CHU Bracket-designen är utformad för tillverkning genom fräsning där komponenten tillverkas av ett homogent block av Al7075 genom borttagning. Denna konventionella tillverkningsmetod leder till att ca 90 % av materialet blir till spån och innebär avsevärda begränsningar av komponentdesignen.
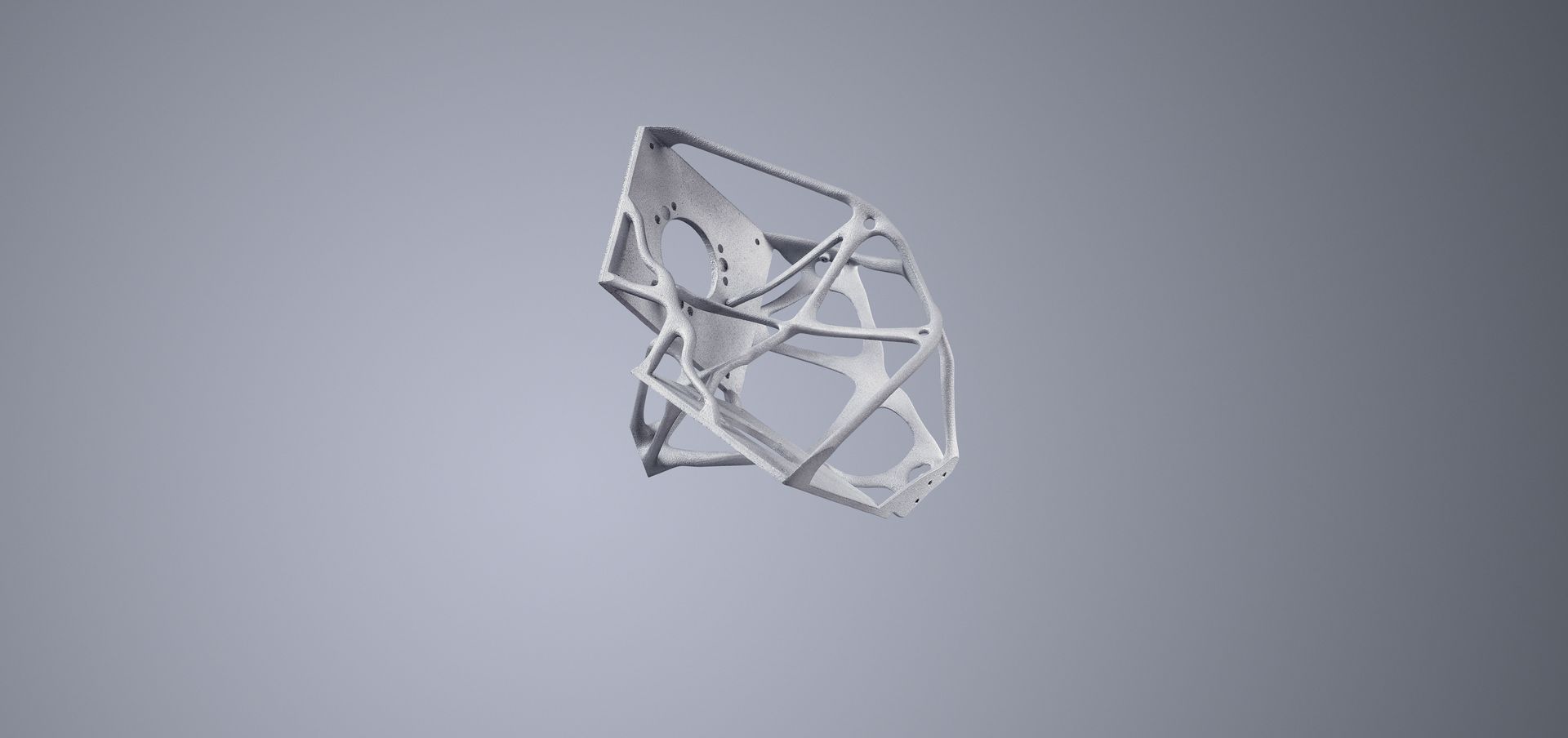
Additiv tillverkning av ett fäste till kamerahuvud (CHU)
Camera Head Unit Bracket I AlSi10Mg I TruPrint 3000
En satellit-startracker består av en kombination av två optiska kameror (”stjärnkameror”) som är justerade i en vinkel av ca 15 grader mot varandra. Kameraenheten (Camera Head Unit = CHU) skyddas mot termisk-mekanisk påverkan av det så kallade CHU Bracket, som konventionellt fräses ut från ett aluminiumblock. Jämfört med detta erbjuder den additiva tillverkningen många fördelar, särskilt när det gäller designfrihet och kvalitet. Startracker är en del av satelliten Flying Laptops som utvecklades 2014 av Institutet för Rymdsystem vid Universitet Stuttgart och som placerades i rymden för att beräkna position och orientering av satelliterna i rymden.
