
Bosch, unter anderem einer der größten Zulieferer der Automobilindustrie, lebt von seinem Ruf, höchste Qualitätsstandards bei seinen Produkten zu setzen. Im Waiblinger Werk werden Komponenten für Steuergeräte hergestellt. Beim Kunststoff-Laserdurchstrahlschweißen, der sogenannten modularen Messerleiste, setzt man auf mehrfache Sicherheit: Bosch kombiniert dabei Temperaturregelung mit Fügewegüberwachung. Hubert Hickl, Projektleiter Laserschweißen Messerleiste bei Bosch: „Unser Hauptziel war es, nachgelagerte Kontrollen einzusparen und trotzdem eine höhere, dokumentierte Qualitätssicherheit zu erreichen.“ Ein Diodendirektlaser schweißt Kunststoffmodule auf einen Modulrahmen fest. Ein Pyrometer nimmt die abgestrahlte Wärme während des gesamten Prozesses auf. Gleichzeitig bewegt sich ein Scanner mehrmals entlang der Schweißkontur. Ein Fügewegsensor überwacht das Absenken des Bauteils und beendet das Schweißprogramm bei Erreichen eines vorgegebenen Schweißweges.
Die Messergebnisse werden verknüpft und automatisch dokumentiert. „Dank der genauen Wegabschaltung können wir enge Positionstoleranzen einhalten. Dies ist entscheidend für die nachgelagerten Montageprozesse. Durch die Kombination von Füge- und Temperaturüberwachung hat sich die Fehlerentdeckungswahrscheinlichkeit deutlich erhöht.“
Bild: Robert Bosch GmbH
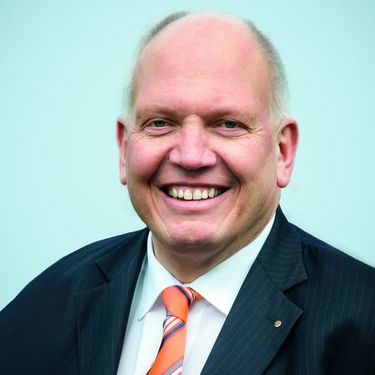
200-mal pro Sekunde trifft der Laserblitz den zu entfernenden Flugzeuglack. 400-mal pro Sekunde schießt eine Kamera ein hoch aufgelöstes spektroskopisches Bild des Ergebnisses. 400-mal pro Sekunde analysiert eine Software dieses Bild, stellt fest, ob die Grundschicht schon erreicht ist, und regelt daraufhin Position und Geschwindigkeit des Roboterarms sowie die Leistung des CO2-Lasers. Jedes Flugzeug muss regelmäßig entlackt und mit neuem Lack versehen werden. Peter Boeijink, CEO bei dem niederländischen Roboterspezialisten LR Systems, sagt: „Unser großes Ziel ist es, dass unser lasertragender Roboterarm das komplette Flugzeug entlackt — selbstständig, schneller und besser als jeder Mensch. 2018 kommen wir damit auf den Markt.“ Auf dem Weg dorthin waren viele Hürden zu nehmen. Eine davon war die Frage: Woher weiß der Roboter, wann die Schicht abgetragen ist, wann der Grundlack oder gar die hochempfindliche Kompositionsoberfläche erreicht ist? Ein Klassifikationsalgorithmus wertet die Bilder nach zehn Kriterien aus und gibt die Signale direkt an Roboter- und Laser-steuerung weiter. „Die riesigen Datenmengen müssen dabei so schnell bewegt werden, dass ein digitales Feldbussignal für uns viel zu langsam war. Wir wichen daher auf einen analogen Eingang für den Feedback-Controller aus.“ LR Systems baute eine selbstlernende Steuerungssoftware ein: „Der Algorithmus lernt aus seinen Fehlern und beginnt, unsere Kriterien zu verstehen, sie selbstständig anzuwenden und weiterzuentwickeln. Mit jedem Flugzeug wird er klüger und besser.“
Bild: Onno van Middelkoop
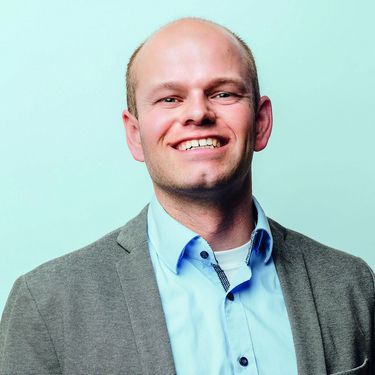
Peter Schömig, Gruppenleiter für Schweiß- und Löttechnik bei ZF Friedrichshafen, hat ein klares Ziel: „Wir wollen deutlich weniger zerstörende Prüfungen machen. Die Qualität der Teile muss auch anders sichergestellt werden können.“ Der große Automobilzulieferer ZF hat ein neues interferometrisch überwachtes Laserschweißverfahren für Teile im Antriebsstrang getestet und Schömig empfiehlt es für den Serieneinsatz. Ein sogenannter OCT (Optical Coherence Tomograph) an der Laseroptik schaut während des Tiefschweißens in die Kapillare und misst unterdessen in Echtzeit die erreichte Schweißtiefe — eine direkte Qualitätskontrolle über die gesamte Nahtlänge. „Wir haben es im Antriebsstrang mit extrem hohen Qualitätsanforderungen zu tun, da das komplette Drehmoment des Motors über die geschweißten Teile läuft. Darum ist es für uns ein Mehrwert, wenn wir für jedes einzelne Bauteil die Einschweißtiefe an jeder Stelle kennen und dokumentiert haben. Die aufwendigen metallografischen Schliffe können wir dadurch deutlich reduzieren.“ Stellt der Sensor fest, dass die gewünschte Einschweißtiefe nicht erreicht oder überschritten wurde, schlägt das System Alarm. „Wenn uns der Prozess wegläuft, erkennen wir das also ab Bauteil 1 und nicht erst am Schichtende. So können wir sofort eingreifen und vermeiden die Produktion von Ausschussteilen.“ Den OCT in seiner jetzigen Form sieht Schömig allerdings nur als gute Übergangslösung: „Längerfristig erhoffen wir uns hier einen regelnden Sensor, der die Einschweißtiefe nicht nur zuverlässig feststellt, sondern aktiv dafür sorgt, dass alles stimmt.“
Bild: Holger Riegel