In which areas of application is LMF particularly attractive?
The spectrum is wide. Everything from tool and mold making, where complex tools are made with conformal cooling, all the way to applications in the dental industry for generating crowns and dental bridges. We’re seeing a lot of potential with demanding applications in the aviation industry and turbine construction. Even suppliers are starting to get involved in additive manufacturing. We’re seeing interest in a lot of different places.
This wasn’t always the case.
We started working on selectively fusing metals, what we now call Laser Metal Fusion (LMF), in 1999 together with the Fraunhofer ILT. We used the experience we gained from this to develop our first LMF machine—the TrumaForm. The machine was introduced to the market in 2003, which was pretty early in the game for industrial additive manufacturing solutions. Unfortunately, it was a bit ahead of its time. The market was still heavily focused on research and development applications, as well as a few niche applications, so we set further development aside for the time being.
What made TRUMPF get involved in LMF again in 2014?
3D printing is on the advance now, so it was a good point for us to get back into LMF. Our customers want to be able to produce more than just prototypes now—they also want to be able to use components in series products. So they expect solutions that can perform at an industrial level. And that’s where we come in. We provide machine tool solutions that enable our customers to produce demanding components economically.
We’ve set up a department at our headquarters in Ditzingen to handle the continued development of the LMF process. All the operations that are essential to this end are located under the same roof, including our production areas. Our own development work is focused on current and future machines. We’ve also put together a team of application engineers who are experts in their respective fields and are therefore capable of addressing the specific needs of our customers.
What do these customers use LMF for?
Operators can use metal 3D printing to create working components directly from a 3D CAD model. This allows the customer to be much more flexible than they would be using classical processes, where tools and equipment have to be built first. LMF also offers a level of geometric design freedom that you just can’t get with other processes. There are other industry-specific advantages, such as the ability to design components bionically, which paves the way for the ultimate in light-weight aviation designs.
Weight savings of between 30 and 50 percent are possible with the same - or even better - mechanical qualities. In other industries, customization is a big plus. In prosthetics revision, for example, custom implants can be produced within a very short time. And even jewelry manufacturers can easily produce unique pieces using LMF.
Is there no getting around 3D printing with future production?
We shouldn’t think of 3D printing as the holy grail that’s going to revolutionize production overnight. Besides the printing process itself, it’s just as important to keep an eye on up and downstream processes. It doesn’t make any sense to print a part overnight when the finishing work is going to take a week.
That sounds kind of forbidding.
Not at all. Companies that have already mastered the process chain can gain a real competitive advantage with LMF. And that’s what we want to help our customers do—to help them make the entry into additive manufacturing. This usually begins with us working together with the customer on an application project to realize a specific component of theirs with LMF technology. In addition to LMF machines, we also offer 3D software and the right powder materials for customers who have found the right use for the technology.
What LMF machines does TRUMPF have available for customers?
The TruPrint 1000 has been on the market since the end of 2015. This machine is very compact and can economically produce parts the size of a fist (a diameter of 100 millimeters by 100 millimeters tall). We’ve also already presented a demonstrator for the TruPrint 3000, which features a larger production area with a diameter of 300 millimeters at a height of 400 millimeters, as well as a more powerful laser. Beyond that, we’re working on machines with much higher productivity levels. This requires the use of multiple lasers as well as a preheated construction chamber in order to reliably process more materials.
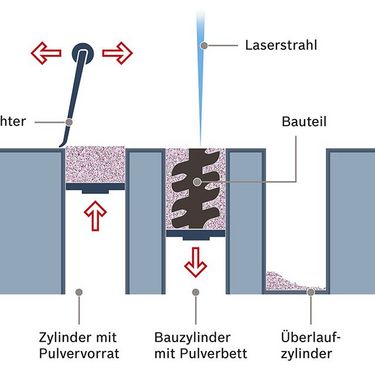
The so-called “coater” applies powder from the storage container to the construction cylinder. Then a laser melts the first layer of powder according to the part contour. After this, the construction cylinder drops. This process is repeated until the component is complete. Each time the coater returns to the storage cylinder, it cleverly tilts in order to reverse quickly without colliding with the powder bed or the constructed component. To ensure component quality, the entire process in the chamber takes place under protective gas.

The TruPrint 1000 from TRUMPF is a compact machine for the production of small metal components by powder-bed-based laser melting, which is also called “laser metal fusion”. Starting from metal powder and laser light, it is able to quickly produce components of virtually any geometric shape. Even complex shapes can be transformed simply from the CAD design into a real, top-quality component.
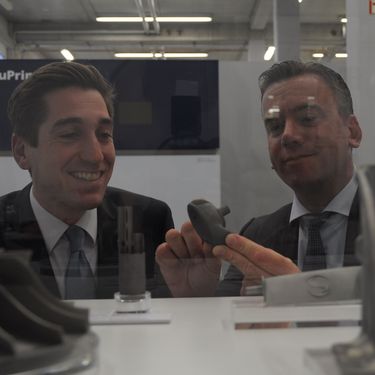
Daniel Lichtenstein (left) is in charge of developing the new Additive Manufacturing business. Tobias Baur heads up the new department at TRUMPF.