Vikten minskas med ca 30 % eftersom komponenten har optimerats topologiskt. De komplexare komponentstrukturerna kan tillverkas med Laser Metal Fusion.
Trots lägre vikt och mjukare aluminiumlegering utmärker sig den utskriva komponenten av en ungefär 43 % högre styvhet.
Om fästet tillverkas med ett TruPrint-system minskas den totala volymen med ungefär en fjärdedel.
På grund av sin design, som är belastningsoptimerad, får det med LMF producerade fästet 48 % lägre spänningstoppar jämfört med det konventionellt producerade fästet.
Med våra mjukvarulösningar kan du lita på en konstant hög produktkvalitet och dokumentation.
Jämfört med mekanisk tillverkning reduceras produktionskostnaderna för additivt tillverkat fäste med upp till 70 %. Samtidigt kan avsevärda kostnader sparas in vid raketstarten på grund av den lägre vikten.
Hur tillverkas Camera Head Unit (CHU) Bracket konventionellt?
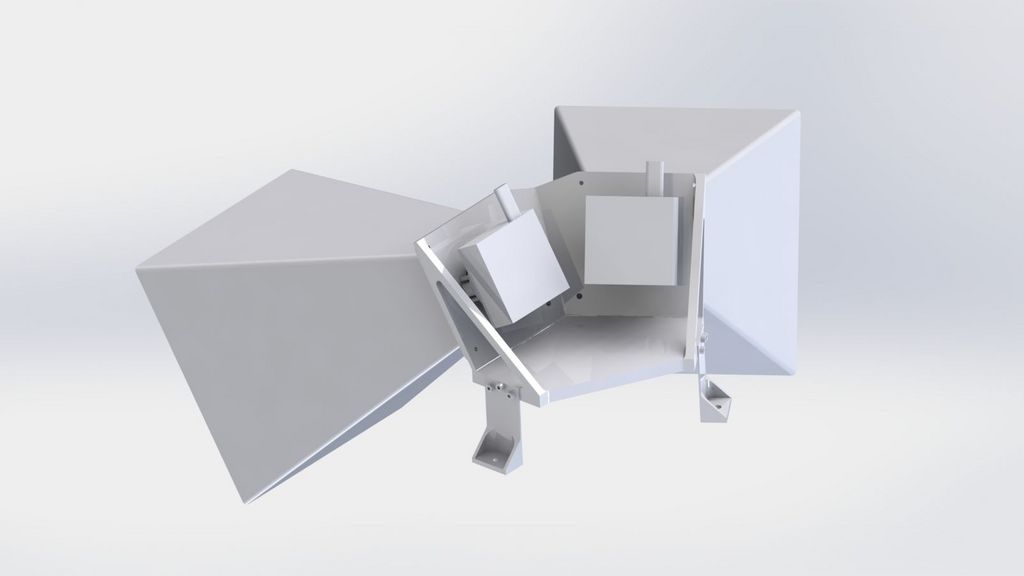
Konventionellt tillverkad Startracker
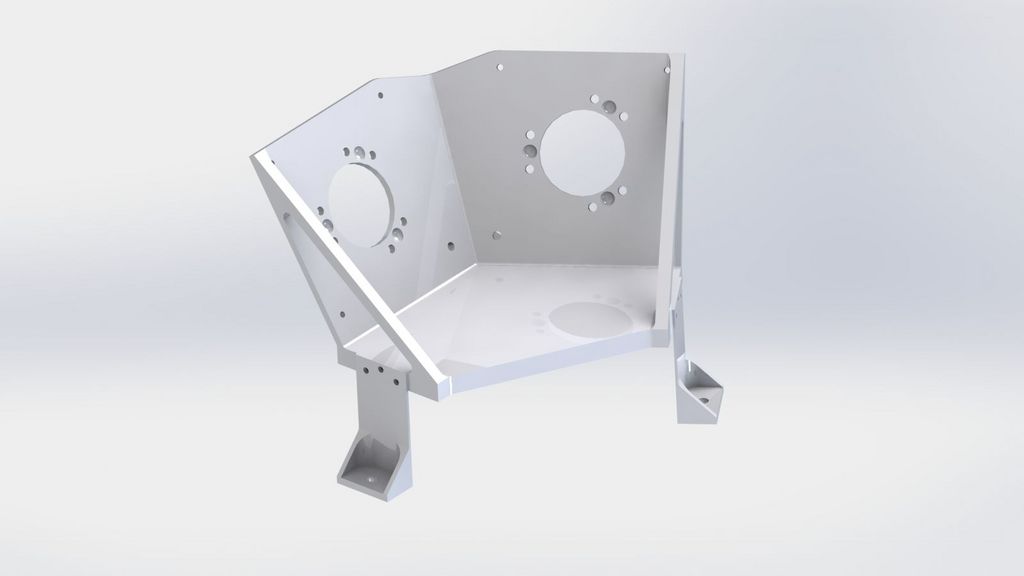
Konventionellt tillverkat CHU-fäste
Hur skapas CHU Bracket med Laser Metal Fusion?
