As a result of the war in Ukraine, the sanctions imposed on Russia and spiraling energy costs, the price of raw materials for sheet metal processing has never been higher. Yet even without these factors, there are sound ecological reasons for being more sparing in the use of steel, copper, aluminum and other metals. In other words, it is now doubly worthwhile for companies to cut their consumption of materials. As a solution provider to the sheet metal processing industry, TRUMPF has developed a number of technologies that help customers prevent material wastage while increasing their manufacturing productivity.
1. Nano joints: Closer nesting and less material wastage
Nano joints, a new process from TRUMPF for use with laser cutting, offers a simple way of reducing the consumption of materials in sheet metal processing. As a rule, when a component is laser cut from a sheet of metal, the part remains connected to the remaining sheet by small tabs known as micro joints. These prevent cut parts from banking out when the rest of the sheet is being cut. Nano joints are even smaller retaining tabs that minimally connect the part to the remaining sheet. The use of nano joints not only boosts process reliability but also saves material, since parts can now be nested directly adjacent to one another in the sheet. Furthermore, production workers are able to remove the components more easily after cutting. This is because they do not need to apply as much pressure to separate the parts from the sheet. Unlike micro joints, barely any force is required to remove the component from the scrap skeleton This assists the workforce and reduces non-productive time.
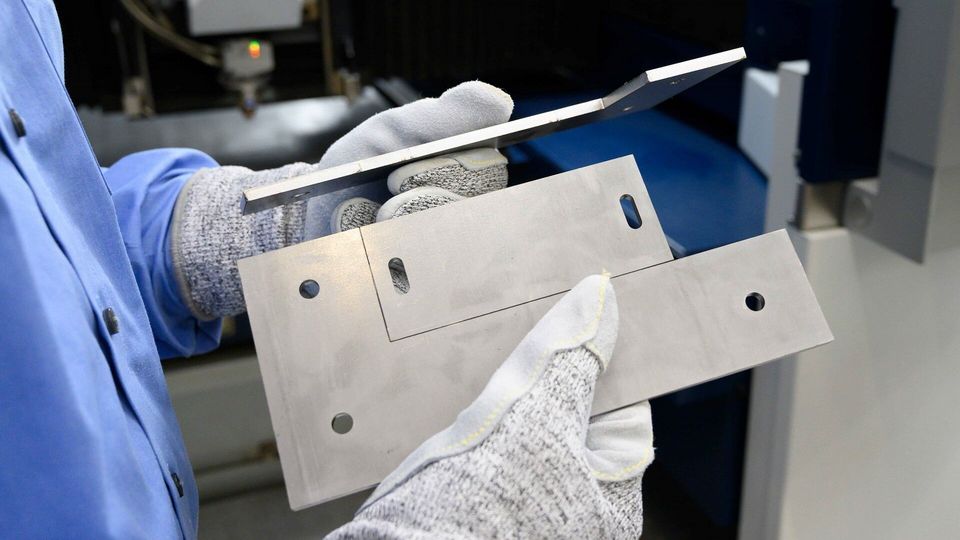
With TRUMPF nano joints, laser cut parts can now be nested directly adjacent to one another in the metal sheet.
2. Drop & Cut: Making optimum use of remainder sheets
Many TRUMPF laser cutting machines feature the Drop & Cut function. This enables users to make optimum use of remainder sheets. A production worker simply takes a leftover metal sheet from which parts have already been cut and places it in the machine work area. Integrated cameras then transfer the image of the remainder sheet onto the display of the control panel. Via touchscreen, the operator can now position additional parts on the remainder sheet for cutting. The operator then starts the machine, and the laser cuts out the shapes from the leftover sheet. This method is ideal when only a small number of components are to be cut – as in the production of spare parts. Drop & Cut reduces scrap by as much as 14 percent.
3. CoolLine: More parts from each sheet
CoolLine is another function that helps users reduce material wastage during laser cutting. This feature automatically sprays the workpiece with water, which vaporizes to provide optimum cooling during cutting. This prevents overheating, which would negatively impact cutting precision. The result is improved component quality and a reduction in the scrap rate. In addition, components can be nested more closely on the metal sheet, which also reduces material consumption.
