The gleaming white floor reflects the LED lighting. The CNC machines are lined up like small spaceships at the space-port, ready to take off. Inside, carbide blanks, carefully cooled by a permanent supply of freshly prepared coolant, are transformed into shimmering tools. They don't leave the construction space until the machine has removed the last micrometer of material exactly according to plan.
Products leaving the production hall at Horn must meet the requirements of Swiss watch manufacturers, medical technology or the aerospace industry. The company, founded in 1969 by Paul Horn, is known worldwide for precision tools for sophisticated chipping. In other words: Horn is one of only a few companies that understand how to remove material down to the last micron.
Learning the hard way
It seems all the more surprising that this company would have a machine whose strength is exactly the opposite. For on the first floor of Tübingen Plant 2, Horn is perfecting its expertise in additive manufacturing with a 3D printer from TRUMPF. In the TruPrint 3000 from TRUMPF, two 500 watt lasers work around the clock to transform the ideas of developers and designers from the finest metal powder into reality.
“Only those who dare to try something new can learn,” said Horn’s recently deceased managing director, Lothar Horn, in an interview in 2019. Matthias Luik, Head of Research and Development since 2010, elaborates: "Anyone who proclaims technological leadership in a sector must not turn a blind eye to new technologies." Therefore it was a natural step for the precision tool experts to create their own additive manufacturing (AM) department at the Tübingen headquarters in 2018, with the aim of exploring the limits and possibilities of 3D printing. “We already had the expertise for substances and materials in-house, and we are able to analyse the powder used ourselves,” explains Matthias Luik. “With everything else we had to learn the hard way.” Even that sounds euphoric coming from him – “learning from mistakes” is part of Horn’s corporate culture.
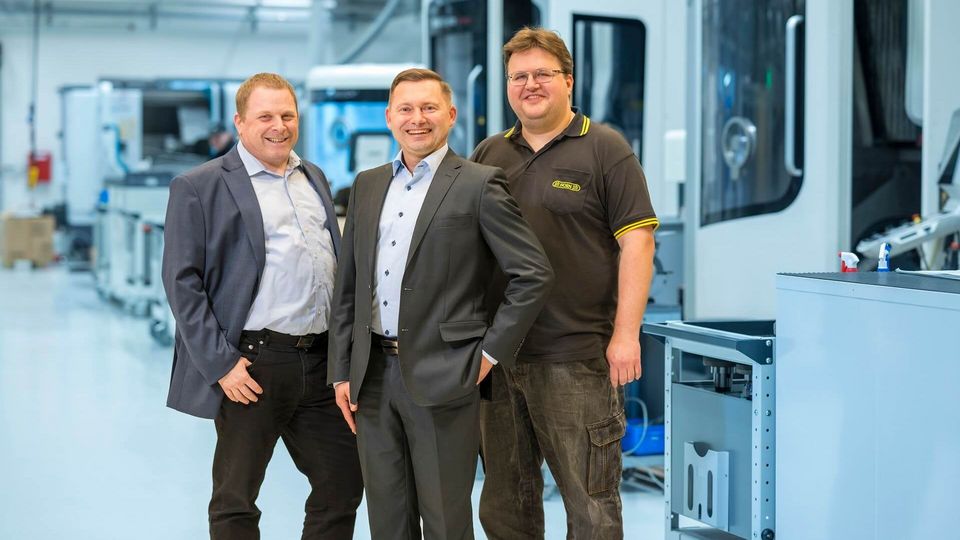
Matthias Luik (left), Head of Research and Development at Horn, with the AM team: Dr Konrad Bartkowiak (centre), Head of the Additive Manufacturing department and Michael Schäfer (right), Designer in Additive Manufacturing and primary operator of the new TRUMPF system at Horn.
Unsatisfactory
After just three years of intensive testing and meticulous examination of powders, process parameters, printing processes and prototype production, the machine initially purchased from another manufacturer could no longer meet the needs of the AM team. A new machine was needed. After a structured, six-month benchmark test including a long-term test, assessment of service quality and communication, Horn ultimately decided on TRUMPF. "The thing simply works“, remarks Dr Konrad Bartkowiak, Head of Additive Manufacturing at Horn, while praising the robustness and consistent quality of the system. The low downtimes and process stability of the TruPrint 3000 also seem to have a positive influence on the work-life balance of the AM team: “Since we started working with the TruPrint 3000, I go into the weekend much more relaxed,” adds Michael Schäfer – he is a designer for additive manufacturing at Horn and the main operator of the new TRUMPF system. In the past, when error messages appeared or build jobs were interrupted, he had to work extra shifts to get the machine running again.
Quickly becoming productive
Bartkowiak and Schäfer's "baby" has been in the production department since May 2022; the team has been working with the system for production since September. In the first seven months, they implemented more than 20 internal and external projects: commissioned work for customers, prototypes for the tool catalogue and components for the production systems in order to get the most out of their own machines. For example, a coolant nozzle for a machine on which employees grind workpieces. The dozens of internal channels of the coolant nozzle enable precise and pinpoint cooling of the grinding point and workpiece. The result: The grinding point lasts longer and the quality of the processed workpiece is higher. "The component would have been impossible to produce using conventional manufacturing methods due to the very fine, internal structures,” explains Matthias Luik.
