From the point of view of a machine, human beings are really quite remarkable things. They have no problem sketching a line on a piece of paper, working completely freehand. Humans can also hold an egg in their hand without crushing it, and then peel it for good measure.
And they seem to have no trouble at all in sharpening a stick and using it to roast marshmallows over a fire without burning them! We humans can tackle these tasks because we have sensors that monitor and adjust our movements based on real-time feedback – in other words, our senses. So wouldn’t it be great if machines had senses, too?
Machines with senses
Then we would finally be free from the hassle of having to program every coordinate path, teach every sequence of operations, and painstakingly slice open and inspect weld seams. We could simply trust our machines to do a great job. Wouldn’t that be something ? Well, in fact, it’s already happening!
Machines are already acquiring these kinds of senses in their own particular way. When laser marking first emerged, machine operators had to use an ultra-precise clamping fixture to get the markings in exactly the right place. After all, how could a marking laser be expected to find the right spot?
All it could do was aim blindly at the point where two coordinates met and hit whatever happened to be there. But today’s marking lasers are different: They have a camera eye that allows them to detect what’s in front of them and align the optics to mark exactly the right spot. This development is already transforming the world of manufacturing – and there’s plenty more to come.
Lasers feel better
There are essentially two types of sensors. Monitoring sensors supply data for quality assurance and documentation purposes, but do not actually intervene in a running process. One popular example is a sensor designed to monitor compliance with specified limit values. If the defined thresholds are exceeded, the machine sounds an alarm and the production manager can immediately check where the problem lies.
Control sensors, on the other hand, measure a value and then intervene in the running process. Depending on the reading, a control sensor might modify the laser power, or adjust the feed rate or focal position. Generally speaking, control sensors are more complex than monitoring sensors.
Laser material-processing machines are particularly easy to equip with sensor technology. The optics are the perfect place to put a sensor, offering a simple connection to the mounting system and allowing the sensor to peer directly into the process. The incorporeal nature of a laser beam means it can only be controlled digitally, so it is very easy to incorporate it in a control loop that includes sensors.
01 — PATTERN RECOGNITION
The camera can easily detect even the smallest hairpins on electronic components, identifying the specific points that need to be welded, and forwards this information to the focusing optics. In the case of laser marking, the image processing system verifies that the marking is in the proper position and checks that the text or code is correct and legible.
02 — TEMPERATURE
A pyrometer measures temperature changes during the active process. During the laser transmission welding of plastics, this can be carriedout at the seam welding point: as soon as the specified target temperature is reached, the system adjusts the laser power to ensure the temperature remains stable.
03 — MELT TRAVEL
An inductive melt-travel sensor records the time and displacement of a part while the process is running. In laser transmission welding, the sensor measures the lowering of the upper plastic part. The laser stops once the specified amount of travel has been achieved. This method also makes it possible to compensate for component tolerances.
04 — WELD DEPTH
A low coherence interferometer measures distances with a degree of accuracy better than a tenth of a micrometer. In laser welding, it can be used to monitor the depth of penetration. That enables the quality control team to ensure that the weld depth is exactly right — in other words not too deep, and not too shallow.
05 — WELD JOINT
With the aid of line lasers projected onto the weld joint, a high-speed camera detects the seam position during the welding process and adjusts the scanner before the process starts. The seam-position control system is an ultra-fast, non-contact solution that operates in real time. Examples of its use include fillet welds in automotive-body manufacturing, butt joints in gearbox welding, and continuous pipe welding. It makes the welding process faster while producing significantly less scrap.
Make more money with sensors
Until just a few years ago, process sensors were the exception rather than the rule. But now they are regarded as an integral part of production in segments such as automotive and medical technology. And it’s not hard to see why: sensors help companies make more money by introducing faster cycle times, better quality, seamless quality control, less scrap, and consistent traceability in the field.
In the realm of automotive-bodywork welding, sensor-based remote welding operates at over twice the speed of welding with filler wire. Cameras detect the position of the part during welding or marking. As a result, the part holder can be made to less demanding specifications, making it cheaper and easier to build.
In welding processes, monitoring sensors provide reliable, seamless quality documentation along the entire length of the seam for each individual part. That gives a greater level of reliability than conducting destructive sample testing in the field, and it means this latter method can often be significantly scaled back or eveneliminated altogether.