4. Active Speed Control: Automatic control of feed rate
Another TRUMPF technology that helps users cut material wastage is Active Speed Control. This function autonomously regulates the feed rate during laser cutting. For this purpose, a sensor monitors the cutting beam from the center of the nozzle. By measuring the so-called process radiation, the system is able to determine whether molten material is forming as intended and, on this basis, calculate the fastest possible feed rate and make any necessary adjustments – a process it repeats many hundreds of times a second. In addition, Active Speed Control automatically regulates numerous other process parameters, including the position of the laser beam. The system informs the operator of any deviations, thereby helping companies prevent production of unusable parts and eliminate material wastage.
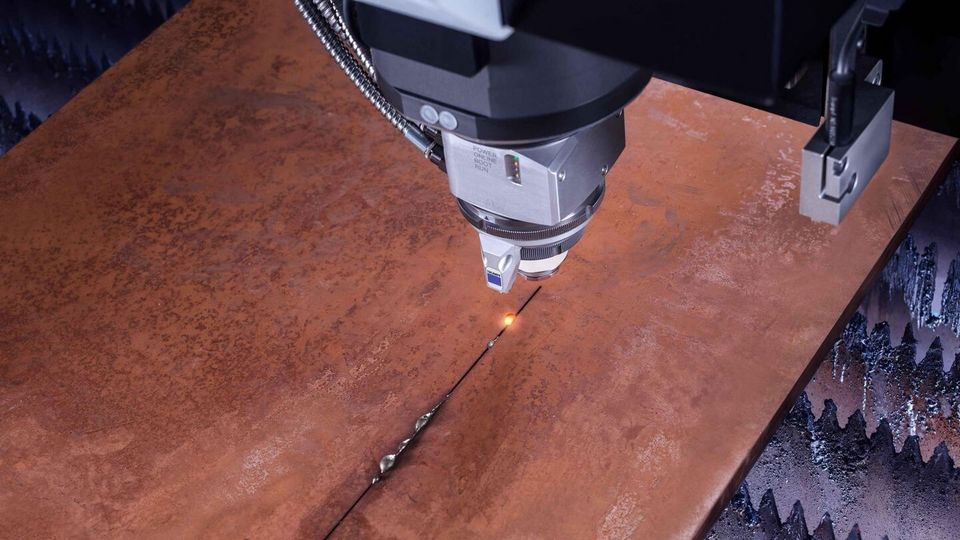
Active Speed Control from TRUMPF autonomously regulates the feed rate during laser cutting.
5. Condition Monitoring: Detecting malfunctions before rejects are produced
Less scrap automatically means lower material consumption. TRUMPF offers a number of solutions to enable continuous monitoring of machine data. All of them help reduce scrap. Condition Monitoring, for example, provides early warning of malfunctions. For this purpose, customer machines are digitally connected to the TRUMPF IT system. All connected machinery sends real-time data to the TRUMPF Predictive Service Center for evaluation by smart algorithms. Any deviations are immediately detected. If, for example, the pressure in the machine room is too high, the operator is automatically notified and can schedule corresponding maintenance measures. This helps companies reduce scrap as well as increase machine availability and prevent unplanned downtime.
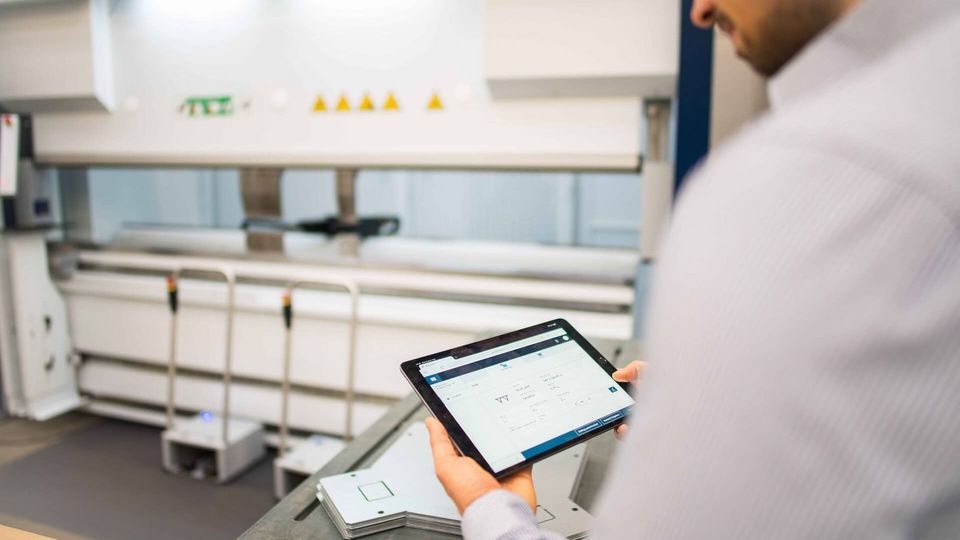
Condition monitoring – the monitoring of machine status data – helps companies reduce scrap and save material.
