradztwo!
Czy w Państwa ofercie też znajdują się elementy, które chcieliby Państwo produkować metodami addytywnymi? A może chcieliby Państwo dowiedzieć się, jaki jest potencjał oszczędności i co można zrealizować dzięki produkcji addytywnej? Zapraszamy do kontaktu z nami i do ustalenia indywidualnego terminu konsultacji z naszymi ekspertami.
Dane i fakty dotyczące elementu
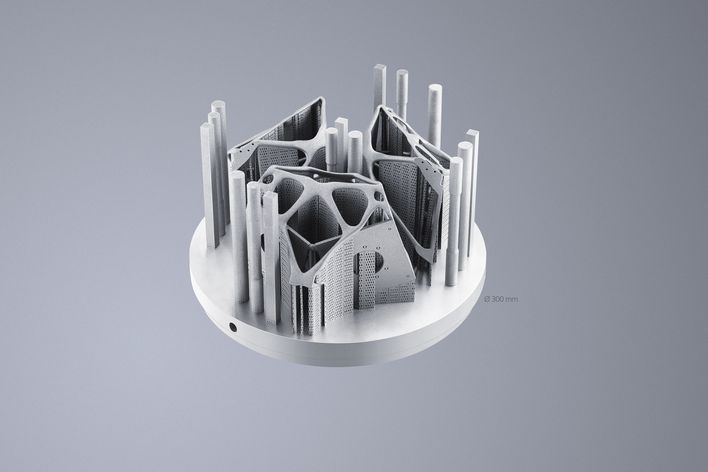
- Wymiary elementu: 112 mm × 160 mm × 128 mm
- Czas produkcji (na element / płytę substratu): ok. 6 h (TruPrint 3000) / 2,5 h (TruPrint 5000)
- Całkowity czas produkcji (wszystkie elementy / płyty substratu): ok. 18 h (TruPrint 3000) / 7,5 h (TruPrint 5000)
- Grubość warstwy: 60 µm
- Liczba warstw: 2155
- Szybkość tworzenia: 9,626 cm³/h
- Masa: 150,746 g
- Objętość: 57,757 cm³
- Klient: Instytut Kosmiczny Uniwersytetu w Stuttgarcie oraz Instytut Konstrukcji i Technologii Strukturalnej Niemieckiej Agencji Kosmicznej