Monitoring sensors also deliver instant reports on any faulty welds, in turn allowing production staff to tackle the problem the moment the first part is affected rather than discovering at the end of the shift that hundreds of parts need to be scrapped. Meanwhile, control sensors endeavor to push scrap rates close to zero by making immediate adjustments whenever something goes wrong
The multi-eye trend
Steadily increasing demand for smaller and more precise components is also driving a trend toward greater use of sensor technology. The more complex the part, the more stringent the quality standards for tasks such as welding, and the greater the need for sensors capable of monitoring and controlling the process with a high level of precision. Of course this argument also holds true in reverse, with the power of sensors paving the way for new kinds of part geometries. In the case of remote welding of car-body parts, for example, the decision to shrink flanges became available only once the operator was confident that the seam-position control system would reliably locate the correct position for each and every fillet weld. This newfound confidence has been helping automakers reduce weight, use less material and speed up their production lines ever since.
A new level of tolerance
Slowly but surely, these efforts to bring about machine perception are transforming the appearance and functionality of entire manufacturing systems. Previously, machines worked blind. Engineers had to guide them millimeter by millimeter, painstakingly anticipating every change in speed, component position, or contour. As expectations of component and machining precision have become more demanding, so too has the effort involved in mounting and positioning each part, some-times reaching absurd heights.
And machine frames have become heavier, bulkier and more complex as operators strive to meet the required tolerances in the micrometer range.
Yet the moment a machine establishes contact with its environment, it becomes capable of formulating its own response to each part. Frames can be made narrower and smaller and reduced to the bare essentials, and positioning devices can be made more flexible. Ultimately a new level of tolerance emerges throughout the process, though the results are just as accurate as ever. Laser welding is the perfect example: place a part just about anywhere in the cabin, and the laser will get the job done.
Delving into the Big Data mine
Factory managers have long recognized the importance of data as an integral part of Industry 4.0 – and more is always welcome. This data stems from various sources, with one of the most reliable being the sensors that monitor production processes. At the same time, however, small and medium-sized enterprises are facing something of a dilemma as to what they should actually do with all the data they collect. In response, a pioneering wave of suppliers is already busy developing intelligent services designed to analyze process data. The ultimate goal is to use big-data methods to spot imminent problems in a manufacturing process or to develop an algorithm that – when fed with enough data – can autonomously suggest how to improve a process and even execute the necessary actions itself.
Condition monitoring for individual machines is already well established; the next step is status monitoring for an entire factory, followed by sensor-based production control.
In the meantime, experts are busy working on new sensors and sensor combinations. They are currently pinning their hopes on interferometric sensors, a highly promising development that is currently very much in vogue. This type of sensor uses the interference of light waves to measure a broad range of parameters ranging from weld depth to seam detection. Although interferometers are still an expensive substitute for cameras when it comes to position sensing, their prices are steadily falling, and it won’t be long before the devices become smaller and cheaper.
No one doubts the benefits they offer. Perhaps at the top of the list is their ability to produce three-dimensional images. This is particularly useful when measuring volumes, especially in applications such as laser ablation and laser metal deposition.
The dream of doing nothing
The promise of autonomous manufacturing is drawing ever nearer. Small companies, in particular, have long been clamoring for simplified production processes where machine operators can simply place any machinable part anywhere they like in a machine. Using its data-base of CAD drawings, the machine would then identify the part, decide how it should be machined, and execute the necessary welding operations. In principle, there would be nothing else the operator would have to do.
Of course there is still some way to go before this becomes reality – the evolution of autonomous driving would perhaps be an apt comparison – but we are clearly heading in the right direction. One example of a sensor capability that really does seem to be just around the corner is material recognition, a technology that will make processes such as laser marking even simpler. The future certainly looks bright!
The dream of doing nothing
The promise of autonomous manufacturing is drawing ever nearer. Small companies, in particular, have long been clamoring for simplified production processes where machine operators can simply place any machinable part anywhere they like in a machine. Using its data-base of CAD drawings, the machine would then identify the part, decide how it should be machined, and execute the necessary welding operations. In principle, there would be nothing else the operator would have to do.
Of course there is still some way to go before this becomes reality – the evolution of autonomous driving would perhaps be an apt comparison – but we are clearly heading in the right direction. One example of a sensor capability that really does seem to be just around the corner is material recognition, a technology that will make processes such as laser marking even simpler. The future certainly looks bright!