Exploring limits
In the future, Horn wants to further increase the utilisation of the machine. A prototype of a previously conventionally manufactured turning tool is currently in the test phase and could soon become part of Horn's product catalogue. At that point nothing would stand in the way of series production. “Our AM department is currently not focusing on series production,” says Luik, Head of Development. “First and foremost, we want to use the TRUMPF system to explore the limits of the technological progress that additive manufacturing offers us. This is what will ultimately give Horn a market advantage and our customers better tools for their business. “The biggest advantages of 3D printing for us are currently in the areas of prototype development, weight reduction and cooling.” In future, the company also wants to enter into hybrid production of tools. The idea is to use conventionally manufactured tool blanks on which the tool head with internal cooling channels is additively printed. This can subsequently be equipped with indexable inserts made from different cutting materials. Horn also offers its customers the production of 3D printed components with the entire process chain - including complete post-processing.
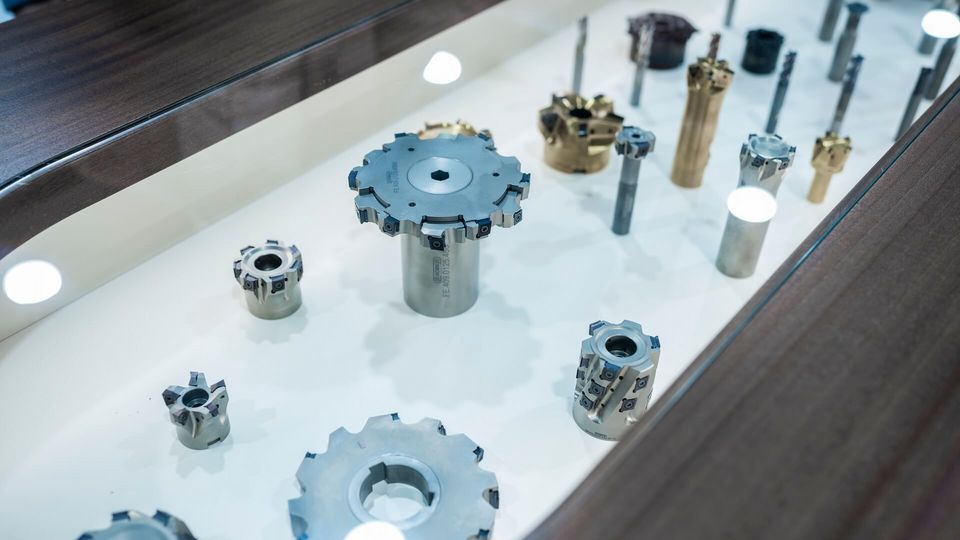
Das erste additiv gefertigte Drehwerkzeug könnte schon bald das Sortiment der mehr als 25.000 Standardwerkzeuge von Horn erweitern.
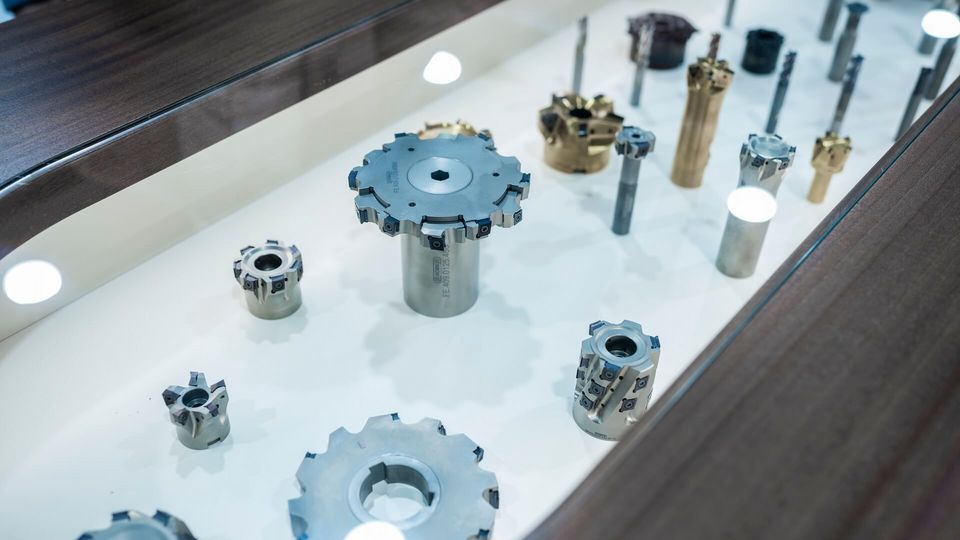
The first additively manufactured turning tool could soon expand Horn's range of more than 25,000 standard tools.
Investing in the future
At Horn, there is no question that additive manufacturing is here to stay. The company is already training its own AM talent with its first trainee projects on the TRUMPF system. And the company has already taken precautions in the event that the AM business suddenly explodes: At Plant 2, Horn has reserved plenty of space for additional additive manufacturing systems in the immediate vicinity of the TruPrint 3000.