Autonomous, free-moving transport systems, repair instructions displayed in data glasses, parts with built-in intelligence: How connected manufacturing is changing sheet metal processing – and what factories of the future will look like.
TRUMPF demonstrates smart-factory solutions at Blechexpo trade fair
Stuttgart; November 7, 2017 – At Blechexpo 2017, TRUMPF will be exhibiting solutions that are faster, simpler and more reliable than ever before. Thanks to these innovations, sheet-metal processors will be equipped for Industry 4.0. In many factories, even today, around 80 percent of all operations consist of indirect processes, such as upstream and downstream job handling. This unnecessarily wastes time, especially in the case of small batches. To remain competitive, companies simply must find ways of reducing the high proportion of activities that create no added value.
TRUMPF will share many examples from its Smart Factory in Chicago to show trade-fair visitors what digitalization can do for them today and tomorrow. The star of this Smart Factory is a TRUMPF production-control system that processes data in real time. It simplifies almost every stage in the production process, from the initial inquiry to invoicing. The benefits of the smart factory for sheet-metal processors can be summarized in ten points:
1. Fast processing of purchase orders and quotations
Online commerce has set new standards, in which products can be ordered via the internet in just a few clicks. In the Chicago Smart Factory, the AXOOM online store allows people to order parts quickly and simply from anywhere. A taste of the future: no more phone calls or back-and-forth inquiries. Instead, the customer is informed of the price and delivery date before the order is placed. The TruTops Fab and TruTops Boost solutions from TRUMPF automatically calculate the costs and even prepare a quotation. These solutions not only ensure that the job order is entered in the manufacturing schedule, automatically and without error, but also make sure that the right machine does the job.
2. Reliable, automated operation
Digital production control facilitates automated night-shift operations. The system automatically reports any malfunctions, and the night-duty supervisor can take immediate action without even having to be on the premises. Without such real-time alerts, there is a risk that the machines might come to a standstill or, worse still, produce a lot of rejects.
3. Fewer mix-ups because each part knows its destination
The metal sheets processed in smart factories know what parts they will be turned into. As well as cutting the blanks, the TruLaser 5030 fiber laser cutting machine marks the parts with a code containing job information such as the customer ID. If required, the code can also include data referring to the next step in the machining process, and thus be used to specify processing parameters. All the operator of the bending machine needs to do is scan the code, and the appropriate machining program is selected automatically. This saves time by eliminating the need for paper documentation.
TRUMPF is also testing new ways of sorting parts in the Chicago Smart Factory. Each part cut from the blank can be digitally allocated to a specific job order. For example, a display panel on the sorting station shows the information of the code for each part, enabling the operator to identify which parts belong to which jobs.
4. The next part arrives without asking
In the Chicago Smart Factory, parts generally travel through the entire production facility. But standalone stations are also on hand. The parts are transported from one station to the next by an autonomous transport system that TRUMPF is testing in Chicago. Three STOPA VARIOCARTS move freely between the stations, without rails or power cords.
5. Efficient inventory management
Unnecessarily full warehouses are yesterday’s news: TruTops Fab always knows how many unprocessed sheets are available in the warehouse, and which storage locations are full or empty. The real-time information provided by this system makes it easy to see whether enough material is available to process a certain job order. It even includes remainder sheets in the planning data. The storage module uses a weighing system to automatically book goods received. As a result, idle time due to the unavailability of parts in the warehouse is a thing of the past.
6. Certainty replaces guesswork
TruTops Fab always knows which parts are where in the manufacturing process: whether still in the warehouse or already in transit. TRUMPF staff in Chicago are testing intralogistics systems capable of locating parts anywhere in the factory at any time. People no longer need to commit time to searching for the parts. They utilize miniature transponders to automatically track parts, from their storage locations in the warehouse to the fully automated carts that transport parts within the factory.
7. Customer response from anywhere
TruTops Fab lets people call up the processing status of job orders at any time. Whether in the factory or in the field, production employees can use their smartphone or other mobile device for permanent access to in-factory information. In everyday practice, this means that customers who inquire about the status of their orders will get reliable updates – anytime, from anywhere.
8. Filling idle time with productive work
The production control system provides a complete, real-time overview of order statuses. Job lists show not only which machines are processing which orders; they also indicate which machines are idle. Buffer times can thus be used to complete rush jobs.
9. Higher productivity through predictive maintenance
The TRUMPF solution for monitoring the machines goes by the name of Condition Guide. It comprises sensors that monitor the condition of machine components essential for the quality of laser cutting – for instance, by verifying the cleanliness of the cooling water.
The Condition Guide also displays warnings in advance of the need to maintain or replace components. This predictive approach reduces unplanned maintenance downtime and thereby increases productivity.
10. Smart glasses simplify maintenance
Internet-connected smart glasses save time and money during service tasks. The Visual Online Support (VOS) app enables fast two-way communication with the customer service team in the form of images, audio and video files. Technical issues can be resolved remotely, quickly and easily. Nothing could be simpler: the video images sent by the service center are projected onto the field technician’s data glasses – whose hands are free to get the job done.
Digital photographs in print-ready resolution are available to illustrate this press release. They may only be used for editorial purposes. Use is free of charge when credit is given as “Photo: TRUMPF”. Graphic editing – except for dropping out the main motive – is prohibited.
Лица за контакти
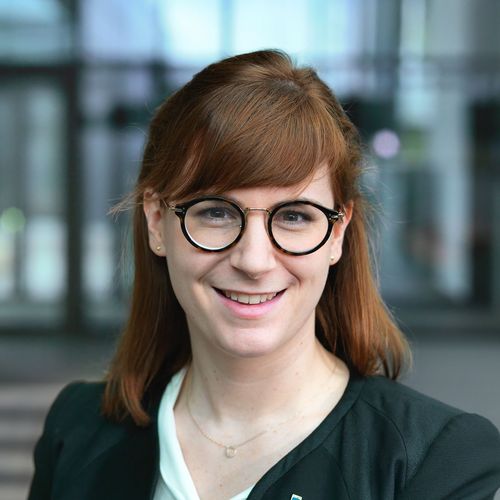