Deposition welding is a generating process that is applied for surface finishing as well as repairing or modifying existing components. Depending on the task at hand, either manual or automated laser deposition welding is used.
Deposition welding
Building shapes out of powder and wire
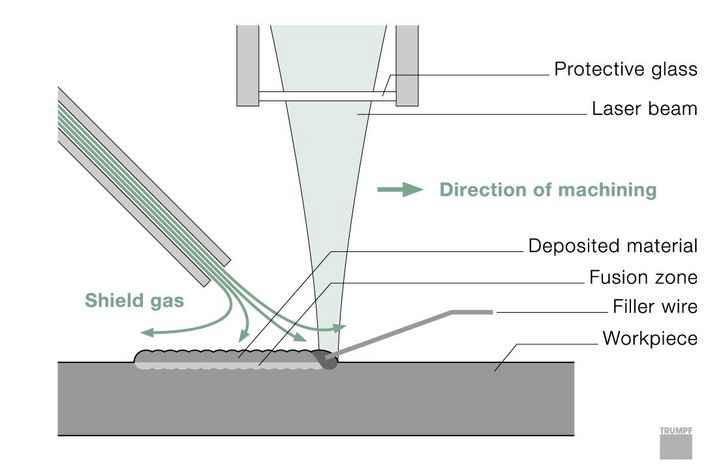
Manual laser deposition welding
In the case of manual deposition welding, the welder guides the filler material "by hand" to the area to be welded. A thin wire with a diameter between 0.15 and 0.6 millimeters is primarily used as filler material in this process. The laser beam melts the wire. The molten material forms a strong bond with the substrate, which is also melted, and then solidifies, leaving behind a small raised area. The welder continues in this fashion, spot by spot, line by line, and layer by layer, until the desired shape is achieved. Argon shields the work process from the ambient air. Finally, the part is restored to its original shape by grinding, lathing, milling, EDM etc.
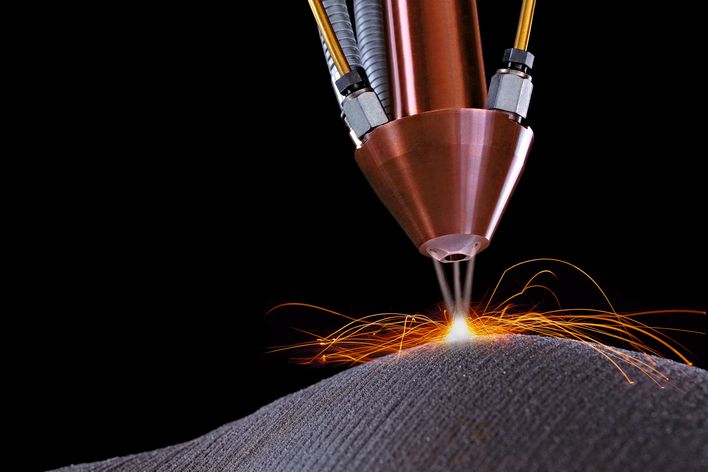
Automated laser deposition welding
In the case of automated deposition welding, the machine guides the filler material to the area to be welded. Although the material can also be a wire, this process primarily uses metal powders. Metal powder is applied in layers to a base material and fused to the base material and is fused to it without pores or cracks. The metal powder forms a high-tensile weld joint with the surface. After cooling, a metal layer develops that can be machined mechanically. A strength of this process is that it can be used to build up a number of similar or differing metal layers.