6. 3D printing: Applying material only where it is required
In terms of material wastage, additive manufacturing – better known as 3D printing – is the most economical process of all. This is because a 3D printer only uses the exact amount of material required to produce a component. In the case of laser metal fusion (LMF) technology, the laser beam within the 3D printer manufactures the component layer by layer. Any excess powder is recovered and can be reused. By comparison, conventional machining processes such as milling produce a large amount of chips. Depending on the component being produced, as much as 80 percent of the raw material is wasted. In addition, 3D printing also saves weight by only using material where it is functionally required.
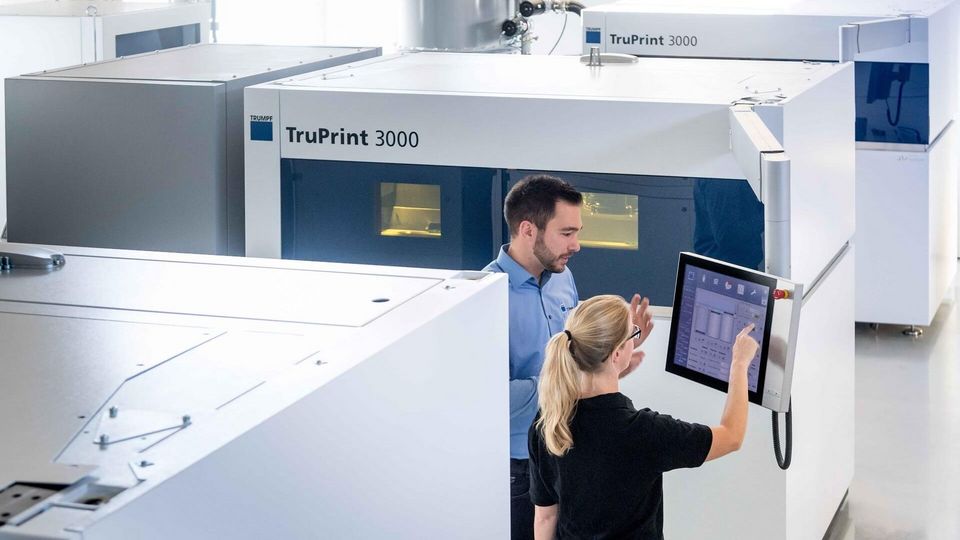
3D printing helps cut material consumption because the machine only uses what is functionally required for the actual part. Conventional machining processes such as milling often waste as much as 80 percent of the raw material.
7. Upcycling: Retrofitting machinery instead of scrapping it
Although a machine may no longer meet the latest standards for sheet metal processing, this is no reason to scrap it. In many cases, the machine can be retrofitted with the requisite technology. This saves not only money but also materials – after all, a standard piece of machinery in this sector weighs around 12 metric tons. TRUMPF offers a variety of solutions to help customers bring older machinery back up to specification. These include the OPC UA Retrofit. This enables companies to equip older machinery with an OPC UA interface – the international, platform-independent standard for data exchange in manufacturing. A similar upgrade is the Windows Retrofit from TRUMPF. This helps companies ensure that older machines continue to meet the increasing requirements for IT systems within their own company network. TRUMPF also supplies the Smart Power Tube IoT Box for its CO2 laser machines. This means companies can connect older machinery to the TRUMPF IT system. And should a company, despite best efforts, find itself no longer able to operate a veteran TRUMPF machine, the TRUMPF Resale Center can help. The team at the Resale Center will refurbish the machine and place it on the market. This way, a future buyer will be able to save money and cut material wastage.