INTECH in-house trade show: TRUMPF presents efficient laser technologies for mass production of electric vehicles // TRUMPF's digital transformation making good progress // Chief Digital Officer Kammüller sees promising opportunities for German machine builders
TRUMPF focusing on electromobility and Industry 4.0
Ditzingen; April 10, 2018 – German high-tech company TRUMPF sees major opportunities for its business and for German industry as a whole in the two megatrends of Industry 4.0 and e-mobility. “The mechanical and systems engineering industry in Germany can reap big benefits from connectivity in industry and e-mobility,” said Mathias Kammüller, Chief Digital Officer at TRUMPF, at the company's in-house trade show INTECH. “Two key areas are connected manufacturing, as the next stage of technology on the shop floor, and future mobility. These two factors will help safeguard jobs in development, manufacturing and application engineering – and even create new ones,” he said. Kammüller also noted that digitally connected lasers will play an essential role in the transition from vehicles powered by internal combustion engines to all-electric vehicles. He also noted that lasers were the key to making the production of electric vehicles cost-competitive in the first place.
Growing demand for manufacturing methods for electric vehicles
TRUMPF has witnessed a surge in demand for manufacturing technologies in the realm of e-mobility. Battery manufacturing already makes up 10 percent of TRUMPF's turnover in the automotive sector, a figure that is continuing to climb. The company has already sold more than 500 lasers worldwide for use in battery manufacturing. “We have the right manufacturing methods to enable the commercially viable production of key components of future mobility solutions: lasers really are the only technology that can offer such a flexible, highly productive way of mass-producing batteries, high-power electronic systems and electric drives,” said Christian Schmitz, Chief Executive Officer Laser Technology at TRUMPF. Finding an affordable means of producing electric vehicles by the millions requires robust manufacturing methods that can be scaled up quickly from today's relatively low volumes to full-scale mass production.
Laser technology for efficient mass production of electric motors
At the INTECH trade show, TRUMPF demonstrated a series of laser techniques that can weld all the seams on an electric motor in just one minute. “Our welding process for what we call the ‘hairpins’ is just one of the techniques we use to make the production of electric motors faster, more reliable and more economical. It eliminates the costly and time-consuming process of winding thick copper wire arounds the coils of powerful electric motors. And that makes it much easier to produce them in bulk,” said Schmitz. The hairpin method involves using a compressed-air pistol to fire a rectangular copper wire, similar to a hairpin, into a slot on the side of the motor. The protruding parts of the wire are then twisted together and welded using a laser.
Digitalization for reliable battery manufacturing
TRUMPF technology also plays a key role in manufacturing batteries for electric vehicles. The batteries consist of multiple layers of wafer-thin copper and aluminum foils that are cut to size using lasers. After adding liquid electrolyte, the battery is welded shut with a cap. It is essential that the welds seal the cell completely, because battery failure during operation could pose a risk of fire and injury. From the battery cells and battery modules to the battery pack, all the welding is carried out using a laser. The laser systems feature sensor systems as well as a software program that connects them to a cloud solution. The sensors provide data for quality assurance and documentation purposes, but they also help control the welding process itself. “One problem for battery manufacturers is that they can't test whether a battery actually works until the very end of the manufacturing process. They need the process to be monitored continuously to ensure that the battery comes out the other end working properly,” said Schmitz.
TRUMPF expands its own digitalization capabilities
“Our lasers for the automotive sector are a good example of how important digital transformation is to TRUMPF. To ensure our own production processes remain fit for the future, we are constantly expanding our in-house digitalization efforts,” said Mathias Kammüller. TRUMPF already has over 500 employees working on more than 30 digital transformation projects. “That’s helping us to improve efficiency, cut costs, and boost our competitiveness. Digitalization is a crucially important factor, particularly for our locations in Germany with their high labor costs,” Kammüller noted. During this fiscal year, the company has opened a smart factory in Chicago as well as a connected logistics center in Ditzingen near Stuttgart, Germany.
Digitally connected solutions for the entire production process
This year's edition of INTECH played host to some 2,200 visitors from all over the world. The show gave them the opportunity to find out more about TRUMPF's full range of products, including the company's TruConnect solutions, which not only monitor laser systems, but also offer a means of boosting the productivity of sheet metal processing. “We are basically digitalizing the entire production process: from initial customer queries to issuing invoices, and from ordering raw materials to dispatching finished products. The activities carried out before and after manufacturing itself make up almost 80 percent of the process. Our solutions can help make drastic reductions to time and money spent,” said Heinz-Jürgen Prokop, Chief Executive Officer Machine Tools.
Cutting-edge solutions for sheet metal and tube processing
The INTECH fair showcased the TruLaser Weld 5000, a new robotic welding cell that can process parts up to four meters long. The company also unveiled two new laser tube cutting machines: the TruLaser 5000 and the TruLaser Tube 7000 fiber, the latter of which can handle tubes with diameters up to 254 millimeters. Cutting speeds are high, thanks to its solid-state laser and RapidCut feature.
The show also marked the world premiere of the new TruLaser Cell 5030. This machine expands TRUMPF's portfolio of 2D and 3D laser cutting systems. The TruLaser Cell 5030 features a new disk laser that offers outstandingly high cutting speeds, particularly when machining thinner sheets.
Digital photographs in print-ready resolution are available to illustrate this press release. They may only be used for editorial purposes. Use is free of charge when credit is given as “Photo: TRUMPF”. Graphic editing – except for dropping out the main motive – is prohibited.
担当者
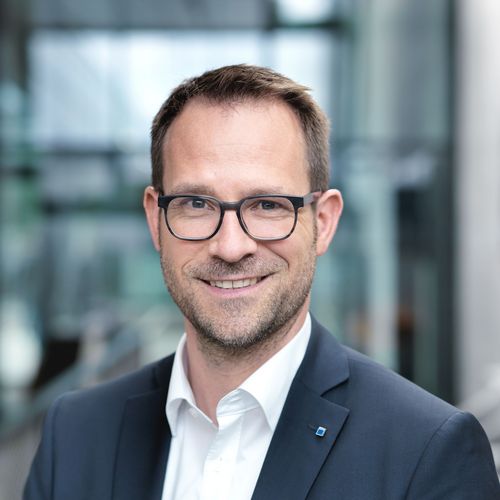