A multinational corporation and one of the biggest suppliers to the automotive industry, Bosch thrives on its reputation for making products that conform to the highest standards of quality. At its Waiblingen plant, the company produces components for electronic control units (ECUs). Bosch firmly believes in putting plenty of safeguards in place to ensure top-quality results, and its plastics laser transmission welding line for connector strips is no exception, combining temperature control with melt travel monitoring. “Our primary goal was to eliminate downstream quality checks while maintaining a high standard of documented quality assurance,” says Hubert Hickl, project manager for connector-strip laser welding at Bosch. In this process, a direct diode laser welds plastic modules securely to a modular frame. A pyrometer measures the heat radiated through- out the entire process and, at the same time, a scanner makes multiple passes along the weld contour. The system also includes a melt travel sensor that monitors the lowering of the component during laser transmission and switches off the welding program once the specified weld travel has been completed. The results of the measurements are collated and automatically documented. “The cut-off switch is precise enough to enable us to meet very tight positional tolerances—crucial for the downstream assembly processes. The combination of melt travel and temperature monitoring has radically increased the likelihood of detecting errors.”
Image: Robert Bosch GmbH
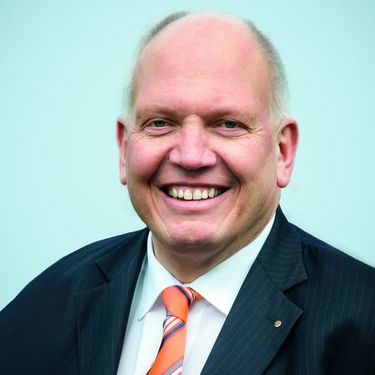
200 times a second: That’s how frequently the laser beam strikes the surface of the aircraft in LR Systems’ paint-stripping system. At the same time, a camera captures a high-resolution spectroscopic image of the results no less than 400 times a second. A software program analyses these images, determines whether the surface below the paint has been reached, and adjusts the position and speed of the robot arm and the power of the CO 2 laser accordingly — all at the same rate of 400 times a second. All aircraft have to be stripped at regular intervals and provided with a fresh coat of paint. “Our ultimate goal is that the laser at the end of our robot arm should be able to de-paint an entire aircraft,” says Peter Boeijink, CEO of robotic solutions provider LR Systems in the Netherlands. “And it should be able to do that faster and better than any human, and without user intervention. We’re set to launch the system in 2018.” They have certainly had to overcome plenty of challenges to reach this point, not least working out how the robot could detect when it had removed the paint and reached the underlying paint layer — or even the composite surface beneath. A classification algorithm evaluates the images based on ten different criteria and forwards the signals directly to the robot- and laser-control units. “We have to transfer huge quantities of data incredibly fast, so a digital fieldbus signal would be much too slow for our purposes. That’s why we switched to an analog input for the feedback controller.” LR Systems even decided to incorporate self-learning control software: “The algorithm learns from its mistakes and gradually starts to understand our criteria, apply them autonomously, and improve them. In other words, it gets better and smarter with every aircraft.”
Image: Onno van Middelkoop
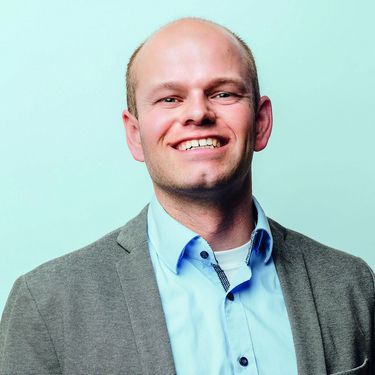
Peter Schömig, Team Manager Corporate Production, Welding and Brazing Processes at ZF, has a clear goal: “We want to significantly reduce the amount of destructive testing we use. We need to find other ways of guaranteeing high-quality parts.” Automotive supplier ZF has been trying out a new laser-welding process for powertrain components that takes advantage of interferometric monitoring — and Schömig is confident it is suitable for high-volume production. An optical coherence tomography (OCT) system attached to the laser optics monitors the capillary during deep penetration welding and measures the weld depth in real time, providing a direct quality-control solution along the entire length of the weldseam. “The quality standards for the powertrain are extremely high, because the entire engine torque is transmitted through the welded parts. That’s why it’s such a big plus for us to be able to detect and document the penetration depth at every point of each individual part. It allows us to significantly reduce the costly and laborious use of metallographic sections.” If the sensor detects that the required depth of penetration has not been reached or has been exceeded, then the system sounds an alarm. “So if the process goes wrong, we discover that right with the very first part rather than at the end of the shift. That means we can take action straight away to avoid producing parts that end up having to be scrapped.” Schömig nevertheless emphasizes that the current incarnation of the OCT system is essentially just a good interim solution: “In the long run, we hope to incorporate a control sensor that not only reliably detects the weld depth, but also takes action to ensure that everything goes exactly as it should.”
Image: Holger Riegel