When welding copper with a green wavelength, users benefit from a high absorption of laser light and high process efficiency. The green laser fully demonstrates its benefits in the field of heat conduction welding. Thanks to its special keyhole shape, even deep penetration welding only creates very few spatters. Regardless of the material surface - polished, brushed, oxidized or etched - copper welds can always be reliably produced with consistent quality with green laser radiation.
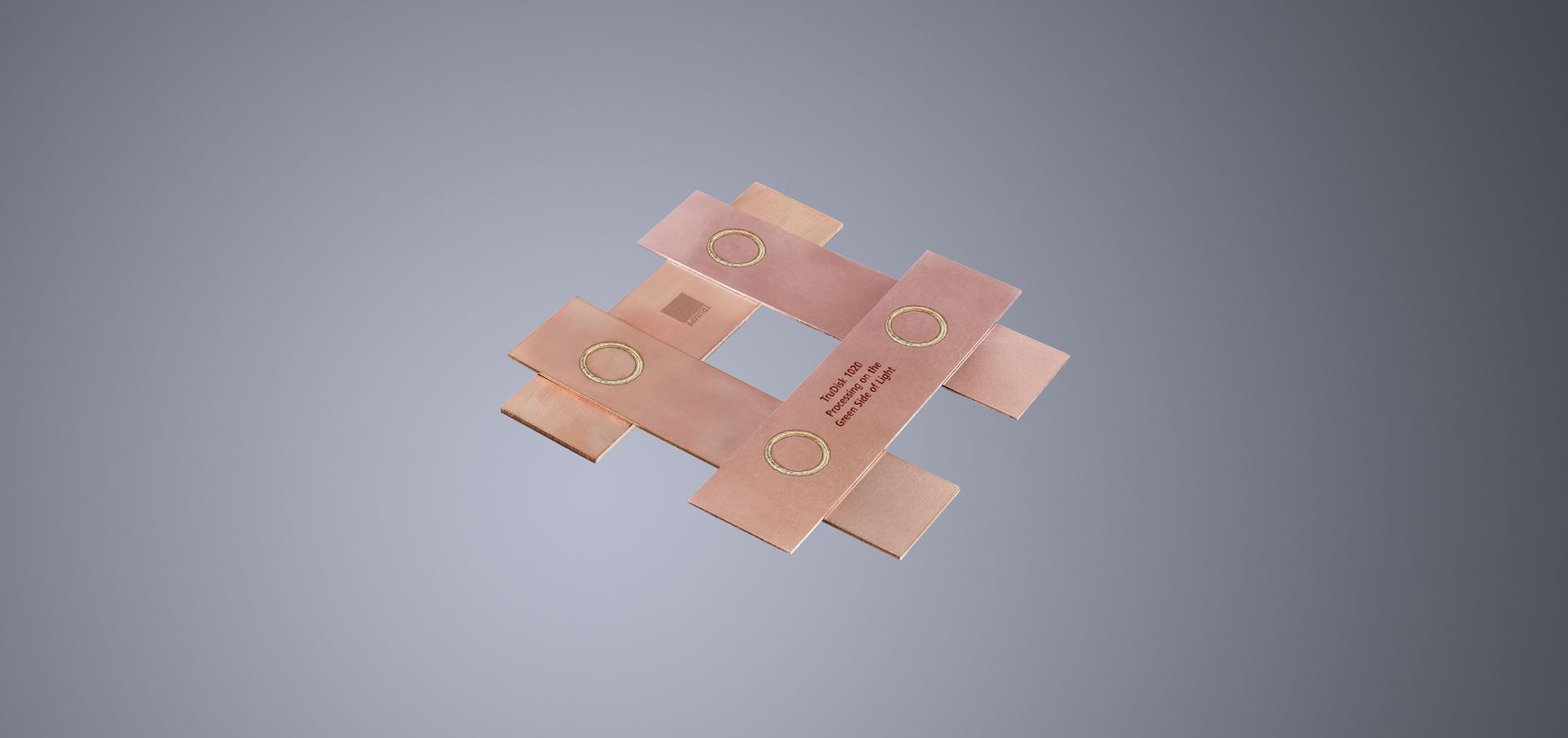
Welding copper - one application, a few challenges
Components made of copper play a key role in many sectors: whether it's e-mobility, electronics or in the jewelry and watchmaking industry. There are two main challenges when welding the highly reflective material: weld seams with consistently high weld quality and minimal spatter. This is where the laser comes into its own. High-strength connections which are also entirely reproducible and have high conductivity can be achieved with non-contact tools. And in comparison with TIG welding, no additional material is required which would make the component heavier.
