Paula cuddles up to her mother and is spellbound as she listens to her bedtime story. She loves books, and loves it especially when someone reads to her. Right after her birth, it was unimaginable that the now five-year-old would be able hear words or even music. Paula was born deaf. She could not hear the voices of her parents or siblings, or even the noises in her surroundings. One in 1,000 children in Germany are born deaf just like Paula. Their families then have to make a decision: a hearing implant or sign language? Paula’s parents wanted to give their daughter a life with as few barriers as possible and decided to go for a so-called cochlear implant. This is a hearing aid implanted in the cochlea.
Complex system
These hearing systems comprise an audio processor with a microphone and the implant itself. The patients wear the processor behind the ear. It captures noise in the surroundings and adapts the sounds and volume, reduces disruptive background noise and amplifies subtle sounds. Surgeons fit the implant under the skin. It assumes the function of the sensory hairs in the ear, triggers the auditory nerve, once more making it possible to hear.
Removing barriers to hearing
The Austrian company MED-EL, based in Innsbruck, has specialised in the development and production of cochlear implants. Implantable and non-implantable auditory systems are part of the product portfolio. The family company has 2,500 employees. Customers include clinics, doctors and also audiologists who support patients after the operation.
Dietmar Köll, responsible for production at MED-EL, says: "The inability to see may distance you from objects, but the inability to hear distances you from people." He and his team are working on changing this. "Through our products, we aspire to overcome hearing loss as a barrier to communication and quality of life, and assist people in rediscovering their enthusiasm for life. What a great job.”
Every ear is different
For their products, MED-EL relies on a wide range, because just like every human is an individual, so is every ear - or every cochlea. Dietmar Köll explains: "We operate with a high degree of dynamism and strive to integrate customer feedback into our product range. This is why we offer a very comprehensive portfolio with a modular structure. We have different processors and implants. We assemble them according to the patient’s individual requirements. This approach enables us to find the most appropriate solution for different listening scenarios.”
Precise markings in the smallest of spaces
Small batch sizes with individual markings are therefore part of day-to-day operations in the Innsbruck-based production. MED-EL assembles the cochlear implants and audio processors here and adds markings to the small metal and plastic components. At the moment, two trends in particular are keeping the hearing experts from Tyrol busy: The parts are getting smaller and smaller to make them more pleasant to wear. Simultaneously, the demands for product traceability and comprehensive documentation of production processes are on the rise. This means that the production team have to apply more and more markings on increasingly smaller spaces. In addition, they need to be legible and resistant. This requires reliable production technologies with high standards.
High-contrast and resistant
At MED-EL, three TruMark Station 5000 systems from TRUMPF do the job. Equipped with lasers from the TruMark Series 3000, they mark components made of titanium, platinum-iridium and plastic. Christoph Fankhauser is the deputy production manager. He explains: “We primarily apply serial numbers and so-called unique device identification codes, or UDIs, to metal and plastic parts. This universal machine-readable product identification is mandated for medical products in Europe. We also apply symbols such as arrows and instructions to the parts to make handling easier for the users.” Uniform processes are extremely important for MED-EL, as many markings are visible on the end product. Achieving a high contrast is crucial for this purpose, as it guarantees excellent readability. “And, of course, the markings have to be reproducible. In other words: The result must always be the same even if the material quality fluctuates,” emphasises Fankhauser. “High performance stability is the prerequisite. "The TruMark laser fulfills these requirements, even when marking extremely small parts.”
With all five senses
Paula is not aware of all the work the cochlea experts put in. Playing loudly and happily in the flat with her siblings is just part of her normal routine as much as going to kindergarten every day. Her cochlear implant has meant that she can hear life - and she is enjoying it with all her senses.
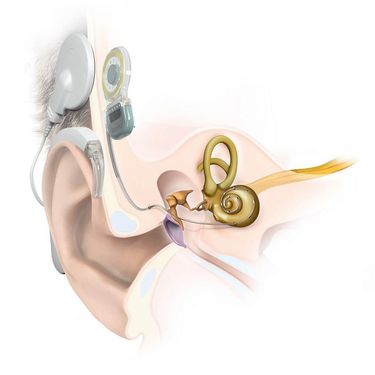
A cochlear auditory solution consists of two parts: An audio processor with microphone which is worn behind the ear and captures sounds and noise and the actual implant under the skin. An electrode extends from the implant into the inner ear. This long, flexible platinum wire is equipped with electrodes and coated with silicone. Any noises the audio processor captures reach the implant as electrical signals. It converts them into electrical pulses, which the electrode directs into the cochlea and stimulates the auditory nerve. It in turn passes the auditory perceptions on to the brain which interprets them as sounds and noise. Profoundly deaf or people who were born deaf can use it to learn to hear. The artificial pulse created by the implant sounds different than natural noises. Just like a new language, the brain must first learn how to understand them. Regular speech training will help.
© MED-EL