Generellt kräver utvecklingen inom flyg- och rymdindustrin mer kostnadseffektiva, komplexare och effektivare komponenter. Mot bakgrund av de argumenten har den additiva tillverkningen av CHU-fästet många fördelar. Du har fördel av hög designfrihet när det gäller komplexa designer. Detta är särskilt användbart vid avvikelse från standardgeometrier som bioniska strukturer. Designen för CHU-fästet konstruerades från scratch, topologiskt optimerad för additiv tillverkning. Tre Camera Head Unit Brackets skrevs ut samtidigt på substratplattan med en TruPrint 3000-anläggning. Tillverkningen av en komponent med TruPrint 3000 tar ungefär sex timmar. Om den skrivs ut på en TruPrint 5000 minskas byggtiden till ungefär 2,5 timmar. Mer data och fakta om komponenten finns längst ner på den här sidan. På byggplattan fanns samtidigt prover för kvalitetssäkring. Elektrokemisk polering och värmebehandling för statiska och modala analyser krävdes inte längre eftersom en optimering av de mekaniska materialegenskaperna genomfördes med materialbytet.
Boka rådgivning!
Du har en komponent som du vill tillverka genom additiv tillverkning? Vill du veta hur stor besparingspotentialen är och vilka fördelar som kan förverkligas med additiv tillverkning? Då ska du kontakta oss och boka ett rådgivningsmöte med våra experter.
Data & fakta om komponenten
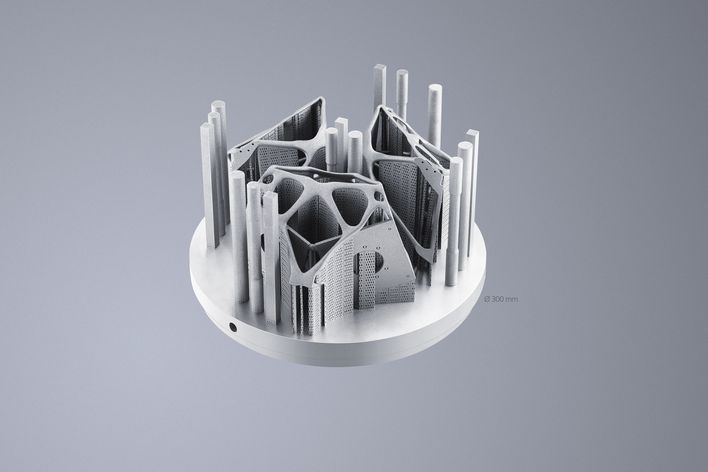
- Komponentmått: 112 mm x 160 mm x 128 mm
- Byggtid (per komponent/substratplatta): ca 6 timmar (TruPrint 3000), 2,5 timmar (TruPrint 5000)
- Byggtid totalt (alla komponenter/substratplatta): 18 timmar (TruPrint 3000), 7,5 timmar (TruPrint 5000)
- Skikttjocklek: 60 µm
- Antal skikt: 2 155
- Bygghastighet: 9 626 cm³/h
- Vikt: 150 746 g
- Volym: 57 757 cm³
- Kund: Institut för Rymdsystem vid Universitet Stuttgart universitet och Institut för konstruktionskoncept och strukturteknologi vid Tyskt Centrum för flyg- och rymdindustrin (DLR)