Copper welding - stable and practically spatter-free
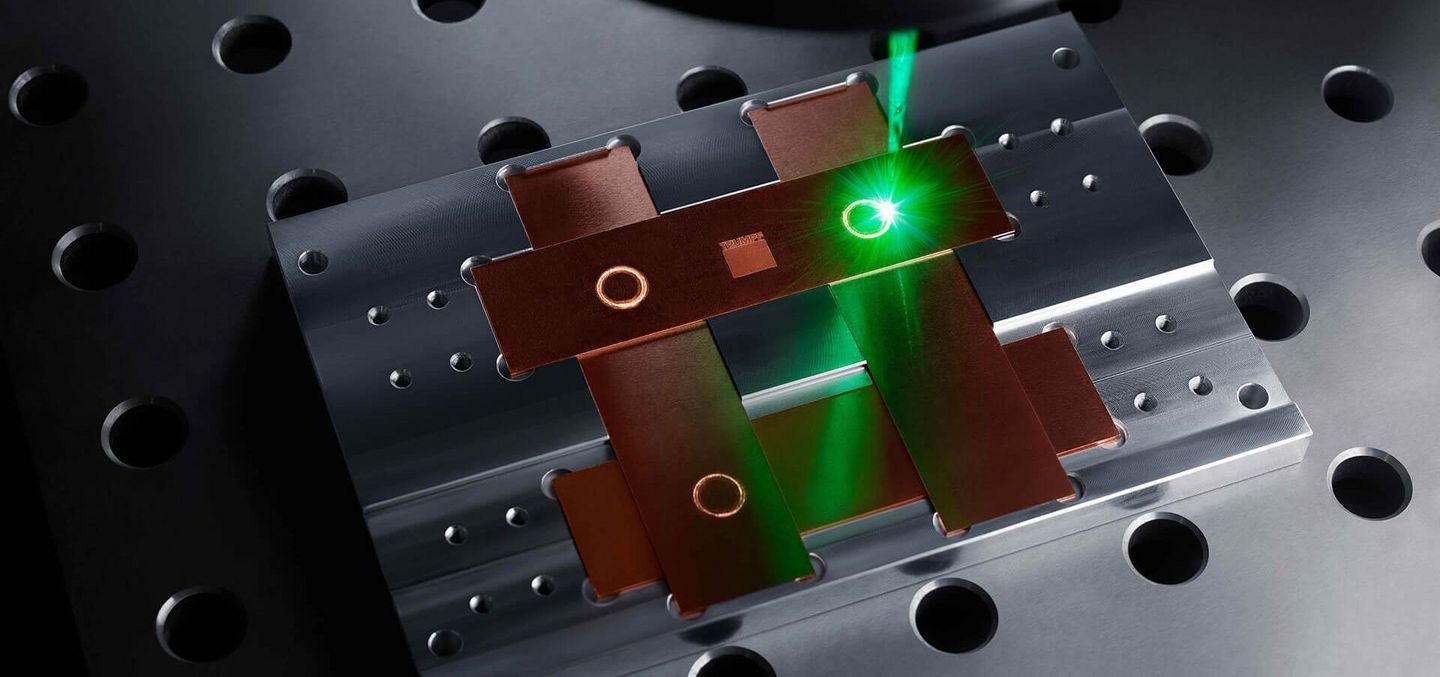
What different methods can be used to weld copper?
TIG welding, soldering, screwing - what are the advantages of copper welding with a laser in comparison with alternative methods?
Compared to TIG welding, screwing or soldering, this laser can produce consistent weld seams without additional material.
Copper welding with a laser inhibits the formation of pores thanks to optimized weld pool dynamics. Spatter is effectively reduced.
Regardless of the material surface composition, the green laser produces weld seams of a consistently high quality.
Welding copper and aluminum connections is possible with minimal mixing of materials (intermetallic phase), resulting in a high degree of stability and conductivity.
A laser is a non-contact tool with no wear. Components are not contaminated or damaged.